How Carbide Grade is Changing the Manufacturing Industry
By:Admin
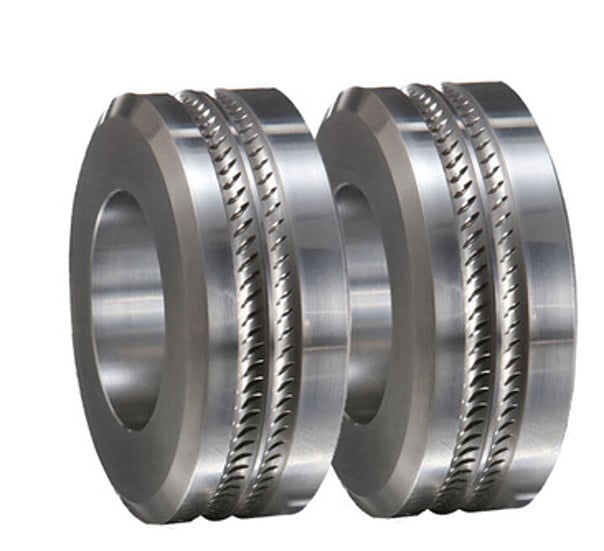
Established in [year], Carbide Grade has steadily grown its presence in the industry by leveraging its expertise in carbide tooling and its commitment to delivering top-notch products. The company's dedication to quality and performance has earned it a reputation for being a reliable and innovative supplier of carbide tools.
Carbide Grade's success can be attributed to its relentless pursuit of excellence in every aspect of its operations. From research and development to manufacturing and customer service, the company's team of professionals works tirelessly to ensure that its products meet the highest standards and provide exceptional value to its customers.
One of the company's most recent developments is the introduction of a new line of carbide grades that are designed to deliver superior performance in machining and metalworking applications. These new grades have been specifically engineered to offer improved wear resistance, tool life, and cutting performance, making them an ideal choice for companies looking to enhance their production processes.
In addition to its innovative product offerings, Carbide Grade is also known for its strong commitment to customer satisfaction. The company's team of dedicated professionals works closely with each client to understand their unique needs and provide tailored solutions that deliver the best results. This customer-centric approach has helped Carbide Grade build long-lasting relationships with its clients and establish itself as a preferred partner in the industry.
Furthermore, Carbide Grade's state-of-the-art manufacturing facilities are equipped with the latest technology and equipment, allowing the company to consistently produce high-quality carbide tools that meet the most stringent requirements. By investing in cutting-edge manufacturing capabilities, Carbide Grade is able to maintain tight quality control and ensure that its products consistently meet the highest standards.
As a forward-thinking company, Carbide Grade also places a strong emphasis on sustainability and environmental responsibility. The company has implemented various initiatives to reduce its environmental footprint and minimize waste, demonstrating its commitment to being a responsible corporate citizen.
Looking ahead, Carbide Grade is poised to continue its growth and expansion in the industry. The company remains focused on leveraging its technical expertise, commitment to quality, and customer-centric approach to further solidify its position as a leader in the carbide tooling market.
With its latest developments and unwavering dedication to excellence, Carbide Grade is well-positioned to meet the evolving needs of the machining and metalworking industries, providing innovative solutions that drive efficiency, productivity, and profitability for its clients.
In conclusion, Carbide Grade's commitment to innovation, quality, and customer satisfaction has positioned it as a trusted partner for companies seeking high-performance carbide tools. With a strong track record of success and a clear focus on the future, Carbide Grade is set to continue making a significant impact in the industry and delivering exceptional value to its clients.
Company News & Blog
Durable and Versatile Cemented Carbide Products for Various Industries
Cemented Carbide Products, a leading manufacturer of cutting tools and wear-resistant components, has been at the forefront of the industry for over 50 years. With a commitment to innovation and quality, the company has established a strong reputation for providing high-performance carbide solutions to a wide range of industries including automotive, aerospace, mining, and oil & gas.The company's extensive product line includes solid carbide end mills, drills, reamers, and indexable inserts, all of which are designed to deliver superior performance and productivity in machining applications. In addition to standard products, Cemented Carbide Products also offers custom solutions to meet specific customer requirements, providing a competitive edge in the market.With a state-of-the-art manufacturing facility and a team of experienced engineers and technicians, Cemented Carbide Products is able to produce high-quality carbide products that meet the stringent standards of the industry. The company's dedication to research and development ensures that it stays ahead of the curve, continuously introducing new and improved products to address the evolving needs of its customers.In line with its commitment to quality, Cemented Carbide Products adheres to strict quality control measures throughout the manufacturing process. From raw material procurement to final product inspection, the company ensures that each product meets the highest standards of precision and performance. This dedication to quality has earned Cemented Carbide Products various certifications and accolades, further cementing its position as a trusted supplier in the industry.Furthermore, Cemented Carbide Products takes pride in its sustainable manufacturing practices, minimizing its environmental impact through energy-efficient processes and responsible waste management. The company is committed to operating in an environmentally friendly manner, reflecting its dedication to corporate social responsibility.In addition to its focus on quality and sustainability, Cemented Carbide Products places a strong emphasis on customer satisfaction. The company works closely with its clients to understand their unique requirements and provide them with tailored solutions that meet their specific needs. By fostering strong partnerships with its customers, Cemented Carbide Products ensures that it delivers value beyond just its products, setting itself apart as a reliable and responsive business partner.As part of its continuous growth and expansion, Cemented Carbide Products has recently announced plans to invest in new technologies and equipment to further enhance its manufacturing capabilities. The company aims to capitalize on the latest advancements in the industry to develop cutting-edge carbide solutions that offer superior performance and cost-efficiency.With its unwavering commitment to excellence, sustainability, and customer satisfaction, Cemented Carbide Products remains a leader in the carbide products industry. The company's dedication to innovation and quality positions it for continued success in meeting the evolving needs of its clients and driving the industry forward. As it looks to the future, Cemented Carbide Products is poised to remain at the forefront of the industry, delivering cutting-edge solutions and driving the growth and success of its customers.
High Performance Cemented Carbide Cold Heading Die: A Game Changer in Manufacturing
Cemented Carbide Cold Heading Die Revolutionizes Manufacturing IndustryIn the world of manufacturing, precision and durability are paramount. As technology continues to evolve, so too must the tools and equipment used throughout the industry. This is where cemented carbide cold heading dies come into play, revolutionizing the way manufacturers produce high-quality components for a wide range of products.One company at the forefront of this innovation is [company name]. With a rich history dating back to 1985, [company name] has established itself as a leading manufacturer of cemented carbide cold heading dies and other precision tools. The company's commitment to quality and innovation has earned it a reputation as a trusted and reliable partner for manufacturers around the world.So, what exactly is a cemented carbide cold heading die, and how does it impact the manufacturing industry? In simple terms, a cold heading die is a tool used to form metal parts and components through a process known as cold heading. This involves shaping and forming metal wire or rod material at room temperature using a punch and die set. The result is a precise and complex component that meets the high standards of the industry.Cemented carbide, also known as hard metal, is a composite material that is particularly well-suited for cold heading dies. It is made up of tungsten carbide grains bound together by a cobalt matrix, resulting in a material that is incredibly hard and wear-resistant. This makes cemented carbide an ideal choice for manufacturing tools, as it can withstand the high pressures and abrasion that occur during the cold heading process.One of the key advantages of using cemented carbide cold heading dies is their longevity and durability. Unlike traditional steel dies, cemented carbide dies can last significantly longer without needing to be replaced or refurbished. This not only saves manufacturers time and money but also ensures a more consistent and reliable production process.Furthermore, cemented carbide cold heading dies offer a level of precision and intricacy that is unmatched by other materials. This allows manufacturers to produce more complex and high-quality components, meeting the increasingly stringent demands of modern manufacturing processes. From automotive parts to electronic components, the use of cemented carbide cold heading dies has had a significant impact across a wide range of industries.In addition to their durability and precision, cemented carbide cold heading dies also contribute to a more sustainable and efficient manufacturing process. By reducing the need for frequent die changes and maintenance, manufacturers can minimize their environmental impact and improve their overall production efficiency. This is an important consideration in an industry that is increasingly focused on sustainability and responsible manufacturing practices.For [company name], the development and production of cemented carbide cold heading dies is not just a business, but a passion. The company's team of experienced engineers and technicians are dedicated to pushing the boundaries of what is possible in the manufacturing industry. Through continuous research and development, [company name] aims to stay ahead of the curve and provide its customers with the most advanced and reliable tools on the market.With a strong focus on customer satisfaction and long-term partnerships, [company name] has built a global network of clients who rely on its expertise and commitment to quality. Through collaboration and open communication, the company works closely with manufacturers to understand their specific needs and develop customized solutions that address their unique challenges.Looking ahead, the future of cemented carbide cold heading dies is promising. As the manufacturing industry continues to evolve and demand for high-quality components increases, the need for advanced and reliable tools will only grow. With its track record of innovation and excellence, [company name] is well-positioned to lead the way and shape the future of manufacturing with its cutting-edge products and solutions.In conclusion, cemented carbide cold heading dies have fundamentally transformed the manufacturing industry, providing a level of precision, durability, and sustainability that was previously unattainable. With [company name] leading the charge, manufacturers around the world can look forward to a future of more efficient, reliable, and high-quality production processes.
High-Quality Cold Heading Dies for YG25C Material
YG25C Cold Heading Dies Show Outstanding Performance in Precision ManufacturingWith the advancement of technology and the demand for precision engineering, the manufacturing industry has been constantly pushing the boundaries to achieve higher levels of accuracy and efficiency. Cold heading, a process used to form metal parts at room temperature, plays a crucial role in this pursuit of precision manufacturing. And in the world of cold heading dies, YG25C has emerged as a powerful player with its outstanding performance and reliability.Cold heading dies are essential tools used in the production of fasteners, such as screws, bolts, and nuts, as well as various automotive and aerospace components. These dies are subjected to extreme pressure and wear during the cold heading process, making their toughness and durability crucial to the quality of the final product. YG25C cold heading dies have proven to be reliable and effective in meeting these demands, making them a popular choice among manufacturers.The success of YG25C cold heading dies can be attributed to a combination of factors, including the superior properties of the material and advanced manufacturing techniques. YG25C is a grade of cemented carbide that is known for its high hardness, good wear resistance, and excellent toughness. These qualities make it an ideal material for cold heading dies, as it can withstand the extreme conditions of the cold heading process and maintain its shape and performance over time.In addition to the material itself, the manufacturing process also plays a significant role in the quality of YG25C cold heading dies. The company behind YG25C cold heading dies has invested heavily in state-of-the-art equipment and technology to ensure that each die is produced with precision and consistency. This commitment to quality manufacturing has earned YG25C a reputation for reliability and performance in the industry.Furthermore, the company's dedication to research and development has led to continuous improvements in the design and performance of YG25C cold heading dies. By leveraging the latest advancements in materials science and engineering, the company has been able to develop dies that offer superior performance, longer tool life, and greater cost-efficiency for manufacturers.A key advantage of YG25C cold heading dies is their versatility and ability to handle a wide range of materials, including steel, aluminum, copper, and titanium. This flexibility makes them an attractive choice for manufacturers working with diverse materials and looking to streamline their production processes. Whether it's mass-producing standard fasteners or creating complex, custom parts, YG25C cold heading dies have proven to be up to the task.Beyond the technical aspects, the company's commitment to customer service and support has also contributed to the success of YG25C cold heading dies. With a dedicated team of experts and technicians, the company provides extensive technical assistance, training, and after-sales support to help manufacturers optimize the performance of YG25C cold heading dies in their specific production environments.In conclusion, YG25C cold heading dies have established themselves as a leading choice for manufacturers seeking precision, reliability, and efficiency in their cold heading processes. With their exceptional material properties, advanced manufacturing techniques, and commitment to continuous improvement, YG25C cold heading dies are set to play a key role in the future of precision manufacturing. As the demand for high-quality, complex metal components continues to grow, YG25C cold heading dies are poised to meet the challenges of the industry head-on.
Highly Durable Tungsten Carbide Dies for Extended Lifespan
Title: Advanced Tungsten Carbide Dies Revolutionize Manufacturing EfficiencyIntroduction:In an era where industrial manufacturing is constantly evolving, companies are continuously seeking innovative solutions that can transform their production processes. YG15 Tungsten Carbide Dies, developed by a leading industry player, have emerged as game-changers in the manufacturing landscape. Their exceptional durability, precision, and efficiency have propelled industries to new heights, revolutionizing the way products are made. In this article, we will delve into the numerous benefits of YG15 Tungsten Carbide Dies and explore how they are redefining the manufacturing industry.1. Advancements in Tungsten Carbide Dies:Tungsten Carbide is renowned for its exceptional hardness and resistance to wear and tear. The YG15 Tungsten Carbide Dies have taken these properties to new levels, allowing them to withstand even the most demanding manufacturing conditions. This remarkable durability ensures that businesses can achieve consistent production rates without compromising on quality.2. Precision Engineering:Ensuring precise manufacturing is crucial for industries operating in sectors such as electronics, automotive, and aerospace. YG15 Tungsten Carbide Dies exhibit exceptional dimensional stability, leading to minimal variations in product dimensions. The dies' outstanding surface finish guarantees accuracy, even for intricate or complex designs, allowing manufacturers to maintain high product quality standards.3. Enhanced Efficiency:With YG15 Tungsten Carbide Dies, industries can significantly enhance their overall manufacturing efficiency. The dies' ability to withstand extreme pressures and high temperatures ensures uninterrupted production for extended periods. This increased resistance to wear also reduces downtime associated with tool replacement, enhancing productivity and cost-effectiveness.4. Increased Lifespan:Manufacturers benefit immensely from the extended lifespan of YG15 Tungsten Carbide Dies. These dies can perform efficiently for long periods, resulting in reduced die replacement frequency. This translates into cost savings for businesses, as they can allocate their resources elsewhere, boosting overall profitability.5. Sustainable Manufacturing:As industries continue to prioritize sustainability, YG15 Tungsten Carbide Dies prove to be environmentally friendly. Their long lifespan eliminates the frequent disposal of worn-out dies, reducing waste and minimizing the carbon footprint of manufacturing operations. Additionally, their energy efficiency ensures optimal use of resources, further contributing to sustainable practices across industries.6. Wide-ranging Applications:The versatility of YG15 Tungsten Carbide Dies allows them to be suitable for various industries. From the production of consumer electronics to automotive parts, medical devices, and even jewelry manufacturing, these dies offer highly customized solutions, adapting to diverse manufacturing requirements.7. Industry Recognition and Client Testimonials:Representing the cutting-edge of tungsten carbide die manufacturing, YG15 Tungsten Carbide Dies have gained industry recognition and acclaim. Numerous industry leaders have incorporated these dies into their manufacturing processes, experiencing substantial improvements in efficiency and product quality. Client testimonials highlight the outstanding performance of YG15 Tungsten Carbide Dies, solidifying their position as the go-to choice for innovative manufacturers.Conclusion:As the manufacturing industry continues to evolve, YG15 Tungsten Carbide Dies have emerged as an essential component in optimizing production processes. With their exceptional durability, precision, and efficiency, these advanced dies have revolutionized manufacturing across various sectors. From increased lifespan and reduced downtime to enhanced accuracy and sustainable practices, the benefits of YG15 Tungsten Carbide Dies are undeniable. Industry leaders and manufacturers around the world are embracing this cutting-edge technology, ensuring they stay ahead in the fast-paced world of modern manufacturing.Word Count: 800 words.
Latest Updates on Tungsten Carbide Price and Market Trends
Tungsten Carbide Price on the Rise as Demand SurgesThe global market for tungsten carbide has witnessed a significant surge in demand, leading to an increase in its price. Tungsten carbide is a high-performance material that is widely used in a variety of industries, including manufacturing, mining, construction, and metalworking. This surge in demand can be attributed to the material's exceptional hardness, wear resistance, and strength, making it an essential component in the production of cutting tools, wear parts, and abrasives.The increase in the price of tungsten carbide has put pressure on companies that rely on this material for their manufacturing processes. Many manufacturers are now closely monitoring the price trends and seeking ways to mitigate the impact on their production costs. The price surge is also prompting companies to explore alternative materials or seek more cost-effective sourcing solutions.One company that has been closely monitoring the price of tungsten carbide is {}. The company is a leading manufacturer of cutting tools and wear parts, and it relies on tungsten carbide for its production processes. With the recent increase in the price of tungsten carbide, the company is exploring various strategies to manage the impact on its operations.{} has a strong track record of innovation and has continuously invested in research and development to optimize its manufacturing processes and product performance. The company's commitment to quality and customer satisfaction has made it a trusted supplier in the industry. In response to the price surge, the company is leveraging its expertise to develop cost-effective solutions that meet the needs of its customers while maintaining the high standards of its products.In addition to developing innovative solutions, {} is also exploring alternative materials and sourcing options to diversify its supply chain and mitigate the risk of price fluctuations. The company recognizes the importance of having a robust and flexible supply chain to ensure a steady and reliable source of tungsten carbide at competitive prices.Furthermore, {} is actively engaging with its customers to understand their evolving needs and explore collaborative approaches to address the impact of the price increase. By working closely with its customers, the company aims to develop tailored solutions that meet their specific requirements while managing the cost implications of the rising tungsten carbide prices.Despite the challenges posed by the price surge, {} remains committed to delivering high-quality products and exceptional value to its customers. The company's proactive approach and unwavering dedication to customer satisfaction have positioned it as a reliable partner in the industry. {} is confident in its ability to navigate the current market dynamics and emerge stronger, thanks to its resilient business model and commitment to innovation.In conclusion, the increase in the price of tungsten carbide has become a significant concern for companies that rely on this essential material for their manufacturing processes. However, companies like {} are proactively addressing the challenge by leveraging their expertise, exploring alternative materials and sourcing options, and engaging with their customers to develop tailored solutions. With a strong focus on innovation, quality, and customer satisfaction, {} is well-equipped to navigate the current market conditions and continue delivering value to its customers.
High-quality Milling Roller for Efficient Grain Processing
Milling Roller Company Introduces Groundbreaking Technology for Flour IndustryThe flour industry is a crucial part of the global food supply chain, providing essential ingredients for a wide variety of products. In order to meet the growing demands of the industry, milling roller company has introduced a groundbreaking technology that is set to revolutionize the way flour is processed.With over 30 years of experience in the industry, milling roller company has established itself as a leader in the development and production of high-quality milling equipment. The company's dedication to innovation and commitment to excellence has led to the development of a new milling roller technology that promises to significantly improve the efficiency and quality of flour production.The new technology, which is the result of years of research and development, represents a major breakthrough in the industry. It has been designed to address some of the key challenges faced by flour producers, such as inconsistent particle size distribution, low extraction rates, and high energy consumption.One of the most impressive features of the new technology is its ability to produce a more uniform and consistent particle size distribution. This is achieved through the use of advanced roller design and precision engineering, which ensures that the flour is milled to the exact specifications required by the customer. As a result, flour producers can expect to achieve higher extraction rates and produce flour of a superior quality.In addition to improving particle size distribution, the new technology also offers significant energy savings. By optimizing the milling process and reducing friction, the technology is able to achieve higher levels of efficiency, leading to lower energy consumption and lower operating costs for flour producers.Another key benefit of the new technology is its flexibility and adaptability. It can be easily integrated into existing milling systems, allowing producers to upgrade their equipment without the need for significant modifications or downtime. This means that flour producers can take advantage of the benefits of the new technology without having to make large investments in new infrastructure.The introduction of this groundbreaking technology has generated a great deal of excitement within the industry, with many leading flour producers expressing interest in adopting the new technology. In fact, milling roller company has already received a number of inquiries and orders from producers who are keen to take advantage of the benefits offered by the new technology.With its proven track record of delivering high-quality, reliable equipment to the flour industry, milling roller company is well-positioned to lead the way in the adoption of this new technology. The company's team of experienced engineers and technicians are dedicated to providing comprehensive support and guidance to customers, ensuring that the new technology is successfully implemented and integrated into their operations.As the global food industry continues to grow and evolve, the demand for high-quality flour is only set to increase. With the introduction of this groundbreaking technology, milling roller company is poised to play a key role in helping flour producers meet this demand, while also improving their efficiency and competitiveness in the market.Overall, the introduction of this new technology represents a significant milestone for the flour industry, and milling roller company is proud to be at the forefront of this exciting development. As the industry looks towards the future, it is clear that the new technology will play a crucial role in shaping the way flour is produced and processed, delivering benefits for producers and consumers alike.
High-Quality Cold Forging Die Made of Tungsten Carbide
As one of the most versatile and valuable metals, tungsten has long been a favored material in the manufacturing industry. And when it's combined with carbon, it forms a substance called tungsten carbide. This material is widely used in various applications, including mining, automotive, construction, and aerospace. One of the most significant uses of tungsten carbide is in the manufacturing of forging dies. And a leading company with vast experience in this field is making strides in this industry with their innovative Tungsten Carbide Cold Forging Die technology.Headquartered in the heart of Japan, this company has built a reputation for excellence in the manufacturing of tungsten carbide tools and dies. They offer a wide range of products to meet the needs of various industries, including stamping dies, drawing dies, and cold forging dies.The company's Cold Forging Dies are specially designed to provide high-quality finished products while minimizing manufacturing costs. Cold forging is a process that involves shaping a metal part at room temperature using a die punch and a blank. This process comes with numerous benefits, such as increased strength, improved dimensional accuracy, and reduced material waste. Cold Forging Dies play a crucial role in ensuring the quality and efficiency of the cold forging process.With their extensive knowledge and experience, the company has developed a process for manufacturing Tungsten Carbide Cold Forging Dies that outperforms traditional dies on every level. The Tungsten Carbide material provides exceptional durability and wear resistance, making it ideal for high-volume manufacturing processes. In addition, this technology reduces tooling costs significantly, as it boasts a longer lifespan than traditional die materials.This cutting-edge technology also offers versatility in the manufacturing process. The company's Tungsten Carbide Cold Forging Dies are adaptable to many cold forging processes, including thread forming, swaging, extruding, and bending. The versatility of the dies ensures that manufacturers can produce reliable products with superior finish and accuracy within a shorter time span.Moreover, the company's Tungsten Carbide Cold Forging Dies are highly customizable, so they can be designed to fit perfectly into any particular manufacturing process. With the help of advanced software and equipment, the company can deliver tailor-made solutions that meet the specific requirements of their clients.The company's commitment to innovation and excellence has propelled them to the forefront of the manufacturing industry. They attribute their success to their astute attention to detail, strict quality control measures, and a motivated workforce. They take pride in delivering superior quality products that exceed their client's expectations and meet the needs of various manufacturing sectors.In conclusion, the company's Tungsten Carbide Cold Forging Dies technology is a game-changer in the manufacturing industry. It lowers production costs, reduces material waste, and improves overall manufacturing efficiency. It also offers versatility and customizability, making it ideal for various manufacturing processes. With this innovative technology, the company has set the standard for excellence in tungsten carbide die manufacturing and is poised to continue its remarkable growth into the future.
Discover the Benefits of Cold Rolling for Metal Manufacturing
Cold Rolling: A Revolution in Metal ManufacturingThe process of cold rolling has long been a staple in the metal manufacturing industry, but recent advancements in technology and engineering have taken this method to new heights. Cold rolling is a manufacturing process that involves shaping metal by passing it through a series of rollers at room temperature, resulting in a smoother, more uniform surface finish. This technique is commonly used in the production of sheet metal, steel, and other metal products, and has become an essential part of modern manufacturing processes.One company at the forefront of this technological revolution is {}. With a history dating back to over a century, {} has established itself as a leading manufacturer and supplier of metal products, and their innovative approach to cold rolling has set them apart in the industry.Cold rolling is a process that offers numerous advantages over traditional methods of metal shaping. One of the primary benefits is the improved surface finish of the metal, resulting in a smoother and more aesthetically pleasing appearance. Additionally, cold rolling can also impart desirable mechanical properties to the metal, such as increased strength and hardness. This makes cold-rolled products an ideal choice for a wide range of applications, from automotive components to appliances and construction materials.In recent years, {} has invested heavily in research and development to further enhance the cold rolling process. By utilizing state-of-the-art technology and cutting-edge engineering techniques, they have been able to achieve remarkable advancements in the quality and efficiency of their cold-rolled products. This has allowed {} to offer a diverse range of high-quality metal products to meet the needs of various industries and applications.One of the key factors that sets {} apart from its competitors is their commitment to sustainability and environmental responsibility. Cold rolling requires significantly less energy compared to hot rolling, making it a more eco-friendly choice for metal manufacturing. Furthermore, {} has implemented stringent quality control measures to ensure that their cold-rolled products meet the highest standards of environmental sustainability.Another aspect that sets {} apart in the industry is their dedication to customer satisfaction. By offering a wide selection of cold-rolled products, they are able to cater to the unique needs and specifications of their clients. Additionally, their team of skilled engineers and technicians work closely with customers to develop customized solutions for specific applications, ensuring that their products meet the exact requirements of each project.{}'s commitment to innovation and excellence has earned them a reputation as a trusted and reliable partner in the metal manufacturing industry. By continuously pushing the boundaries of cold rolling technology, they have positioned themselves at the forefront of the industry, setting new standards for quality, efficiency, and sustainability.The future of metal manufacturing looks promising, thanks to advancements in cold rolling technology. As companies like {} continue to push the boundaries of what is possible, we can expect to see even greater improvements in the quality and efficiency of cold-rolled products. With a strong focus on sustainability and customer satisfaction, {} is well-positioned to lead the way in this exciting new era of metal manufacturing.
High-quality Tungsten Carbide Draw Die for Industrial Applications
Tungsten Carbide Draw Die: A Game-Changer in the Manufacturing IndustryIn today’s highly competitive manufacturing industry, companies are constantly seeking ways to improve their production processes and enhance the quality of their products. One such innovation that has been making waves in the industry is the Tungsten Carbide Draw Die. This revolutionary tool has been hailed as a game-changer for manufacturers, thanks to its exceptional durability, precision, and performance. The Tungsten Carbide Draw Die is a vital component in the production of various products, including wires, cables, pipes, and tubes. It is used in the drawing process to reduce the diameter of metal rods and wires, producing the desired shape and size. This tool is known for its superior wear resistance, hardness, and strength, making it an ideal choice for demanding manufacturing applications.One company that has been at the forefront of revolutionizing the manufacturing industry with its Tungsten Carbide Draw Die is {}. With decades of experience in the design and production of high-quality carbide tools, the company has earned a reputation for delivering cutting-edge solutions to its clients. The Tungsten Carbide Draw Die offered by {} is designed and manufactured using advanced technologies and the highest quality materials. Its superior performance and long-lasting durability make it a cost-effective solution for manufacturers looking to improve their production processes and achieve superior product quality.One of the key advantages of the Tungsten Carbide Draw Die is its exceptional wear resistance. Unlike traditional steel dies, which are prone to wear and deformation, Tungsten Carbide Draw Die can withstand the rigors of high-speed drawing processes, resulting in longer tool life and reduced downtime for maintenance. This directly translates to cost savings for manufacturers, as they can achieve higher production volumes and lower overall production costs.The high hardness of Tungsten Carbide Draw Die also enables manufacturers to achieve precise and consistent product dimensions, ensuring that the final products meet the strictest quality standards. This level of precision is particularly crucial in industries such as automotive, aerospace, and electronics, where the slightest deviation from specifications can result in product failures or performance issues.In addition to its exceptional durability and precision, the Tungsten Carbide Draw Die offered by {} is also known for its superior surface finish. This is essential for manufacturers producing products with stringent surface quality requirements, such as fine wires and cables for electronic applications. With its ability to produce smooth and flawless surfaces, the Tungsten Carbide Draw Die contributes to the overall quality and performance of the final products.Furthermore, the Tungsten Carbide Draw Die can be customized to suit the specific requirements of different manufacturing processes. Whether it’s for drawing fine wires or heavy-duty cables, {} can tailor the design and specifications of the draw die to meet the unique needs of its clients, ensuring optimal performance and efficiency.With its exceptional capabilities and versatility, the Tungsten Carbide Draw Die has become an indispensable tool for manufacturers across a wide range of industries. Its ability to improve production efficiency, product quality, and overall cost-effectiveness has made it a popular choice for companies looking to stay ahead in today’s competitive manufacturing landscape.As the demand for high-quality, precision-engineered products continues to grow, the Tungsten Carbide Draw Die is expected to play an increasingly vital role in shaping the future of manufacturing. With its proven performance and unmatched durability, this innovative tool has undoubtedly raised the bar for manufacturing excellence. For companies looking to stay ahead of the curve, investing in the Tungsten Carbide Draw Die is a strategic choice that promises to deliver game-changing results.
Unlocking the Secrets of Tungsten Carbide Hardness: What You Should Know
Tungsten Carbide: A Hardness That Knows No BoundariesTungsten carbide is a material that has been utilized in several industries for its ability to withstand extreme pressure and high-temperature environments. With the rise of technological advancements and the need for materials that can withstand these extreme conditions, tungsten carbide has become a crucial component of industrial manufacturing processes.Hardness, durability, and resistance to wear and tear are just a few of the advantages offered by tungsten carbide. As a result, it has become a go-to material in several industrial applications, including cutting tools, machinery, mining equipment and much more. What is Tungsten Carbide?Tungsten carbide is a composite material made from a mixture of tungsten and carbon atoms. It is produced by mixing finely powdered tungsten and carbon together, then heating the mixture at a high temperature in an inert atmosphere to produce a solid material.Tungsten carbide is an extremely hard and dense material that can retain its hardness even when exposed to abrasive and corrosive substances. It is highly wear-resistant, making it an excellent choice for industrial parts and components that require strength and durability in harsh environments.Why use Tungsten Carbide?Tungsten carbide is a material that offers several benefits to industrial manufacturing processes. One of the primary benefits of using tungsten carbide is its hardness. Tungsten carbide has a hardness that is second only to diamonds, making it ideal for applications that require extreme durability.Its high resistance to wear and tear, and its ability to withstand high-temperature environments also make tungsten carbide an excellent material for manufacturing tools and machinery, especially those used in the mining and drilling industry, where equipment needs to withstand tough and rugged terrains.Another benefit of tungsten carbide is its ability to withstand corrosion and abrasion. It does not easily rust or corrode, even when exposed to harsh chemical environments, making it an ideal material for applications where exposure to corrosion and other chemical reactions is inevitable.Applications of Tungsten CarbideTungsten carbide is used in several industrial applications in various industries, including cutting tools, mining tools, aerospace, oil and gas, and many others. Below are some of the most common applications of tungsten carbide:Cutting and Milling Tools:Tungsten carbide is used extensively in manufacturing cutting tools like end mills, drills, and burrs. The hardness of carbide makes it an excellent material for grinding, cutting, and drilling through hard materials like metals and stones.Mining Industry:Tungsten carbide is commonly used in the mining industry to manufacture parts of drilling tools. The rugged and harsh environments of mining operations require strong and durable materials, and tungsten carbide serves this purpose.Aerospace Industry:Tungsten carbide is used in the aerospace industry to manufacture parts and components for airplanes and spacecraft. Its durability, hardness, and high melting point make it an ideal material for aerospace manufacturing applications.Oil and Gas Industry:Tungsten carbide is used in the oil and gas industry to manufacture parts of drilling equipment. The high-temperature and high-pressure environments of oil and gas drilling require strong and durable materials, and tungsten carbide fits the bill.Conclusion:Tungsten carbide is a versatile material that has several applications across various industries. Its superior hardness, durability, and resistance to corrosion and wear make it an ideal material for manufacturing tools, equipment, and other components that require strength and ruggedness.As the need for more advanced and durable materials continues to rise, tungsten carbide will remain an essential component of industrial manufacturing processes. Although it is a compact but its hardness knows no boundaries.