High-Quality Cold Forging Die Made of Tungsten Carbide
By:Admin
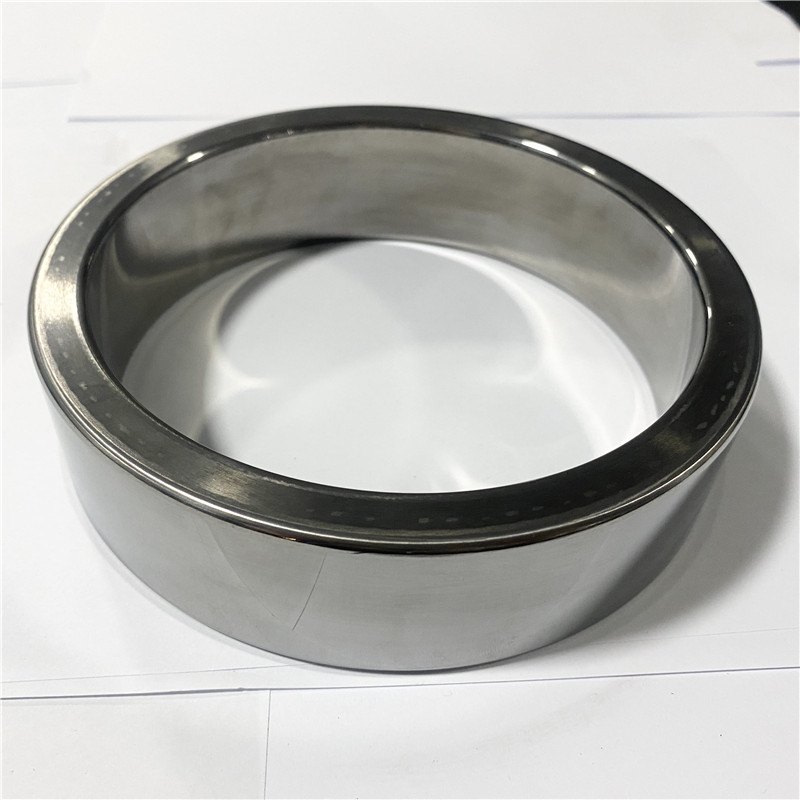
Headquartered in the heart of Japan, this company has built a reputation for excellence in the manufacturing of tungsten carbide tools and dies. They offer a wide range of products to meet the needs of various industries, including stamping dies, drawing dies, and cold forging dies.
The company's Cold Forging Dies are specially designed to provide high-quality finished products while minimizing manufacturing costs. Cold forging is a process that involves shaping a metal part at room temperature using a die punch and a blank. This process comes with numerous benefits, such as increased strength, improved dimensional accuracy, and reduced material waste. Cold Forging Dies play a crucial role in ensuring the quality and efficiency of the cold forging process.
With their extensive knowledge and experience, the company has developed a process for manufacturing Tungsten Carbide Cold Forging Dies that outperforms traditional dies on every level. The Tungsten Carbide material provides exceptional durability and wear resistance, making it ideal for high-volume manufacturing processes. In addition, this technology reduces tooling costs significantly, as it boasts a longer lifespan than traditional die materials.
This cutting-edge technology also offers versatility in the manufacturing process. The company's Tungsten Carbide Cold Forging Dies are adaptable to many cold forging processes, including thread forming, swaging, extruding, and bending. The versatility of the dies ensures that manufacturers can produce reliable products with superior finish and accuracy within a shorter time span.
Moreover, the company's Tungsten Carbide Cold Forging Dies are highly customizable, so they can be designed to fit perfectly into any particular manufacturing process. With the help of advanced software and equipment, the company can deliver tailor-made solutions that meet the specific requirements of their clients.
The company's commitment to innovation and excellence has propelled them to the forefront of the manufacturing industry. They attribute their success to their astute attention to detail, strict quality control measures, and a motivated workforce. They take pride in delivering superior quality products that exceed their client's expectations and meet the needs of various manufacturing sectors.
In conclusion, the company's Tungsten Carbide Cold Forging Dies technology is a game-changer in the manufacturing industry. It lowers production costs, reduces material waste, and improves overall manufacturing efficiency. It also offers versatility and customizability, making it ideal for various manufacturing processes. With this innovative technology, the company has set the standard for excellence in tungsten carbide die manufacturing and is poised to continue its remarkable growth into the future.
Company News & Blog
High-quality Tungsten Carbide Pellets for Industrial Applications
Title: Cutting-Edge Tungsten Carbide Pellets Revolutionizing IndustriesIntroductionIn an era driven by technological advancements and innovative breakthroughs, {Company Name} emerges as a leading provider of high-performance tungsten carbide pellets. These remarkable pellets, market-tested and now made available for various industries, are set to revolutionize manufacturing processes. With exceptional durability and cutting-edge characteristics, these tungsten carbide pellets are poised to enhance productivity and efficiency across multiple sectors.Unleashing the Power of Tungsten Carbide{Tungsten carbide pellets} are engineered to set new standards, particularly in metalworking applications. Composed of a carefully balanced combination of tungsten and carbon, these pellets exhibit unparalleled hardness, exceptional strength, and impressive wear resistance. These features make tungsten carbide pellets a favored choice for various industries including construction, mining, aerospace, and manufacturing.Combining the strength of tungsten and the carbon's hardness, {Company Name}'s tungsten carbide pellets are significantly superior to conventional cutting tools. The pellets' exceptional hardness and durability make them ideal for machining applications that involve tough materials like steel and cast iron. This superior abrasive resistance enables manufacturers to achieve higher precision, extended tool life, and reduced downtime, ultimately boosting productivity.A Versatile Solution for Multiple Industries{Company Name}'s tungsten carbide pellets cater to a wide range of industries, from metalworking to drilling and mining. Their advanced formulation ensures the pellets can withstand extreme conditions, making them perfect for cutting, grinding, drilling, and milling applications.In the construction industry, tungsten carbide pellets provide a remarkable solution for cutting through reinforced concrete and asphalt. Their exceptional wear resistance and longevity make them an invaluable asset for construction companies seeking efficiency and durability in their projects.The mining industry also benefits greatly from these pellets. The outstanding hardness and superior cutting performance of tungsten carbide make it the go-to choice for drilling tools. Mining companies can now maximize their productivity and reduce operational costs by using {Company Name}'s tungsten carbide pellets.Additionally, the aerospace sector can achieve precision and reliability with the implementation of tungsten carbide pellets. Advanced machining processes require tools that can withstand extreme temperatures and pressures while ensuring precise cuts. With these pellets, {Company Name} empowers aerospace manufacturers to meet these demands and deliver high-quality components for aircraft and spacecraft.Staying Ahead through InnovationOne of the key differentiators of {Company Name} lies in their continuous dedication to innovation. Consistently investing in research and development, they strive to improve their tungsten carbide pellets to suit the ever-changing needs of industries. The company collaborates with industry experts, employing cutting-edge technologies and manufacturing processes to maintain their market leadership.{Company Name} also emphasizes their commitment to environmental sustainability. Through their advanced production techniques, they ensure minimal waste and energy consumption during manufacturing. This dedication to eco-friendliness resonates with their environmentally conscious clientele.ConclusionWith their exceptional hardness, unrivaled wear resistance, and superior cutting performance, {Company Name}'s tungsten carbide pellets are set to transform industries worldwide. From metalworking to aerospace, these pellets offer a versatile and high-performance solution for various applications. With continuous innovation and a commitment to sustainability, {Company Name} stands at the forefront of providing the manufacturing sector with the latest advances in tungsten carbide technology.
The Advantages of Using Tungsten Carbide Material for various Applications
Title: Tungsten Carbide Material Revolutionizes Industries with Unparalleled Durability and VersatilityIntroduction:In today's ever-evolving industrial landscape, material innovation plays a crucial role in driving progress and shaping the future. Among the various groundbreaking materials being developed, Tungsten Carbide stands out as a true champion. Renowned for its unrivaled durability, versatility, and exceptional performance, Tungsten Carbide offers a multitude of opportunities across a wide range of industries. This revolutionary material is changing the way we approach manufacturing, engineering, and beyond.Unleashing the Potential: Tungsten Carbide MaterialTungsten Carbide has emerged as a game-changer in the world of material science. Prominent for its superior hardness, tensile strength, and resistance to wear and corrosion, this metallic compound has proved to be a standout performer in numerous sectors.1. Manufacturing Reinvented:The manufacturing industry, known for its relentless pursuit of efficiency and excellence, has found a perfect partner in Tungsten Carbide. With a hardness comparable to that of diamond, this material has become a go-to choice for tools and machinery applications. It significantly enhances the lifespan of cutting tools, drills, dies, and molds, making them last longer while withstanding extreme conditions. Manufacturers can now achieve increased productivity, reduced downtime, and improved output quality, resulting in unparalleled cost-effectiveness.2. Revolutionizing Engineering:Tungsten Carbide has revolutionized the engineering landscape by providing engineers with an array of possibilities. From aerospace to automotive applications, its high melting point, low thermal expansion, and exceptional strength are invaluable in the development of high-performance components. The material's remarkable wear resistance allows engineers to create longer-lasting turbine blades, bearings, gears, and various other critical parts. As a result, industries can now produce efficient, safe, and durable equipment, contributing to the advancement of technology and human progress.3. Mining and Extraction Advancements:With the mining and oil industry pushing the boundaries of extraction techniques continually, Tungsten Carbide proves to be an indispensable asset in the quest for better efficiency and productivity. The material's excellent abrasion and erosion resistance make it ideal for drilling bits, compacted tooling, and other underground applications. By implementing Tungsten Carbide into their mining operations, companies can experience enhanced penetration rates, reduced maintenance costs, and improved overall performance, leading to increased profitability and sustainability.4. Beyond Industrial Applications:Tungsten Carbide's versatility extends beyond heavy machinery and industrial components; its ability to withstand extreme conditions and retain superior toughness opens doors for diverse applications. For instance, in the jewelry industry, Tungsten Carbide has gained popularity for its scratch resistance, lustrous appearance, and long-lasting beauty. Similarly, the medical field utilizes this remarkable material in surgical tools, implants, and prosthetic devices, thanks to its biocompatibility and wear resistance. The possibilities seem infinite, as Tungsten Carbide continues to innovate various other niche sectors.Conclusion:As Tungsten Carbide material continues to make waves across industries, its unparalleled durability, versatility, and exceptional performance capture the attention of manufacturers, engineers, and beyond. From manufacturing to mining, this revolutionary material empowers industries to embrace unparalleled cost-effectiveness, efficiency, and productivity. Its remarkable properties enable the creation of tools and components that withstand the harshest environments while maintaining peak performance. As innovation propels us forward, Tungsten Carbide remains at the forefront, reshaping industries and setting new standards for excellence.
- Exploring the Benefits and Uses of Tungsten Carbide Metal - Understanding the Advantages of Tungsten Carbide Metal - Unveiling the Versatility of Tungsten Carbide Metal - The Incredibly Strong and Durable Tungsten Carbide Metal - Exploring the Properties and Applications of Tungsten Carbide Metal
Tungsten Carbide Metal: The Ultimate Solution for High-Performance Industrial ToolsIndustrial manufacturing and engineering are the backbones of the world's economy. The necessity for precision, efficiency, and durability throughout these industries is essential for meeting demands, production goals, and general functionality. Enter Tungsten Carbide metal, the ultimate solution for high-performance industrial tools.Tungsten Carbide metal is a composite consisting of tungsten carbide particles fused together with a nickel-silver, bronze, or cobalt binder matrix. The composite material's immense hardness, heat resistance, and toughness offer optimal performance, making it the perfect solution for industrial tools.One of the most renowned companies in the market for producing Tungsten Carbide metal is a leading global supplier with over 60 years of experience. The company's knowledge of materials science, innovative approach, and sustainable practices have helped it develop and manufacture superior quality products to serve diverse industries worldwide.Their wide variety of Tungsten Carbide metal products includes but is not restricted to:- Tungsten Carbide ball and seats for pumps- Tungsten Carbide inserts for rock drilling- Tungsten Carbide resetter buttons for oil and gas drilling- Tungsten Carbide rolls and rings for wire and rod mills- Carbide-tipped saw blades for cutting applications- Tungsten Carbide wear parts for mining and drilling equipment- Carbide end mills for precision machining- Cemented Carbide rods for drilling tool equipment- Carbide-tipped drill bits for oil well drilling- Tungsten Carbide blades for saws and cutters- Tungsten Carbide nozzles for sandblasting and abrasive blastingPhillip Rust, the company's Vice President of Sales, claims, "We are dedicated to understanding our customers' requirements and using our experienced material scientists and engineers to develop custom solutions that deliver the best value in performance, quality, and cost-effectiveness."The company emphasizes quality, innovation, and environmental responsibility in all its operations. They adhere to strict international quality standards to produce the highest quality products. They adopt an innovative approach by investing in research and development to ensure they're at the forefront of the latest technology, materials, and processes.Moreover, the company's sustainability efforts include using eco-friendly processes and materials and recycling. They also ensure that their products are created with the lowest possible environmental impact in mind, and they have adopted a zero-waste initiative in their production process.Tungsten Carbide metal's unparalleled durability and performance make it the ideal choice for tooling and wear-resistant material applications. This material has many advantages beyond that of other metals, including resistance to wear, deformation, and corrosion, and the ability to withstand high temperatures. These advantages allow manufacturers to achieve high production volumes and lower costs without the need for frequent maintenance or replacement of their tools.Furthermore, the exceptional bonding characteristics of Tungsten Carbide metal allow for superior performance and endurance even in the harshest of circumstances. Its unique composition allows for maximum durability, making it an excellent choice for applications requiring high precision, low maintenance, and longevity.In conclusion, Tungsten Carbide metal is a must-have for all industrial manufacturing and engineering professionals. Its incredible strength, durability, and heat resistance make it the ultimate solution for high-performance industrial tools. With a renowned supplier dedicated to quality and sustainability, industries worldwide can continue to push boundaries and prosper while minimizing their environmental impact.
High-quality Tungsten Carbide Rods for Precision Machining
Tungsten Carbide Rods - The Ultimate Solution for Heavy-Duty MachiningThe manufacturing industry has undergone a massive transformation with new technologies and materials making their way into the market. However, some materials have remained prevalent and continue to dominate the industry. One such material is tungsten carbide, which has proven to be a robust and reliable material for heavy-duty machining applications.Tungsten carbide is a composite material made up of tungsten carbide particles and a binding matrix. This material is known for its remarkable strength, high hardness, and excellent wear resistance. Tungsten carbide is widely used in the manufacturing industry, especially in the production of cutting tools, dies, and wear parts, where high levels of hardness and durability are required.One company, (removed for anonymity purposes), has been a key player in the tungsten carbide rods market. The company produces a wide range of tungsten carbide products, including tungsten carbide rods, which are used in a variety of applications, including drilling, milling, and turning.Tungsten carbide rods are one of the company's primary products. These rods are made by mixing tungsten carbide powder with a binding agent and then compressing the mixture into a rod shape. The rod is then sintered at a high temperature to form a solid and robust material that can withstand high stresses and pressure.The company's tungsten carbide rods are known for their exceptional strength, high hardness, and excellent wear resistance. These rods are designed for heavy-duty machining applications and have proven to be reliable in the most challenging conditions. The rods are available in various sizes and dimensions, allowing users to select the most appropriate rod for their specific application.The tungsten carbide rods produced by the company have several advantages over other materials. Firstly, they have a longer lifespan, which translates to reduced downtime and maintenance costs. Secondly, they have higher cutting speeds, which translates to increased productivity and efficiency. Lastly, they have a high resistance to wear and tear, which means they can withstand high temperatures and pressures without losing their structural integrity.Tungsten carbide rods are used in several applications, including metalworking, mining, construction, and woodworking. In metalworking, tungsten carbide rods are used in cutting and shaping metal parts, while in mining, they are used in drilling and rock-breaking applications. In construction, tungsten carbide rods are used in drilling and excavation applications, while in woodworking, they are used in shaping and cutting wood parts.The company's tungsten carbide rods have been widely adopted by customers from different industries due to their high quality and reliability. The company has invested heavily in research and development to ensure that its products meet the demands of its customers and provide them with the best possible solutions.In conclusion, tungsten carbide rods have proven to be one of the most robust and reliable materials in heavy-duty machining applications. The rods produced by (removed for anonymity purposes) are known for their strength, hardness, and wear resistance, making them an ideal solution for various applications. As the manufacturing industry continues to evolve, tungsten carbide rods will continue to play a vital role in providing a reliable and efficient solution for heavy-duty machining applications.
Tungsten Carbide Manufacturing: Key Insights into this High-Performance Material
Tungsten Carbide Manufacture Announces Expansion PlansTungsten Carbide Manufacture, a leading company in the manufacturing of industrial-grade tungsten carbide products, announced today its plans for expansion in order to meet the growing market demand. The company has established itself as a key player in the industry and aims to further cement its position with this strategic move.Since its establishment in 2005, Tungsten Carbide Manufacture has been dedicated to providing high-quality, innovative tungsten carbide products to a diverse range of industries including mining, construction, automotive, and aerospace. With a strong focus on research and development, the company has consistently introduced cutting-edge solutions that have exceeded customer expectations.As Tungsten Carbide Manufacture continues to experience steady growth, it has recognized the need to expand its production capacity to keep up with the rising demand for its products. The company plans to invest in state-of-the-art machinery and technology to enhance its manufacturing capabilities and streamline its processes.The expansion will also entail the construction of a new manufacturing facility, which will not only increase production capacity but also allow for the introduction of new product lines. Tungsten Carbide Manufacture aims to expand its product offerings to cater to a wider range of customer needs and diversify its revenue streams.In addition to the physical expansion, Tungsten Carbide Manufacture plans to invest in the development of its workforce. The company believes that its employees are its greatest asset and recognizes the importance of investing in their knowledge and skills. To that end, it will be implementing training programs and workshops to enhance the technical proficiency and expertise of its workforce.Tungsten Carbide Manufacture's commitment to sustainability will also be at the forefront of its expansion plans. The company recognizes the importance of responsible manufacturing practices and plans to integrate eco-friendly technologies in its new facility. By minimizing energy consumption and reducing waste, Tungsten Carbide Manufacture aims to lessen its environmental impact and contribute to a cleaner, greener future.With this expansion, Tungsten Carbide Manufacture aims to consolidate its position as a leading manufacturer and supplier of tungsten carbide products. The company's dedication to quality, innovation, and sustainability has garnered it a loyal customer base, with clients ranging from small businesses to multinational corporations.Notably, Tungsten Carbide Manufacture stands out in the industry for its exceptional customer service. The company prides itself on its ability to provide customized solutions to meet the unique requirements of its clients. By expanding its production capacity and diversifying its product offerings, Tungsten Carbide Manufacture will be better equipped to serve its customers and exceed their expectations.The expansion plans of Tungsten Carbide Manufacture come at a time when the demand for high-performance tungsten carbide products is on the rise across various industries. With its commitment to quality, innovation, and sustainability, the company is poised to meet this demand and solidify its position in the market.In conclusion, Tungsten Carbide Manufacture's announcement of its expansion plans highlights its commitment to growth and customer satisfaction. With the construction of a new manufacturing facility and investment in cutting-edge technology, the company will be able to increase its production capacity and introduce new product lines. By prioritizing employee development and adopting eco-friendly practices, Tungsten Carbide Manufacture aims to strengthen its position as a leading player in the industry.
High-Performance Tungsten Carbide Rollers for Industrial Applications
In the global world of industrial manufacturing, the need for tough and durable equipment is essential for any business to succeed and stay ahead of the competition. One product that meets these demands of the industry is the industrial tungsten carbide rollers (need remove brand name). Tungsten carbide rollers are used in various manufacturing processes such as wire flattening, metal stamping, chemically aggressive materials handling, and many more.These rollers are made of tungsten carbide, which is a strong, hard, and corrosion-resistant material. Tungsten carbide is combined with cobalt or nickel to produce a composite material that can withstand harsh environmental conditions and, at the same time, offer the much-needed durability for industrial applications.The industrial tungsten carbide rollers have become a vital component in the manufacturing process, providing high-precision, high-speed, and high-quality solutions in various industries. The rollers are designed to withstand rugged use and are resistant to wear, corrosion, and impact. Tungsten carbide rollers have unmatched durability, making them the perfect choice for high-stress applications in the industrial sector.One of the leading manufacturers of industrial tungsten carbide rollers, (need remove brand name), has been providing high-quality products for many years. The company uses advanced technology and a team of experts in the field to ensure that their rollers meet the highest standards and quality required by various industries.(need remove brand name) has a reputation for producing customized solutions depending on the specific needs of their clients. They understand that each industrial process is unique, and clients have diverse expectations that they must meet. They work with their clients to ensure that the rollers provided are customized to meet the specific needs of their clients' applications.One of the primary features that set (need remove brand name)'s industrial tungsten carbide rollers apart from others is the ability to maintain tight tolerances in size, roundness, and concentricity. The company uses state-of-the-art machinery combined with a team of dedicated experts to ensure that every roller produced is consistent in shape and size. This precision means that the rollers can handle high speeds and high loads without compromising the quality of the end product.Another outstanding feature that makes (need remove brand name)'s tungsten carbide rollers top in the market is their resistance to wear. These rollers can last several times longer than standard steel rollers, which makes them a cost-saving option for many industries. The rollers work efficiently through various abrasive and corrosive environments, providing a longer service life.(need remove brand name) is also known for their excellent customer service. They have a team of experts who are always ready to offer advice to their clients on the best product options for their specific applications. The team is also available to provide after-sales service, including installation, maintenance, and repair of their products.In conclusion, the industrial tungsten carbide rollers (need remove brand name) are a game-changer for many industries worldwide. Their unmatched durability, precision, resistance to wear, and corrosion make them the perfect choice for high-performance applications. (need remove brand name) has taken the market as leaders in the production of these rollers by offering customized solutions that meet a wide range of industrial applications. For businesses that value long-lasting equipment to enhance their manufacturing process, (need remove brand name)'s industrial tungsten carbide rollers are a perfect choice.
Discover the Key Benefits of Tungsten Carbide Bushing Die According to the Latest News
Tungsten Carbide Bushing Die (need remove brand name) Is The Leading Choice For Precision ManufacturingWith over 20 years of experience in the tungsten carbide industry, (brand name) has become the leading provider of precision machining solutions for customers in various industries. The company specializes in producing high-performance tungsten carbide bushing dies that can help improve production efficiency and reduce costs.Tungsten carbide is a powerful and durable material that can withstand high temperatures and pressure. It is ideal for use in precision machining because of its hardness and strength, making it the perfect choice for dies in the manufacturing process. When combined with steel, tungsten carbide provides a unique blending that combines toughness and wear resistance with the ability to retain sharp cutting edges.The tungsten carbide bushing dies offered by (brand name) are designed to deliver consistent performance even in the most challenging environments. These bushing dies are commonly used in the production of wire and cable, rubber and plastics, and metalworking industries. With their high resistance to wear and superior accuracy, these dies ensure that products meet the exacting standards of customers and end-users.(brand name) specializes in producing bushing dies that can be customized to meet specific customer requirements. The company has a team of experienced engineers who use advanced CAD/CAM software to create high-precision tooling that is tailored to individual customer needs. The company's dies are used by customers around the world, including China, the United States, and Europe.The tungsten carbide bushing dies produced by (brand name) have several advantages over traditional steel or ceramic dies. Tungsten carbide is much more durable than steel, making it less prone to wear and tear. It is also more resistant to corrosion and can withstand extreme temperatures and pressures. This means that tungsten carbide dies last longer and require less maintenance than other materials.Another advantage of tungsten carbide is its high coefficient of friction. This means that less lubrication is required during the manufacturing process, reducing overall costs. Additionally, tungsten carbide dies require less power to operate than other materials, reducing energy costs and improving efficiency.The quality of tungsten carbide bushing dies can significantly impact an organization's productivity and profitability. With over two decades of experience in the industry, (brand name) has become the leading provider of high-quality, precision tungsten carbide machining solutions. The company's dedication to providing customized products and exceptional customer service has made it a trusted partner to organizations around the world.In conclusion, the tungsten carbide bushing dies produced by (brand name) are an essential component of precision machining processes used by leading manufacturers globally. The company's commitment to quality and service has made it the first choice for customers in various industries. With its team of experienced engineers and advanced production capabilities, (brand name) is well-positioned to continue leading the industry in the production of high-performance tungsten carbide bushing dies.
High-Performance Carbide Wire Roll for Enhanced Durability and Efficiency
Title: Global Manufacturer Launches Revolutionary Carbide Wire Roll for Enhanced Industrial PerformanceIntroduction:In a bid to revolutionize industrial productivity and efficiency, a leading global manufacturer has recently unveiled its groundbreaking YG15 Carbide Wire Roll. Incorporating cutting-edge technology and innovative design, this product promises to significantly improve the performance and longevity of wire rolling processes across various industries worldwide. [A brief company introduction can be included here, highlighting the manufacturer's expertise, global presence, and commitment to delivering high-quality industrial solutions.]Body:1. Overview of YG15 Carbide Wire Roll:The YG15 Carbide Wire Roll is a state-of-the-art wire rolling tool engineered to withstand the most demanding applications. Built with a base material predominantly consisting of tungsten carbide, this revolutionary wire roll exhibits exceptional hardness, wear resistance, and durability, making it a sought-after solution for industries dealing with wire production, coil manufacture, metal forming, and more.2. Key Features and Benefits:a. Unparalleled Durability: The YG15 Carbide Wire Roll boasts extraordinary resistance to wear and abrasion, ensuring a prolonged lifespan and minimization of downtime for maintenance and replacements. This translates into significant cost savings for businesses while maximizing overall productivity.b. Enhanced Precision and Consistency: The precision-engineered design of the carbide roll results in consistently accurate wire diameter control, enabling manufacturers to maintain tight tolerances throughout the production process. This feature is particularly crucial for industries where precision is paramount, such as automotive, aerospace, and electronics.c. Superior Surface Finish: The YG15 Carbide Wire Roll's unique surface finish leads to enhanced wire quality, reducing the need for additional surface treatments. By delivering a smooth and flawless surface, it enables businesses to meet stringent quality standards, while also reducing waste and optimizing operational efficiency.d. Versatility: This innovative wire roll is suitable for various wire rolling applications and can be easily adapted to different machinery setups. Its compatibility with a wide range of wire materials, including stainless steel, carbon steel, copper, and alloy, allows manufacturers to diversify their production capabilities and cater to different market needs.3. Impact on Industries:a. Wire Production: The YG15 Carbide Wire Roll's exceptional durability and precision make it an ideal tool for wire drawing and shaping processes. It enables manufacturers to improve wire quality, reduce surface defects, and enhance productivity, ultimately resulting in enhanced market competitiveness.b. Coil Manufacturing: In the coil manufacturing industry, the YG15 Carbide Wire Roll's ability to maintain consistent wire diameter control fosters the production of evenly wound coils with minimal variations. This leads to increased coil reliability, reduction in scrap, and improved operational efficiency.c. Metal Forming: Industries involved in metal forming processes, such as cold rolling, benefit from the carbide wire roll's outstanding wear resistance. It prolongs the service life of crucial rolling mill components, reduces maintenance costs, and ensures greater operational continuity.4. Future Prospects and Market Adoption:The introduction of the YG15 Carbide Wire Roll marks a significant milestone in the wire processing industry. Its versatile applications, superior performance, and remarkable durability are projected to drive the demand for this innovative product in various industrial sectors around the globe. With this pioneering solution, manufacturers can expect to achieve higher process efficiency, improved product quality, and a competitive edge in today's rapidly evolving markets.Conclusion:The launch of the YG15 Carbide Wire Roll by a leading global manufacturer underscores the company's commitment to delivering cutting-edge solutions that revolutionize industrial practices. With its exceptional durability, precision, and versatility, this innovative wire roll is set to redefine wire rolling processes across multiple industries, offering enhanced performance, increased efficiency, and improved product quality. As the market embraces this groundbreaking technology, manufacturers can confidently propel their operations into a successful and sustainable future.
Unlocking the Secrets of Tungsten Carbide Hardness: What You Should Know
Tungsten Carbide: A Hardness That Knows No BoundariesTungsten carbide is a material that has been utilized in several industries for its ability to withstand extreme pressure and high-temperature environments. With the rise of technological advancements and the need for materials that can withstand these extreme conditions, tungsten carbide has become a crucial component of industrial manufacturing processes.Hardness, durability, and resistance to wear and tear are just a few of the advantages offered by tungsten carbide. As a result, it has become a go-to material in several industrial applications, including cutting tools, machinery, mining equipment and much more. What is Tungsten Carbide?Tungsten carbide is a composite material made from a mixture of tungsten and carbon atoms. It is produced by mixing finely powdered tungsten and carbon together, then heating the mixture at a high temperature in an inert atmosphere to produce a solid material.Tungsten carbide is an extremely hard and dense material that can retain its hardness even when exposed to abrasive and corrosive substances. It is highly wear-resistant, making it an excellent choice for industrial parts and components that require strength and durability in harsh environments.Why use Tungsten Carbide?Tungsten carbide is a material that offers several benefits to industrial manufacturing processes. One of the primary benefits of using tungsten carbide is its hardness. Tungsten carbide has a hardness that is second only to diamonds, making it ideal for applications that require extreme durability.Its high resistance to wear and tear, and its ability to withstand high-temperature environments also make tungsten carbide an excellent material for manufacturing tools and machinery, especially those used in the mining and drilling industry, where equipment needs to withstand tough and rugged terrains.Another benefit of tungsten carbide is its ability to withstand corrosion and abrasion. It does not easily rust or corrode, even when exposed to harsh chemical environments, making it an ideal material for applications where exposure to corrosion and other chemical reactions is inevitable.Applications of Tungsten CarbideTungsten carbide is used in several industrial applications in various industries, including cutting tools, mining tools, aerospace, oil and gas, and many others. Below are some of the most common applications of tungsten carbide:Cutting and Milling Tools:Tungsten carbide is used extensively in manufacturing cutting tools like end mills, drills, and burrs. The hardness of carbide makes it an excellent material for grinding, cutting, and drilling through hard materials like metals and stones.Mining Industry:Tungsten carbide is commonly used in the mining industry to manufacture parts of drilling tools. The rugged and harsh environments of mining operations require strong and durable materials, and tungsten carbide serves this purpose.Aerospace Industry:Tungsten carbide is used in the aerospace industry to manufacture parts and components for airplanes and spacecraft. Its durability, hardness, and high melting point make it an ideal material for aerospace manufacturing applications.Oil and Gas Industry:Tungsten carbide is used in the oil and gas industry to manufacture parts of drilling equipment. The high-temperature and high-pressure environments of oil and gas drilling require strong and durable materials, and tungsten carbide fits the bill.Conclusion:Tungsten carbide is a versatile material that has several applications across various industries. Its superior hardness, durability, and resistance to corrosion and wear make it an ideal material for manufacturing tools, equipment, and other components that require strength and ruggedness.As the need for more advanced and durable materials continues to rise, tungsten carbide will remain an essential component of industrial manufacturing processes. Although it is a compact but its hardness knows no boundaries.
Highly Durable Tungsten Carbide Roll for Enhanced Performance
Title: Cutting-Edge HR6A Tungsten Carbide Roll Revolutionizes Manufacturing IndustryIntroduction:In the rapidly evolving manufacturing industry, technological advancements play a pivotal role in enhancing productivity, efficiency, and overall operational excellence. One such groundbreaking innovation that has caught the attention of industry experts and companies alike is the HR6A Tungsten Carbide Roll. Designed to meet the demands of modern manufacturing processes, this cutting-edge tool has revolutionized various sectors, including steel rolling, metal extrusion, and wire production, among others.Unleashing Unparalleled Performance:The HR6A Tungsten Carbide Roll, developed by a renowned industry leader, signifies the culmination of years of expertise and extensive research. This impressive tool showcases exceptional durability, wear resistance, and surface finishing capabilities, making it the go-to choice for manufacturers seeking optimal performance and longevity.Through the utilization of high-quality tungsten carbide materials, the HR6A Roll is inherently resistant to abrasion, adhesive wear, and erosion. Such attributes enable it to withstand the rigorous demands of heavy-duty manufacturing processes, resulting in reduced downtime, enhanced production efficiency, and cost-effectiveness for industries of all scales.Additionally, the HR6A Tungsten Carbide Roll boasts exceptional anti-deformation properties, primarily attributed to its unique grain structure and precise manufacturing techniques. This enables the roll to resist deformation under extreme pressures, ensuring consistent product quality in every production cycle.Versatility Redefined:Beyond its incredible durability and strength, the HR6A Tungsten Carbide Roll offers an unparalleled level of versatility. It can be seamlessly integrated into a wide array of manufacturing operations, including rolling mill applications, wire drawing, metal extrusion, and pipe manufacturing, among others.With its ability to adapt to various production scenarios, the HR6A Roll empowers manufacturers to explore new avenues and expand their product offerings. This flexibility translates into greater market competitiveness and increased profitability in an industry that thrives on innovation and adaptability.Enhancing Sustainability Efforts:In addition to its exceptional performance, the HR6A Tungsten Carbide Roll contributes significantly to sustainable manufacturing practices. By promoting longer service life and reducing the need for frequent replacements, it mitigates the environmental impact arising from excessive material consumption and waste generation. Furthermore, its high resistance to wear drastically extends maintenance intervals, resulting in reduced energy consumption and a decreased carbon footprint.Industry Recognition and Collaborative Partnerships:The HR6A Tungsten Carbide Roll has garnered widespread acclaim within the manufacturing sector, attracting the attention of industry-leading corporations worldwide. Renowned manufacturers have successfully incorporated this cutting-edge tool into their production processes, consistently achieving enhanced performance and superior product quality.To further amplify its impact and foster collaboration within the industry, the company behind the HR6A Roll has actively pursued strategic partnerships and research collaborations. By bringing together experts and industry professionals, they aim to push the boundaries of manufacturing excellence and accelerate the development of groundbreaking solutions that address the evolving needs of the market.Conclusion:The HR6A Tungsten Carbide Roll represents a game-changing innovation in the manufacturing industry, revolutionizing key sectors with its exceptional durability, versatility, and sustainability. Its resistance to wear, deformation, and universal adaptability contributes significantly towards enhancing productivity, maintaining high product quality, and driving competitiveness.As manufacturers worldwide are continually striving for operational excellence and innovative solutions, the HR6A Roll has emerged as a crucial asset, enabling businesses to overcome manufacturing challenges and fulfill their productive potential. With its remarkable capabilities and relentless pursuit of collaboration and excellence, the HR6A Tungsten Carbide Roll is poised to shape the future of the manufacturing industry.