Durable and Efficient Cemented Carbide Cold Roller for Industrial Applications
By:Admin
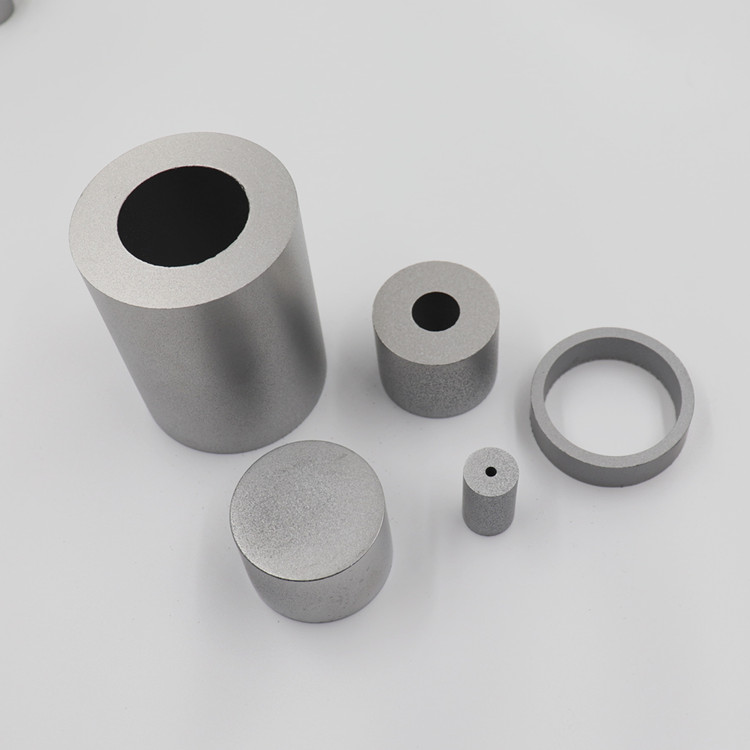
Cemented carbide cold roller is a critical component in the process of metal rolling, providing high-quality and efficient rolling solutions for various industries. This essential tool, manufactured by a leading company in the cemented carbide industry, plays a significant role in shaping and refining metal products, ensuring precise dimensions and surface finish.
The company, with decades of experience and expertise in cemented carbide production, has developed a range of cold rollers that are widely used in the production of steel, aluminum, copper, and other metal products. These rollers are engineered to withstand the extreme pressure and wear encountered during the rolling process, ensuring continuous and reliable operation.
The cemented carbide cold roller is made from high-quality raw materials, carefully selected and processed to achieve the desired mechanical properties. The use of advanced manufacturing techniques, including powder metallurgy and sintering, results in a product with exceptional hardness, strength, and resistance to wear and corrosion. As a result, the cold roller maintains its shape and performance characteristics over an extended period, minimizing downtime and maintenance costs for the end user.
In addition to the superior material properties, the company's cold rollers are precision-engineered to meet the specific requirements of different rolling applications. The rollers are available in various dimensions and configurations, allowing for customization to match the needs of individual production lines. This flexibility ensures that customers can achieve optimal results in terms of product quality and production efficiency.
The performance of the cemented carbide cold roller is further enhanced by the company's ongoing commitment to research and development. By investing in advanced technologies and collaborating with industry partners, the company continuously improves its products to meet the evolving demands of the metal processing industry. This dedication to innovation has resulted in cold rollers that offer superior performance, longer service life, and improved cost-effectiveness.
Furthermore, the company's commitment to quality extends beyond the product itself, encompassing the entire customer experience. From initial inquiry to after-sales support, the company provides responsive and personalized service to ensure customer satisfaction. By understanding the unique requirements of each customer and providing tailored solutions, the company has built strong and lasting relationships with partners and clients around the world.
The cemented carbide cold roller has established itself as a crucial component in the metal rolling industry, delivering precision, reliability, and efficiency to a wide range of applications. From shaping steel sheets for the automotive industry to producing aluminum foil for packaging, the cold roller plays a vital role in modern manufacturing processes, enabling the production of high-quality metal products that are essential to everyday life.
In conclusion, the cemented carbide cold roller, manufactured by the leading company, represents a benchmark in rolling technology, providing unmatched performance and value to its customers. With a focus on quality, innovation, and customer satisfaction, the company continues to be a trusted partner for businesses seeking efficient and reliable rolling solutions. As the metal processing industry continues to evolve, the company remains at the forefront, driving advancements in cold rolling technology and contributing to the success of its customers.
Company News & Blog
The Advantages and Applications of Cemented Carbide YG15: A Comprehensive Guide
In recent news, a cemented carbide manufacturer has made significant progress in the development of their product - YG15 (brand name removed). The YG15 cemented carbide is a highly durable and wear-resistant material that is widely used in the manufacturing industry for various components.The YG15 cemented carbide is an alloy made from a combination of tungsten carbide and cobalt powder, which is blended together and then subjected to a sintering process to produce a solid, hard-wearing material. The YG15 cemented carbide has been tested against various types of wear and tear, including abrasion, corrosion, and impact, and has been found to be highly resistant against all forms of wear and tear.One of the unique features of YG15 cemented carbide is its excellent resistance to abrasion. Abrasion is a type of wear that is caused by the rubbing or scraping of two surfaces against each other, which can result in the surface becoming rough and dull. This type of wear can be particularly problematic in industrial applications, where components are subjected to constant abrasion, leading to high levels of wear and tear.YG15 cemented carbide is also highly resistant to corrosion, which is the process of materials gradually deteriorating due to exposure to environmental factors such as moisture, temperature, and chemicals. This makes YG15 cemented carbide an ideal material for use in harsh environments, such as those found in the oil and gas industry, where components are exposed to corrosive fluids.In addition to its excellent resistance to wear and tear, YG15 cemented carbide is also known for its high strength and durability. This makes it an ideal material for use in high-stress applications, such as those found in the aerospace and automotive industries.One of the key benefits of YG15 cemented carbide is its ability to be shaped and formed into various components. This makes it a versatile material that can be used to manufacture a wide range of products, including cutting tools, wear parts, and industrial machinery components.The manufacturer of YG15 cemented carbide prides itself on producing a high-quality product that is consistently reliable and meets the needs of its customers. The company has invested heavily in research and development to ensure that its products are at the forefront of technological advancements.In addition to providing high-quality products, the manufacturer of YG15 cemented carbide places a great deal of emphasis on customer service and support. This includes providing expert advice on product selection, as well as offering technical support and troubleshooting services to help customers get the most out of their products.Overall, YG15 cemented carbide is a highly durable and wear-resistant material that is widely used in the manufacturing industry for various components. Its excellent resistance to abrasion and corrosion, as well as its high strength and durability, make it an ideal material for use in high-stress applications. With its consistent reliability and commitment to customer service and support, the manufacturer of YG15 cemented carbide is a trusted and respected name in the industry.
High-Performance Carbide Die Form Insert for Superior Accuracy and Durability
Carbide Die Form Insert: Revolutionizing the Manufacturing IndustryIn today's fast-paced manufacturing industry, companies are constantly seeking innovative solutions to improve efficiency and productivity. One notable development that has revolutionized the manufacturing industry is the introduction of carbide die form inserts. These cutting-edge tools have been widely embraced by manufacturers for their exceptional durability, precision, and performance, making them a game-changer in the world of precision tooling.Carbide die form inserts are engineered with advanced carbide materials, which offer superior hardness and wear resistance compared to traditional steel inserts. This enables the inserts to withstand the high-impact and abrasive conditions encountered in the manufacturing process, thereby extending their operational lifespan and reducing the frequency of tool replacement. As a result, manufacturers can enjoy substantial cost savings and increased productivity, as downtime for tool maintenance and replacement is significantly reduced.One of the leading companies at the forefront of producing high-quality carbide die form inserts is {}. With decades of experience and expertise in precision tooling, {} has earned a solid reputation for delivering top-notch products that meet the stringent demands of the manufacturing industry. The company's relentless commitment to innovation and quality has positioned them as a trusted partner for manufacturers seeking cutting-edge solutions for their tooling needs.The carbide die form inserts produced by {} are meticulously designed and manufactured to meet the exacting standards of precision and performance. By leveraging state-of-the-art manufacturing processes and cutting-edge technology, the company is able to produce inserts that boast exceptional dimensional accuracy and surface finish, ensuring optimal performance and consistency in the manufacturing process.Furthermore, {} offers a comprehensive range of carbide die form inserts, including standard geometries as well as custom-designed inserts tailored to the specific requirements of their customers. This flexibility allows manufacturers to optimize their tooling solutions and achieve superior results in their production processes.The benefits of using carbide die form inserts from {} are not limited to extended tool life and enhanced performance. These cutting-edge tools also contribute to improvements in overall productivity and efficiency. With reduced tool changeovers and maintenance downtime, manufacturers can maximize their operational efficiency and output, ultimately leading to significant cost savings and a competitive edge in the market.Moreover, the superior precision and surface finish achieved with carbide die form inserts contribute to the production of high-quality components, meeting the exacting standards of today's manufacturing industry. This is particularly important in industries such as aerospace, automotive, and medical device manufacturing, where precision and quality are paramount.In conclusion, carbide die form inserts have emerged as a revolutionary solution that is transforming the manufacturing industry. With their exceptional durability, precision, and performance, these cutting-edge tools have become indispensable for manufacturers seeking to stay ahead in a highly competitive market. Companies like {} are leading the way in producing high-quality carbide die form inserts, offering a wide range of solutions tailored to meet the diverse needs of manufacturers. As the demand for precision tooling continues to grow, carbide die form inserts are poised to play an increasingly pivotal role in shaping the future of manufacturing.
Durable Carbide Roll Ring for Industrial Use: A Comprehensive Guide
Carbide Roll Ring is a cutting-edge product that has revolutionized the industrial manufacturing sector. With its superior quality and exceptional durability, it has become a go-to choice for companies across various industries. The carbide roll ring is a key component in improving productivity, reducing maintenance costs, and extending the lifespan of machinery.The company behind this innovative product is a renowned leader in the field of carbide tools and wear parts. With a strong focus on research and development, they have continuously pushed the boundaries of innovation in the industry. Their commitment to delivering top-notch products and excellent customer service has earned them a sterling reputation in the market.One of the key features of the carbide roll ring is its exceptional hardness and wear resistance. This makes it ideal for use in high-stress applications, where traditional steel or iron components would quickly wear out. The roll ring's superior hardness also allows it to maintain its shape and precision for a longer period, resulting in improved product quality and reduced scrap rates.In addition to its exceptional durability, the carbide roll ring also offers excellent thermal stability. This means that it can withstand high temperatures without deforming or losing its strength, making it suitable for use in demanding manufacturing processes such as hot rolling and forging. Furthermore, its thermal stability also translates to longer maintenance intervals, reducing downtime and maintenance costs for companies.The company's dedication to quality and innovation is reflected in their state-of-the-art manufacturing facilities. Equipped with the latest technology and a team of skilled engineers, they ensure that every roll ring that leaves their factory meets the highest standards of precision and quality. This commitment to excellence has made them a trusted partner for countless major manufacturers worldwide.Another key advantage of the carbide roll ring is its versatility. It can be customized to fit a wide range of machinery and applications, making it a flexible solution for companies with diverse manufacturing needs. Whether it's for cold rolling, hot rolling, or any other specialized process, the roll ring can be tailored to meet the specific requirements of the customer.The company's dedication to environmental sustainability is also reflected in the production of the carbide roll ring. They have implemented eco-friendly processes and materials, ensuring that their products not only deliver exceptional performance but also minimize their impact on the environment. As more and more companies prioritize sustainability, this commitment to eco-friendly manufacturing is another reason why the company stands out in the market.The carbide roll ring has already made a significant impact in the manufacturing sector, with a growing number of companies reaping the benefits of this innovative product. Its ability to improve productivity, reduce maintenance costs, and enhance product quality has made it an invaluable asset for manufacturers around the world. As the industry continues to evolve, the roll ring is expected to play an even larger role in shaping the future of industrial manufacturing.In conclusion, the carbide roll ring is a game-changer for the manufacturing industry, and the company behind it continues to set the bar for excellence in the field of carbide tools and wear parts. With its exceptional durability, thermal stability, and versatility, the roll ring has become an indispensable component for companies looking to optimize their manufacturing processes and stay ahead of the competition. As the demand for high-quality, long-lasting industrial components continues to rise, the carbide roll ring is well-positioned to lead the way into a new era of manufacturing excellence.
Unlocking the Potential of YG20C: Everything You Need to Know About This Premium-Grade Alloy
Title: High-Quality YG20C Grade Tungsten Carbide: Revolutionizing Industrial ApplicationsIntroduction (112 words):In today's rapidly evolving industrial landscape, there is a constant demand for reliable, durable, and high-performing materials. In response to this need, the renowned company ***, equipped with cutting-edge technology and expertise, introduces their groundbreaking product – the YG20C grade tungsten carbide. This exceptional material is set to revolutionize various industries by offering enhanced strength, resilience, and versatility. With its unparalleled quality and reliability, YG20C grade tungsten carbide promises to redefine the notion of durability and efficiency across multiple industrial fields.Paragraph 1 (122 words):YG20C grade tungsten carbide, manufactured by ***, is an industry-leading material that is gaining significant attention for its exceptional quality and remarkable performance. The YG20C grade refers to a classification system that confirms the high level of tungsten content in the alloy, making it superior in strength and hardness. Its unique composition allows it to withstand extreme conditions, including high temperature, corrosion, wear, and abrasion.Paragraph 2 (132 words):One of the distinguishing features of the YG20C grade tungsten carbide is its versatility. With its superior physical properties, this material finds extensive applications in sectors such as metalworking, mining, petroleum, engineering, and construction. Tungsten carbide is highly valued for its remarkable resistance against wear, making it ideal for cutting tools, drilling bits, heavy machinery parts, and machinery components that endure intense wear and tear.Paragraph 3 (140 words):In addition to its exceptional toughness and durability, YG20C grade tungsten carbide also boasts excellent thermal conductivity and electrical resistivity. This unique combination of properties positions it as a highly desirable material for manufacturing precision tools, such as micro drills, circuit board drills, and tool inserts. Its ability to maintain sharp cutting edges even during prolonged usage ensures superior precision and efficiency, resulting in cost savings and improved productivity for industries relying on such tools.Paragraph 4 (134 words):Furthermore, YG20C grade tungsten carbide is also finding its way into the realm of jewelry and accessories. Its high luster and scratch-resistant nature make it an ideal choice for crafting high-quality rings, bracelets, and watch bezels. As the demand for sustainable and durable jewelry continues to grow, tungsten carbide has emerged as a popular alternative to traditional materials.Conclusion (110 words):The introduction of YG20C grade tungsten carbide by *** marks a significant milestone in the materials industry, thanks to its exceptional properties and wide-ranging applications. From heavy machinery and precision tools to jewelry, this remarkable material offers durability, strength, and versatility. As industries strive for increased efficiency and longevity, the utilization of YG20C grade tungsten carbide is poised to shape the future of manufacturing and engineering. With ***, industries can now tap into a material that provides outstanding resistance to wear, heat, and corrosion, transforming the way various sectors operate and creating a more sustainable and reliable future.
High-quality Tungsten Carbide Pellets for Industrial Applications
Title: Cutting-Edge Tungsten Carbide Pellets Revolutionizing IndustriesIntroductionIn an era driven by technological advancements and innovative breakthroughs, {Company Name} emerges as a leading provider of high-performance tungsten carbide pellets. These remarkable pellets, market-tested and now made available for various industries, are set to revolutionize manufacturing processes. With exceptional durability and cutting-edge characteristics, these tungsten carbide pellets are poised to enhance productivity and efficiency across multiple sectors.Unleashing the Power of Tungsten Carbide{Tungsten carbide pellets} are engineered to set new standards, particularly in metalworking applications. Composed of a carefully balanced combination of tungsten and carbon, these pellets exhibit unparalleled hardness, exceptional strength, and impressive wear resistance. These features make tungsten carbide pellets a favored choice for various industries including construction, mining, aerospace, and manufacturing.Combining the strength of tungsten and the carbon's hardness, {Company Name}'s tungsten carbide pellets are significantly superior to conventional cutting tools. The pellets' exceptional hardness and durability make them ideal for machining applications that involve tough materials like steel and cast iron. This superior abrasive resistance enables manufacturers to achieve higher precision, extended tool life, and reduced downtime, ultimately boosting productivity.A Versatile Solution for Multiple Industries{Company Name}'s tungsten carbide pellets cater to a wide range of industries, from metalworking to drilling and mining. Their advanced formulation ensures the pellets can withstand extreme conditions, making them perfect for cutting, grinding, drilling, and milling applications.In the construction industry, tungsten carbide pellets provide a remarkable solution for cutting through reinforced concrete and asphalt. Their exceptional wear resistance and longevity make them an invaluable asset for construction companies seeking efficiency and durability in their projects.The mining industry also benefits greatly from these pellets. The outstanding hardness and superior cutting performance of tungsten carbide make it the go-to choice for drilling tools. Mining companies can now maximize their productivity and reduce operational costs by using {Company Name}'s tungsten carbide pellets.Additionally, the aerospace sector can achieve precision and reliability with the implementation of tungsten carbide pellets. Advanced machining processes require tools that can withstand extreme temperatures and pressures while ensuring precise cuts. With these pellets, {Company Name} empowers aerospace manufacturers to meet these demands and deliver high-quality components for aircraft and spacecraft.Staying Ahead through InnovationOne of the key differentiators of {Company Name} lies in their continuous dedication to innovation. Consistently investing in research and development, they strive to improve their tungsten carbide pellets to suit the ever-changing needs of industries. The company collaborates with industry experts, employing cutting-edge technologies and manufacturing processes to maintain their market leadership.{Company Name} also emphasizes their commitment to environmental sustainability. Through their advanced production techniques, they ensure minimal waste and energy consumption during manufacturing. This dedication to eco-friendliness resonates with their environmentally conscious clientele.ConclusionWith their exceptional hardness, unrivaled wear resistance, and superior cutting performance, {Company Name}'s tungsten carbide pellets are set to transform industries worldwide. From metalworking to aerospace, these pellets offer a versatile and high-performance solution for various applications. With continuous innovation and a commitment to sustainability, {Company Name} stands at the forefront of providing the manufacturing sector with the latest advances in tungsten carbide technology.
Tungsten Carbide Bushing Grade: A Comprehensive Guide to its Properties and Applications
article:Tungsten Carbide Bushing Grade: The Ultimate Solution to Wear ResistanceWhen it comes to mechanical applications, wear resistance is a primary concern. Over time, even the strongest materials wear down, creating a need for regular maintenance or replacement. However, with the advent of tungsten carbide bushing grade, the game has changed, and wear resistance is no longer a concern.Tungsten carbide is a versatile material that combines the hardness and strength of metallic tungsten with the toughness and ductility of a carbide. With its excellent wear resistance and toughness, it is highly desirable for a range of industrial applications.One of the key applications of tungsten carbide is the production of bushings, which are critical in manufacturing and construction. Bushings play a vital role in reducing the friction and wear between machine parts, ensuring the smooth and efficient operation of machinery.The use of tungsten carbide bushing grade has revolutionized the way industrial machinery works, creating a more efficient and effective system. The tungsten carbide bushings have a high wear resistance, which leads to longer service life and reduced maintenance costs. In addition, the material has a low coefficient of friction, reducing the amount of energy needed to operate the machinery and resulting in lower operating costs.The combination of the high wear resistance and low coefficient of friction makes tungsten carbide bushing grade the ideal material for a range of industrial applications, including mining, construction, oil and gas, and manufacturing.One company that has been at the forefront of the production of tungsten carbide bushing grade is {company name}. With its state-of-the-art manufacturing facilities, the company produces high-quality tungsten carbide bushings that meet industry standards and exceed customer expectations.Founded in {year}, {company name} is a global leader in the production of tungsten carbide products, offering a wide range of products and services to customers worldwide. The company has a team of highly skilled and experienced professionals who are committed to delivering excellence in every project.In addition to its production line, {company name} provides its customers with technical support and solutions to their specific needs. The company's engineers work closely with customers to understand their needs and requirements, providing customized solutions that address their unique challenges.{Company name} has a robust quality control system that ensures all products meet the highest standards. The company uses advanced technology and equipment to test the quality and performance of its products, ensuring that only the best products are delivered to customers.The company's commitment to excellence has earned it a reputation as a leader in the industry, with customers from around the world relying on its products and services to keep their machinery running smoothly.In conclusion, tungsten carbide bushing grade is a game-changer when it comes to wear resistance in industrial applications. With its high wear resistance and low coefficient of friction, it is the ideal material for a range of industries, from mining to manufacturing.Companies like {company name} are at the forefront of the production of tungsten carbide bushings, providing high-quality products and solutions to customers worldwide. With their commitment to excellence and customer satisfaction, companies like {company name} are helping to shape the future of industrial machinery and production.
Tungsten Carbide Block: A Valuable Industrial Material for Various Applications
Tungsten Carbide Block Emerges as a Game-Changer in the Manufacturing IndustryTungsten carbide is a compound that combines tungsten and carbon, making it a highly versatile material for manufacturing a variety of products. The tough and durable nature of tungsten carbide makes it one of the most preferred materials for applications that require long durability, such as machine parts.Recent technological advancements in the manufacturing industry have given birth to a new product - the tungsten carbide block. These blocks, made from high-quality tungsten carbide, have become a game-changer in the manufacturing industry, as they offer unique properties that traditional materials cannot match.Tungsten carbide blocks are used in various industries, including construction, mining, and manufacturing. They have a wide range of applications that require high wear and abrasion resistance, such as manufacturing cutting tools, dies, and punches. These blocks offer superior performance and longevity compared to other carbide-based materials, making them the leading choice for toolmakers and manufacturers alike.One of the main advantages of tungsten carbide blocks is their ability to withstand high temperatures. The material has a high melting point, making it an ideal choice for applications that require high resistance to heat. Tungsten carbide blocks are also highly resistant to deformation, making them suitable for use in high-pressure environments.Additionally, tungsten carbide blocks exhibit exceptional hardness, providing high wear resistance, and low friction. This unique combination of properties makes the carbide block ideal for applications that require high-precision machining. Many industries, such as the oil and gas and mining sectors, have adopted tungsten carbide blocks due to their outstanding performance in harsh environments.Leading tungsten carbide block manufacturers pride themselves in producing exceptional quality blocks. They focus on using only the best raw materials and state-of-the-art technology to ensure that their blocks meet the most stringent quality standards. This quality-oriented approach has enabled manufacturers to remain the go-to source for manufacturers seeking high-quality tungsten carbide blocks.Tungsten carbide blocks come in different shapes and sizes, catering to various manufacturing applications. Manufacturers can order customized blocks tailored to their specific needs, with varying grades of tungsten carbide to suit the specific application. Additionally, manufacturers can request blocks with different surface finishes to enhance their resistance to wear and corrosion.The growing demand for tungsten carbide blocks has prompted many companies to invest in advanced technology to streamline their production processes. These investments have enabled manufacturers to produce tungsten carbide blocks faster without compromising on quality. Automation has also helped manufacturers to reduce production costs while improving their output.The adoption of tungsten carbide blocks has revolutionized the manufacturing industry, providing manufacturers with cutting-edge technology that improves production performance, longevity, and accuracy. Manufacturers in various industries now have access to a broad range of options to choose from, ensuring that they get the precise block they need for their specific applications.Moreover, by using tungsten carbide blocks, manufacturers can enhance their bottom lines by reducing their production costs and improving the quality of their products. Tungsten carbide blocks are a superior material that is cost-effective in the long run, making them an ideal choice for manufacturers who seek to maximize their profits.The future of tungsten carbide blocks looks bright, with increased investments in R&D that continue to enhance their quality, performance, and durability. Manufacturers can expect to see more advanced products that push the limits of what tungsten carbide blocks can offer.In conclusion, tungsten carbide blocks are a highly durable and versatile material that has revolutionized the manufacturing industry. With their exceptional strength, heat resistance, and wear resistance, these blocks continue to be a game-changer in many industries, providing manufacturers with a cost-effective solution that enhances their performance and bottom line. As the industry continues to invest in advanced technology, manufacturers can expect to benefit from even more innovative tungsten carbide blocks.
Discover the Benefits of Cold Rolling for Metal Manufacturing
Cold Rolling: A Revolution in Metal ManufacturingThe process of cold rolling has long been a staple in the metal manufacturing industry, but recent advancements in technology and engineering have taken this method to new heights. Cold rolling is a manufacturing process that involves shaping metal by passing it through a series of rollers at room temperature, resulting in a smoother, more uniform surface finish. This technique is commonly used in the production of sheet metal, steel, and other metal products, and has become an essential part of modern manufacturing processes.One company at the forefront of this technological revolution is {}. With a history dating back to over a century, {} has established itself as a leading manufacturer and supplier of metal products, and their innovative approach to cold rolling has set them apart in the industry.Cold rolling is a process that offers numerous advantages over traditional methods of metal shaping. One of the primary benefits is the improved surface finish of the metal, resulting in a smoother and more aesthetically pleasing appearance. Additionally, cold rolling can also impart desirable mechanical properties to the metal, such as increased strength and hardness. This makes cold-rolled products an ideal choice for a wide range of applications, from automotive components to appliances and construction materials.In recent years, {} has invested heavily in research and development to further enhance the cold rolling process. By utilizing state-of-the-art technology and cutting-edge engineering techniques, they have been able to achieve remarkable advancements in the quality and efficiency of their cold-rolled products. This has allowed {} to offer a diverse range of high-quality metal products to meet the needs of various industries and applications.One of the key factors that sets {} apart from its competitors is their commitment to sustainability and environmental responsibility. Cold rolling requires significantly less energy compared to hot rolling, making it a more eco-friendly choice for metal manufacturing. Furthermore, {} has implemented stringent quality control measures to ensure that their cold-rolled products meet the highest standards of environmental sustainability.Another aspect that sets {} apart in the industry is their dedication to customer satisfaction. By offering a wide selection of cold-rolled products, they are able to cater to the unique needs and specifications of their clients. Additionally, their team of skilled engineers and technicians work closely with customers to develop customized solutions for specific applications, ensuring that their products meet the exact requirements of each project.{}'s commitment to innovation and excellence has earned them a reputation as a trusted and reliable partner in the metal manufacturing industry. By continuously pushing the boundaries of cold rolling technology, they have positioned themselves at the forefront of the industry, setting new standards for quality, efficiency, and sustainability.The future of metal manufacturing looks promising, thanks to advancements in cold rolling technology. As companies like {} continue to push the boundaries of what is possible, we can expect to see even greater improvements in the quality and efficiency of cold-rolled products. With a strong focus on sustainability and customer satisfaction, {} is well-positioned to lead the way in this exciting new era of metal manufacturing.
High-Quality Tungsten Carbide Wear Resistant Parts from China
China Tungsten Carbide Wear Resistant Parts - A Leading Player in the IndustryChina has long been a leader in the production and distribution of tungsten carbide wear resistant parts, and one company has been making significant strides in this industry. With a strong focus on quality, innovation, and customer satisfaction, {remove brand name} has become a prominent player in the global market for tungsten carbide wear resistant parts. The company's commitment to excellence and its advanced manufacturing capabilities have set it apart from its competitors and made it a trusted name in the industry.Tungsten carbide is a durable and high-performance material that is widely used in various industrial applications, and {remove brand name} has emerged as a key supplier of high-quality tungsten carbide wear resistant parts. These parts are known for their exceptional wear resistance, hardness, and toughness, making them ideal for use in demanding and high-stress environments. {remove brand name} offers a wide range of tungsten carbide wear resistant parts, including inserts, tips, and cutting tools, which are designed to meet the specific needs of its diverse customer base.The company's success in the industry can be attributed to its relentless focus on research and development. {remove brand name} has invested significantly in cutting-edge technology and state-of-the-art manufacturing processes to ensure that its tungsten carbide wear resistant parts meet the highest industry standards. By continuously refining its production techniques and exploring new materials and designs, the company has been able to stay at the forefront of innovation and deliver superior products to its customers.In addition to its commitment to quality, {remove brand name} also places a strong emphasis on customer satisfaction. The company works closely with its clients to understand their unique requirements and provide customized solutions that meet their specific needs. Whether it's developing a new product or improving an existing one, {remove brand name} is dedicated to delivering value to its customers and building long-lasting partnerships based on trust and reliability.Furthermore, {remove brand name} has established a robust global distribution network that enables it to serve customers around the world. With a strong presence in key markets, the company is able to efficiently deliver its tungsten carbide wear resistant parts to a wide range of industries, including mining, construction, oil and gas, and manufacturing. This extensive reach, coupled with the company's unwavering commitment to quality and customer service, has helped {remove brand name} build a strong reputation as a preferred supplier of tungsten carbide wear resistant parts.Looking ahead, {remove brand name} is poised to continue its growth and cement its position as a leading player in the industry. The company remains focused on expanding its product portfolio, enhancing its manufacturing capabilities, and exploring new market opportunities to further strengthen its global presence. By staying true to its core values of quality, innovation, and customer satisfaction, {remove brand name} is well-positioned to drive the advancement of tungsten carbide wear resistant parts and set new standards for the industry.In conclusion, {remove brand name} has emerged as a key player in the global market for tungsten carbide wear resistant parts, thanks to its unwavering commitment to quality, innovation, and customer satisfaction. With a strong focus on research and development, advanced manufacturing capabilities, and a robust global distribution network, the company has established itself as a trusted supplier of high-quality tungsten carbide wear resistant parts. As {remove brand name} continues to grow and expand its reach, it is poised to lead the industry and shape the future of wear resistant parts.
Applications of Tungsten Carbide: A Versatile Industrial Material
Title: Tungsten Carbide: Revolutionizing Industries with Unparalleled VersatilityIntroduction:In the world of industrial applications, Tungsten Carbide has emerged as a game-changing material renowned for its exceptional hardness, durability, and versatility. With its remarkable properties and myriad of applications, this composite material has found its way into various industries, transforming manufacturing processes and enhancing product performance. This article delves into the multifaceted use of Tungsten Carbide and its profound impact on different sectors of the global economy.1. Automotive Industry:From precision cutting tools to durable automotive components, Tungsten Carbide is revolutionizing the automotive sector. In cutting-edge engine manufacturing, Tungsten Carbide inserts in tooling systems play a vital role in delivering precise and high-speed machining with superior surface finish. Mechanical seals made from this robust material ensure leak-free operation in automotive water pumps and ensure prolonged service life. Moreover, the use of Tungsten Carbide in brake pads and clutch facings improves braking performance and enhances durability, ensuring driver safety.2. Oil and Gas Industry:The oil and gas industry heavily relies on Tungsten Carbide due to its exceptional wear resistance and high-temperature stability. Exploration and drilling operations utilize hard-facing applications, such as drill bits, to withstand extreme working conditions while maximizing drilling efficiency. Furthermore, Tungsten Carbide components in downhole tools, such as stabilizers and wear-resistant valves, endure the challenging environment and enhance operational reliability. By offering superior resistance to erosion and corrosion, Tungsten Carbide ensures increased productivity and reduced downtime in the oil and gas sector.3. Mining and Construction:In the mining and construction sectors, where equipment operates in harsh environments, Tungsten Carbide plays a crucial role in enhancing equipment longevity and efficiency. The use of Tungsten Carbide in drill bits, augers, and tooling systems allows for improved penetration rates and extended tool life. Excavation buckets and teeth made from this material withstand abrasion from rocks and other challenging geological conditions, reducing maintenance costs and increasing productivity. The mining industry benefits greatly from the advanced performance and reliability offered by Tungsten Carbide, enabling extraction operations to occur seamlessly and efficiently.4. Metalworking and Tooling:Tungsten Carbide is widely acclaimed in the metalworking industry for its exceptional resistance to wear, deformation, and high temperatures. Cutting inserts and end mills made from this composite material offer superior cutting speed, precision, and surface finish, thereby enhancing overall machining productivity. Tungsten Carbide tooling systems also find extensive applications in the woodworking industry, where they deliver increased cutting efficiency and improved finish quality. These properties make Tungsten Carbide an indispensable choice for manufacturing sectors, guaranteeing efficiency and precision in every operation.5. Electronics and Semiconductors:In the rapidly advancing field of electronics and semiconductors, Tungsten Carbide is sought after for its electrical conductivity and resistance to wear and heat. The material is widely used in the production of semiconductor dies, integrated circuit packages, and wire bonding tools, ensuring reliable and durable electronic devices. Tungsten Carbide's remarkable electrical conductivity, coupled with its high strength, makes it an indispensable choice for electronics manufacturers.Conclusion:Tungsten Carbide's unique blend of hardness, durability, and versatility has transformed various industries and manufacturing processes worldwide. From automotive components to oil and gas equipment, mining tools to metalworking applications, and electronics to semiconductors, this exceptional material has proven to be an invaluable asset for enhancing product performance, increasing productivity, and reducing maintenance costs. As technological advancements continue to shape our world, Tungsten Carbide remains at the forefront, playing a pivotal role in shaping a more efficient and sustainable future across multiple sectors.