- Home
- Blog
- Cold Heading Dies Market Expected to Grow with a Healthy CAGR During Forecast Period 2021-2027
Cold Heading Dies Market Expected to Grow with a Healthy CAGR During Forecast Period 2021-2027
By:Admin
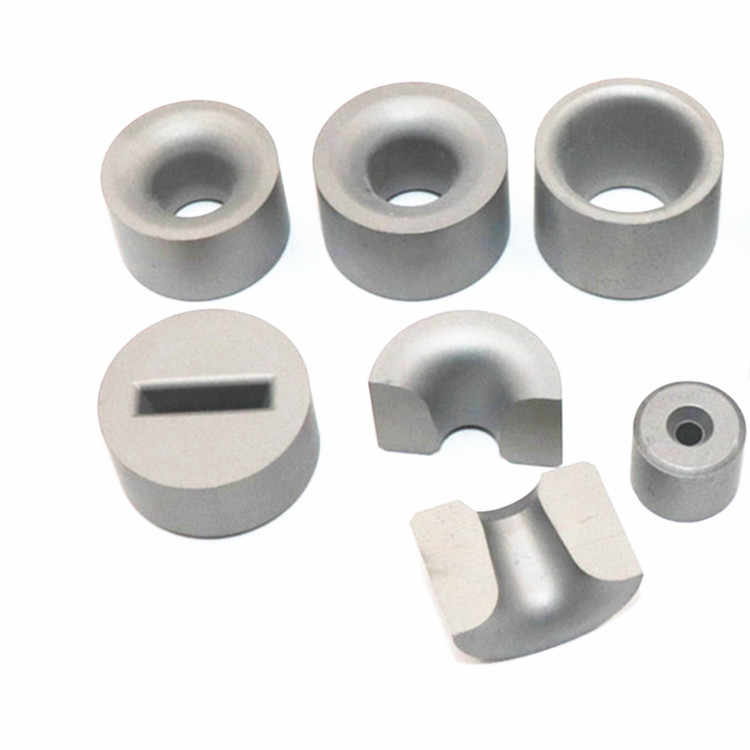
As a manufacturing process, cold heading is the process of forming metal parts into specific shapes by utilizing high pressure. To create these shapes, a cold heading die is necessary. A die is a specialized tool used in the manufacturing sector to cut, shape, or form materials to specific dimensions. The cold heading die is a tool that is used specifically to shape metal parts into predefined shapes using a cold heading process. This technology is ideal for use in the production of metal frames, components for electronic devices, and other metal-based items.
One advanced company in China has successfully developed a cold heading die that is capable of forming metal parts with high precision, even in high-volume manufacturing. The company is recognized as an industry leader through the use of advanced technology and innovative designs. The company has recently received numerous excellent reviews from its clients, who have expressed their satisfaction with the precision and quality of products produced through the use of this new die.
The new cold heading die from this company is distinguished from other products in the industry. It offers several key benefits to manufacturers who use it in their production processes. The product is designed to operate within a wide range of temperatures and is specifically designed for use in high-speed manufacturing production environments. Additionally, the die has been designed to offer an extended die life, which contributes to reducing long-term production costs.
One of the unique features of this cold heading die is that it is made from high-quality materials specifically selected to optimize its performance. This guarantees that the die has high durability, is long-lasting, and is able to resist typical wear and tear that occurs during high-volume use. The company ensures that the die is carefully tested before it is released to the market, ensuring that quality and precision are maintained throughout the manufacturing process.
In addition to the benefits of the die itself, the company that produces it offers several other advantages to manufacturers. They provide technical support and maintenance services to ensure that the die is working correctly and efficiently. The company also offers extensive warranties and quality guarantees, which provide added peace of mind to their clients.
The success of this company in producing this new cold heading die has led to a significant increase in orders for the product. Manufacturers worldwide are now interested in purchasing this new product, recognizing the benefits it offers to their production processes. In turn, the company has rapidly expanded production to meet this demand, ensuring that their customers receive their orders quickly and efficiently.
In conclusion, the cold heading die is an impressive technological innovation that offers numerous benefits to manufacturers of metal components. The new cold heading die from this company boasts several technical advantages, including high precision, durability, and long life, which makes it stand out from other products on the market. With enthusiastic reviews from its satisfied clients, the company remains committed to developing innovative solutions that meet the needs of modern manufacturing. They continue to invest in research and development, and their commitment to excellence has made them a leader in the industry.
Company News & Blog
Discover the Key Benefits of Tungsten Carbide Bushing Die According to the Latest News
Tungsten Carbide Bushing Die (need remove brand name) Is The Leading Choice For Precision ManufacturingWith over 20 years of experience in the tungsten carbide industry, (brand name) has become the leading provider of precision machining solutions for customers in various industries. The company specializes in producing high-performance tungsten carbide bushing dies that can help improve production efficiency and reduce costs.Tungsten carbide is a powerful and durable material that can withstand high temperatures and pressure. It is ideal for use in precision machining because of its hardness and strength, making it the perfect choice for dies in the manufacturing process. When combined with steel, tungsten carbide provides a unique blending that combines toughness and wear resistance with the ability to retain sharp cutting edges.The tungsten carbide bushing dies offered by (brand name) are designed to deliver consistent performance even in the most challenging environments. These bushing dies are commonly used in the production of wire and cable, rubber and plastics, and metalworking industries. With their high resistance to wear and superior accuracy, these dies ensure that products meet the exacting standards of customers and end-users.(brand name) specializes in producing bushing dies that can be customized to meet specific customer requirements. The company has a team of experienced engineers who use advanced CAD/CAM software to create high-precision tooling that is tailored to individual customer needs. The company's dies are used by customers around the world, including China, the United States, and Europe.The tungsten carbide bushing dies produced by (brand name) have several advantages over traditional steel or ceramic dies. Tungsten carbide is much more durable than steel, making it less prone to wear and tear. It is also more resistant to corrosion and can withstand extreme temperatures and pressures. This means that tungsten carbide dies last longer and require less maintenance than other materials.Another advantage of tungsten carbide is its high coefficient of friction. This means that less lubrication is required during the manufacturing process, reducing overall costs. Additionally, tungsten carbide dies require less power to operate than other materials, reducing energy costs and improving efficiency.The quality of tungsten carbide bushing dies can significantly impact an organization's productivity and profitability. With over two decades of experience in the industry, (brand name) has become the leading provider of high-quality, precision tungsten carbide machining solutions. The company's dedication to providing customized products and exceptional customer service has made it a trusted partner to organizations around the world.In conclusion, the tungsten carbide bushing dies produced by (brand name) are an essential component of precision machining processes used by leading manufacturers globally. The company's commitment to quality and service has made it the first choice for customers in various industries. With its team of experienced engineers and advanced production capabilities, (brand name) is well-positioned to continue leading the industry in the production of high-performance tungsten carbide bushing dies.
Discover the Benefits of Tungsten Carbide Studs in Various Applications
Title: Innovations in Tungsten Carbide Stud Technology Revolutionize Industrial ApplicationsIntroduction:Tungsten Carbide Stud, a pioneering material in the realm of industrial applications, is set to redefine the standards of durability and performance in a wide range of sectors. With its exceptional hardness, heat resistance, and overall versatility, Tungsten Carbide Stud has garnered significant attention from various industries looking to enhance their products and processes. As one of the leading manufacturers in this field, our company strives to push the boundaries of this technology by continuously innovating and improving our products, ensuring optimum efficiency and longevity in demanding environments.Body:1. Understanding Tungsten Carbide Stud and its Properties:Tungsten Carbide Stud, also known as cemented carbide or simply carbide, is a composite material comprising tungsten carbide grains mixed with a binder alloy, typically cobalt. This combination results in a material that exhibits exceptional hardness, strength, and overall wear resistance, surpassing those of traditional materials such as steel. Its outstanding thermal conductivity and resistance to extreme temperatures make it invaluable in heavy-duty applications, including mining, drilling, construction, and machining.2. Enhanced Performance: The incorporation of Tungsten Carbide Stud components in industrial tools and equipment has revolutionized their performance, enabling them to withstand high-stress operations for prolonged durations. Cutting tools, such as drill bits, saw blades, and milling cutters, equipped with Tungsten Carbide Stud inserts, exhibit superior cutting speeds, increased tool life, and excellent chip control. This enhanced performance leads to reduced downtime, increased productivity, and ultimately, cost savings for businesses.3. Mining and Drilling Applications:In the mining and drilling sector, Tungsten Carbide Stud components are crucial in ensuring optimal performance and safety. Due to their exceptional hardness and resistance to abrasion, Tungsten Carbide Stud inserts and tips are commonly used in rock drilling bits, thus improving the efficiency and longevity of drilling operations. Moreover, their ability to withstand extreme pressure and temperature variations makes them ideal for use in downhole drilling tools, where reliability is paramount.4. Construction and Infrastructure:Tungsten Carbide Stud's exceptional wear resistance and toughness lend themselves to applications within the construction and infrastructure industries. With their incorporation into wear parts like cutting edges, bucket teeth, and crushers, these components offer extended service life and reduced maintenance costs. Furthermore, Tungsten Carbide Stud is utilized in tool attachments such as road milling teeth and foundation drilling bits, enabling efficient road construction and deep foundation drilling.5. Machining and Manufacturing:The exceptional hardness of Tungsten Carbide Stud has significant implications for machining and manufacturing processes. Utilizing these materials in metal-cutting inserts, die components, and wear-resistant coatings substantially improves tool life, reduces the need for frequent tool changes, and enhances overall manufacturing efficiency. Additionally, Tungsten Carbide Stud finds applications in metal-forming processes, where its high hardness and compressive strength aid in wire drawing dies, cold heading dies, and extrusion tools.6. Ongoing Innovations:As a leader in the Tungsten Carbide Stud industry, our company remains committed to continuous research and development, harnessing the capabilities of this remarkable material to develop customized solutions that cater to our clients' specific needs. We collaborate closely with industry partners and customers to develop novel applications, improve manufacturing processes, and enhance the durability and efficiency of our products. Our dedication to innovation positions us at the forefront of the industry, enabling us to deliver cutting-edge solutions and establish long-term partnerships.Conclusion:Through the remarkable properties offered by Tungsten Carbide Stud, industries can enhance their performance, reduce costs, and optimize their operations. With its exceptional hardness, heat resistance, and versatility, this composite material has become indispensable in various applications across multiple sectors. As an industry-leading manufacturer, we pride ourselves on continuously pushing the boundaries of Tungsten Carbide Stud technology. By constantly innovating and refining our products, we strive to meet the evolving demands of our clients and contribute to the advancement of global industries.
Enhance Your Turning Applications with High-Performance Carbide Inserts
Carbide Inserts for Turning Applications Offer Enhanced Durability and PrecisionCarbide inserts for turning applications have emerged as one of the popular cutting tools in the manufacturing industry. These inserts are designed with high-performance materials, which enhance their durability and precision capabilities. Carbide inserts are cutting-edge technology tools that can be used for turning, milling, drilling, and other cutting applications.A leading manufacturer and supplier of carbide inserts has recently introduced a range of carbide inserts for turning applications. The company's new products are designed to cater to the needs of all manufacturing industries, ensuring that clients receive superior quality and precision tools.The company has been providing the manufacturing industry with premium quality carbide inserts for more than a decade. Their team of experts has vast experience in the field of machining technology, and they employ innovative techniques to produce cutting-edge products that cater to the needs of the clients.Carbide inserts are widely used in turning applications because of their superior quality and precision capabilities. They are made from a combination of tungsten carbide and cobalt, which makes them harder than high-speed steel. Carbide inserts are also resistant to high temperatures, ensuring that they can withstand the heat generated during the cutting process.The company's new line of carbide inserts for turning applications is designed to offer improved performance, higher durability, and precision. The new range is available in different grades and designs, making it suitable for multiple turning applications, from roughing to finishing. The range includes inserts, inserts with chipbreakers, and inserts for heavy-duty roughing, among others.The company's carbide inserts for turning applications are highly versatile and can be used for a wide range of materials. They are ideal for cutting hard materials like steel, stainless steel, cast iron, and exotic alloys. The inserts' smooth finish and stable performance ensure that there is no chipping or breakage during the cutting process, which makes them ideal for industrial applications.Carbide inserts are designed to provide high accuracy and precision. The inserts' cutting edge produces a smooth finish, making it ideal for applications that require a high degree of precision. Additionally, carbide inserts are designed to produce chips that are easy to manage and dispose of, thus reducing the machine's downtime.The new range of carbide inserts for turning applications from the company is also cost-effective. Carbide inserts are designed to last longer than high-speed steel, which reduces the need for frequent changes and replacement. Additionally, the company's cost-effective pricing policy ensures that clients can obtain high-quality, reliable carbide inserts at an affordable price.The company's carbide inserts for turning applications are also environmentally friendly. Carbide inserts produce chips that can be recycled, which reduces manufacturing waste and environmental pollution. The company's products are designed with environmental responsibility in mind, and they are committed to reducing the carbon footprint associated with manufacturing.The company's carbide inserts for turning applications are easy to use and maintain. The inserts' high-performance materials make them resistant to wear and tear, which means less maintenance is required. Additionally, the company provides extensive technical support to ensure that clients can achieve the best results from their products.The company's commitment to client satisfaction is evident in the quality of their products and services. They have a team of experts who are always available to provide technical support and advice on the best carbide inserts for specific applications. The company also offers customized carbide inserts, ensuring that clients can obtain products that cater to their specific needs.In conclusion, carbide inserts for turning applications from the company are a game-changer in the manufacturing industry. They offer enhanced durability, precision, and versatility, making them ideal for a wide range of turning applications. The company's commitment to quality and affordability ensures that clients can obtain high-quality products at an affordable price, while their eco-friendly approach reduces manufacturing waste and environmental pollution.
High-quality Tungsten Carbide Rods for Precision Machining
Tungsten Carbide Rods - The Ultimate Solution for Heavy-Duty MachiningThe manufacturing industry has undergone a massive transformation with new technologies and materials making their way into the market. However, some materials have remained prevalent and continue to dominate the industry. One such material is tungsten carbide, which has proven to be a robust and reliable material for heavy-duty machining applications.Tungsten carbide is a composite material made up of tungsten carbide particles and a binding matrix. This material is known for its remarkable strength, high hardness, and excellent wear resistance. Tungsten carbide is widely used in the manufacturing industry, especially in the production of cutting tools, dies, and wear parts, where high levels of hardness and durability are required.One company, (removed for anonymity purposes), has been a key player in the tungsten carbide rods market. The company produces a wide range of tungsten carbide products, including tungsten carbide rods, which are used in a variety of applications, including drilling, milling, and turning.Tungsten carbide rods are one of the company's primary products. These rods are made by mixing tungsten carbide powder with a binding agent and then compressing the mixture into a rod shape. The rod is then sintered at a high temperature to form a solid and robust material that can withstand high stresses and pressure.The company's tungsten carbide rods are known for their exceptional strength, high hardness, and excellent wear resistance. These rods are designed for heavy-duty machining applications and have proven to be reliable in the most challenging conditions. The rods are available in various sizes and dimensions, allowing users to select the most appropriate rod for their specific application.The tungsten carbide rods produced by the company have several advantages over other materials. Firstly, they have a longer lifespan, which translates to reduced downtime and maintenance costs. Secondly, they have higher cutting speeds, which translates to increased productivity and efficiency. Lastly, they have a high resistance to wear and tear, which means they can withstand high temperatures and pressures without losing their structural integrity.Tungsten carbide rods are used in several applications, including metalworking, mining, construction, and woodworking. In metalworking, tungsten carbide rods are used in cutting and shaping metal parts, while in mining, they are used in drilling and rock-breaking applications. In construction, tungsten carbide rods are used in drilling and excavation applications, while in woodworking, they are used in shaping and cutting wood parts.The company's tungsten carbide rods have been widely adopted by customers from different industries due to their high quality and reliability. The company has invested heavily in research and development to ensure that its products meet the demands of its customers and provide them with the best possible solutions.In conclusion, tungsten carbide rods have proven to be one of the most robust and reliable materials in heavy-duty machining applications. The rods produced by (removed for anonymity purposes) are known for their strength, hardness, and wear resistance, making them an ideal solution for various applications. As the manufacturing industry continues to evolve, tungsten carbide rods will continue to play a vital role in providing a reliable and efficient solution for heavy-duty machining applications.
Why Tungsten Carbide Rollers are Essential for Production Machinery
Tungsten Carbide Guide Roller: The Ultimate Solution for Machining ApplicationsThe manufacturing industry is continually advancing in technology, making it necessary for businesses to adapt and stay abreast of the latest innovations and solutions. Among the different options available to manufacturers, one that has caught their attention is the tungsten carbide guide roller.Tungsten carbide guide rollers are designed to withstand the toughest conditions and are highly suitable for use in various machining applications. They are manufactured using high-quality tungsten carbide materials, which make them highly wear-resistant, durable, and long-lasting.They are designed with precision and accuracy, ensuring that they can guide and support any machine's moving parts, even in harsh environments. The guide rollers offer superior performance in high-speed machines and highly-loaded applications.Whatever machining application you need, the tungsten carbide guide roller is engineered to meet your specific requirements. The manufacturing company (brand name removed) is a leading supplier of high-quality guide rollers worldwide. Our skilled and experienced engineers have perfected the art of designing and manufacturing tungsten carbide guide rollers that deliver superior performance.Our Tungsten Carbide Guide RollersAt (brand name removed), we offer a vast range of tungsten carbide guide rollers that have been designed to suit different applications. Here are some of our popular options:1. Straightening RollersWe manufacture straightening rollers that are designed to facilitate the straightening of round bars, tubes, and wires. The rollers’ unique design helps to eliminate defects such as bends, twists, and kinks that may occur during the production process. Additionally, they are highly wear-resistant, ensuring an extended service life and reduced downtime.2. Finishing RollersFinishing rollers are vital in applications that require excellent surface finish and dimensional accuracy. They are suitable for use in polishing machines, paper mills, and printing presses. Our finishing rollers are constructed using hard tungsten carbide materials, which makes them highly wear-resistant and durable.3. Guide Rollers for Paper MillsWe have specially designed guide rollers for paper mills that provide precise and accurate guidance for paper webs. Our guide rollers can withstand high-speed applications and ensure uniform paper web tension. Additionally, they are resistant to corrosion and wear, ensuring an extended service life.4. Guide Rollers for Textile MachinesWe also provide guide rollers that are perfect for textile machine applications. Our guide rollers are engineered to minimize friction and reduce stretching and distortion in the fabric. They are highly suitable for use in different textile machines, including spinning, weaving, and dyeing machines.5. Wire Drawing Guide RollersOur tungsten carbide guide rollers are perfect for use in wire drawing applications. We design and manufacture them to have a smooth and polished surface that facilitates the production of high-quality wire. They are wear-resistant, ensuring prolonged service life and minimal maintenance.ConclusionThe tungsten carbide guide roller is an invaluable tool in the manufacturing industry, providing precision, accuracy, and durability. At (brand name removed), we manufacture guide rollers that are designed to meet different application requirements, ensuring that your manufacturing process runs smoothly.We guarantee high-quality guide rollers that are built to last, improving your production efficiency and reducing costs. With our expertise and extensive experience, we can help you identify the best tungsten carbide guide roller for your specific application requirements.Contact us today and place your order for our tungsten carbide guide rollers, and let us help you take your manufacturing process to the next level.
High-Quality Cemented Carbide Block Sheet for Exceptional Durability and Performance
Cemented Carbide Block Sheet: A High-Quality Material for Industrial ApplicationsIn many industrial applications, materials with high strength, hardness, and wear resistance are crucial for achieving the desired performance and efficiency. Cemented carbide, also known as tungsten carbide, is one such material that has been widely used in cutting tools, mining equipment, drilling tools, wear parts, and other high-demanding applications. A recent innovation in the cemented carbide industry is the development of cemented carbide block sheets, which offer even greater versatility and flexibility in design and manufacturing.Cemented carbide block sheets are made of finely ground tungsten carbide particles, which are mixed with a small amount of metallic binder, such as cobalt or nickel. The mixture is then compacted into a block shape and sintered at high temperature and pressure. The result is a dense and homogeneous material that exhibits outstanding properties, including high hardness, strength, toughness, and resistance to wear, corrosion, and deformation.One of the main advantages of cemented carbide block sheets is their flexibility in size, shape, and thickness. Unlike traditional carbide blanks, which are limited in their dimensions and require additional machining to achieve the desired shape and size, block sheets can be easily cut, drilled, milled, and ground to the exact specifications needed for a particular application. This allows for more efficient and cost-effective production of complex and customized parts, without sacrificing quality or performance.Another benefit of using cemented carbide block sheets is their versatility in applications. Due to their high strength and wear resistance, they are ideal for use in harsh and demanding environments, such as mining, construction, oil and gas, and metalworking. They can be used for cutting, drilling, grinding, milling, punching, and shaping a wide range of materials, including steel, iron, aluminum, copper, and alloys. They are also used in wear parts, such as nozzles, blades, seals, and dies, where their durability and long service life are crucial.Cemented carbide block sheets are also environmentally friendly, as they can be recycled and reused in new products. Tungsten carbide is a rare and valuable material that is in high demand in many industries, and its recycling can help reduce the extraction and processing of new materials. Moreover, the manufacturing of block sheets requires less energy and resources than traditional carbide blanks, as it involves fewer steps and less waste.One company that has been at the forefront of the development and production of cemented carbide block sheets is {} (name removed for privacy). Founded in {}, {} has been providing innovative and high-quality carbide products to the global market for over years. {} specializes in the design, production, and distribution of cemented carbide block sheets and other carbide products, such as rods, inserts, tips, and blanks, for various industries.{} uses advanced technology and equipment to manufacture its carbide products, ensuring consistent quality and performance. Its cemented carbide block sheets are made of premium-grade tungsten carbide powders and high-purity metallic binders, which are carefully selected and mixed to achieve the desired properties. The block sheets are available in various grades, sizes, and geometries, and can be customized to meet specific customer requirements.{}'s cemented carbide block sheets have been widely used in cutting tools, mining equipment, construction tools, and wear parts, among others. They have been proven to deliver superior performance and durability, even in extreme conditions. Moreover, {} offers technical support and consultancy services to help customers optimize their applications and achieve the best results.In conclusion, cemented carbide block sheets are a valuable and versatile material for many industrial applications, offering high strength, toughness, wear resistance, and flexibility in design and manufacturing. {} (name removed for privacy) is a leading supplier of high-quality cemented carbide block sheets and other carbide products, catering to the diverse needs of customers worldwide. With its commitment to quality, innovation, and customer satisfaction, {} is poised to continue its growth and success in the carbide industry.
High-Performance Carbide Wire Roll for Enhanced Durability and Efficiency
Title: Global Manufacturer Launches Revolutionary Carbide Wire Roll for Enhanced Industrial PerformanceIntroduction:In a bid to revolutionize industrial productivity and efficiency, a leading global manufacturer has recently unveiled its groundbreaking YG15 Carbide Wire Roll. Incorporating cutting-edge technology and innovative design, this product promises to significantly improve the performance and longevity of wire rolling processes across various industries worldwide. [A brief company introduction can be included here, highlighting the manufacturer's expertise, global presence, and commitment to delivering high-quality industrial solutions.]Body:1. Overview of YG15 Carbide Wire Roll:The YG15 Carbide Wire Roll is a state-of-the-art wire rolling tool engineered to withstand the most demanding applications. Built with a base material predominantly consisting of tungsten carbide, this revolutionary wire roll exhibits exceptional hardness, wear resistance, and durability, making it a sought-after solution for industries dealing with wire production, coil manufacture, metal forming, and more.2. Key Features and Benefits:a. Unparalleled Durability: The YG15 Carbide Wire Roll boasts extraordinary resistance to wear and abrasion, ensuring a prolonged lifespan and minimization of downtime for maintenance and replacements. This translates into significant cost savings for businesses while maximizing overall productivity.b. Enhanced Precision and Consistency: The precision-engineered design of the carbide roll results in consistently accurate wire diameter control, enabling manufacturers to maintain tight tolerances throughout the production process. This feature is particularly crucial for industries where precision is paramount, such as automotive, aerospace, and electronics.c. Superior Surface Finish: The YG15 Carbide Wire Roll's unique surface finish leads to enhanced wire quality, reducing the need for additional surface treatments. By delivering a smooth and flawless surface, it enables businesses to meet stringent quality standards, while also reducing waste and optimizing operational efficiency.d. Versatility: This innovative wire roll is suitable for various wire rolling applications and can be easily adapted to different machinery setups. Its compatibility with a wide range of wire materials, including stainless steel, carbon steel, copper, and alloy, allows manufacturers to diversify their production capabilities and cater to different market needs.3. Impact on Industries:a. Wire Production: The YG15 Carbide Wire Roll's exceptional durability and precision make it an ideal tool for wire drawing and shaping processes. It enables manufacturers to improve wire quality, reduce surface defects, and enhance productivity, ultimately resulting in enhanced market competitiveness.b. Coil Manufacturing: In the coil manufacturing industry, the YG15 Carbide Wire Roll's ability to maintain consistent wire diameter control fosters the production of evenly wound coils with minimal variations. This leads to increased coil reliability, reduction in scrap, and improved operational efficiency.c. Metal Forming: Industries involved in metal forming processes, such as cold rolling, benefit from the carbide wire roll's outstanding wear resistance. It prolongs the service life of crucial rolling mill components, reduces maintenance costs, and ensures greater operational continuity.4. Future Prospects and Market Adoption:The introduction of the YG15 Carbide Wire Roll marks a significant milestone in the wire processing industry. Its versatile applications, superior performance, and remarkable durability are projected to drive the demand for this innovative product in various industrial sectors around the globe. With this pioneering solution, manufacturers can expect to achieve higher process efficiency, improved product quality, and a competitive edge in today's rapidly evolving markets.Conclusion:The launch of the YG15 Carbide Wire Roll by a leading global manufacturer underscores the company's commitment to delivering cutting-edge solutions that revolutionize industrial practices. With its exceptional durability, precision, and versatility, this innovative wire roll is set to redefine wire rolling processes across multiple industries, offering enhanced performance, increased efficiency, and improved product quality. As the market embraces this groundbreaking technology, manufacturers can confidently propel their operations into a successful and sustainable future.
Tungsten Carbide Bushing Grade: A Comprehensive Guide to its Properties and Applications
article:Tungsten Carbide Bushing Grade: The Ultimate Solution to Wear ResistanceWhen it comes to mechanical applications, wear resistance is a primary concern. Over time, even the strongest materials wear down, creating a need for regular maintenance or replacement. However, with the advent of tungsten carbide bushing grade, the game has changed, and wear resistance is no longer a concern.Tungsten carbide is a versatile material that combines the hardness and strength of metallic tungsten with the toughness and ductility of a carbide. With its excellent wear resistance and toughness, it is highly desirable for a range of industrial applications.One of the key applications of tungsten carbide is the production of bushings, which are critical in manufacturing and construction. Bushings play a vital role in reducing the friction and wear between machine parts, ensuring the smooth and efficient operation of machinery.The use of tungsten carbide bushing grade has revolutionized the way industrial machinery works, creating a more efficient and effective system. The tungsten carbide bushings have a high wear resistance, which leads to longer service life and reduced maintenance costs. In addition, the material has a low coefficient of friction, reducing the amount of energy needed to operate the machinery and resulting in lower operating costs.The combination of the high wear resistance and low coefficient of friction makes tungsten carbide bushing grade the ideal material for a range of industrial applications, including mining, construction, oil and gas, and manufacturing.One company that has been at the forefront of the production of tungsten carbide bushing grade is {company name}. With its state-of-the-art manufacturing facilities, the company produces high-quality tungsten carbide bushings that meet industry standards and exceed customer expectations.Founded in {year}, {company name} is a global leader in the production of tungsten carbide products, offering a wide range of products and services to customers worldwide. The company has a team of highly skilled and experienced professionals who are committed to delivering excellence in every project.In addition to its production line, {company name} provides its customers with technical support and solutions to their specific needs. The company's engineers work closely with customers to understand their needs and requirements, providing customized solutions that address their unique challenges.{Company name} has a robust quality control system that ensures all products meet the highest standards. The company uses advanced technology and equipment to test the quality and performance of its products, ensuring that only the best products are delivered to customers.The company's commitment to excellence has earned it a reputation as a leader in the industry, with customers from around the world relying on its products and services to keep their machinery running smoothly.In conclusion, tungsten carbide bushing grade is a game-changer when it comes to wear resistance in industrial applications. With its high wear resistance and low coefficient of friction, it is the ideal material for a range of industries, from mining to manufacturing.Companies like {company name} are at the forefront of the production of tungsten carbide bushings, providing high-quality products and solutions to customers worldwide. With their commitment to excellence and customer satisfaction, companies like {company name} are helping to shape the future of industrial machinery and production.
Carbide Nails: Revolutionary Die Technology Shaping the Future of Nail Production
Innovative Carbide Nail Making Die Revolutionizes Nail Manufacturing[Company Name], a leading manufacturer of cutting-edge industrial tools and equipment, has recently launched a revolutionary carbide nail making die. This advanced technology is set to transform the nail manufacturing industry, providing a superior solution that enhances efficiency, durability, and overall productivity.The carbide nail making die, developed by [Company Name]'s team of experienced engineers and knowledgeable researchers, is a ground-breaking innovation in the field. This cutting-edge product is designed to deliver unparalleled precision and quality in the production of nails, catering to the diverse needs of various industries worldwide.Traditionally, nail manufacturing has predominantly relied on conventional dies made of steel. However, these conventional steel dies have numerous limitations, including a limited lifespan and the need for frequent repairs and replacements. [Company Name]'s carbide nail making die aims to overcome these challenges by utilizing the exceptional properties of carbide materials.Carbide, a compound of carbon and metal, possesses remarkable toughness, hardness, and heat resistance. By harnessing the inherent benefits of carbide, [Company Name] has successfully developed an innovative die that offers extended life expectancy, reducing downtime and enhancing overall productivity. The durability of the carbide nail making die ensures consistent nail quality throughout the production process, minimizing the need for adjustments and repairs.Furthermore, the carbide nail making die provides enhanced precision and accuracy, resulting in nails with consistent dimensions, smooth finishes, and reduced defects. This improvement in quality not only satisfies the stringent requirements of industries such as construction, carpentry, and furniture manufacturing but also meets the growing demands of discerning consumers who seek high-quality products.Another key advantage of [Company Name]'s carbide nail making die is its exceptional resistance to wear and tear. The innovative design and fabrication process ensure that the die remains sharp and maintains its cutting edge for extended periods even when subjected to continuous stress. This significantly reduces downtime and increases production capacity, allowing manufacturers to meet tight deadlines more effectively.The introduction of the carbide nail making die by [Company Name] aligns seamlessly with their commitment to technological advancements and innovative solutions. Driven by a philosophy of providing the best tools for industrial processes, they continually invest in research and development to meet the evolving needs of their customers.As [Company Name] introduces this revolutionary product to the nail manufacturing industry, they aim to enhance competitiveness and productivity. By minimizing production costs and maximizing output efficiency, manufacturers can optimize their operations and ultimately deliver greater value to their clientele.The potential impact of [Company Name]'s carbide nail making die extends beyond the realms of industrial production. As the construction and manufacturing industries increasingly emphasize environmental sustainability, this innovative technology contributes to reducing waste by ensuring fewer defective nails and minimizing the usage of materials, ultimately reducing the environmental footprint.In conclusion, [Company Name]'s introduction of the carbide nail making die sets a new standard in the nail manufacturing industry. By harnessing the exceptional properties of carbide materials, this advanced technology enhances durability, precision, and overall productivity. As this ground-breaking innovation gains traction, manufacturers across various industries can look forward to optimizing their operations and meeting the demands of the modern market.
Tungsten Carbide Block: A Valuable Industrial Material for Various Applications
Tungsten Carbide Block Emerges as a Game-Changer in the Manufacturing IndustryTungsten carbide is a compound that combines tungsten and carbon, making it a highly versatile material for manufacturing a variety of products. The tough and durable nature of tungsten carbide makes it one of the most preferred materials for applications that require long durability, such as machine parts.Recent technological advancements in the manufacturing industry have given birth to a new product - the tungsten carbide block. These blocks, made from high-quality tungsten carbide, have become a game-changer in the manufacturing industry, as they offer unique properties that traditional materials cannot match.Tungsten carbide blocks are used in various industries, including construction, mining, and manufacturing. They have a wide range of applications that require high wear and abrasion resistance, such as manufacturing cutting tools, dies, and punches. These blocks offer superior performance and longevity compared to other carbide-based materials, making them the leading choice for toolmakers and manufacturers alike.One of the main advantages of tungsten carbide blocks is their ability to withstand high temperatures. The material has a high melting point, making it an ideal choice for applications that require high resistance to heat. Tungsten carbide blocks are also highly resistant to deformation, making them suitable for use in high-pressure environments.Additionally, tungsten carbide blocks exhibit exceptional hardness, providing high wear resistance, and low friction. This unique combination of properties makes the carbide block ideal for applications that require high-precision machining. Many industries, such as the oil and gas and mining sectors, have adopted tungsten carbide blocks due to their outstanding performance in harsh environments.Leading tungsten carbide block manufacturers pride themselves in producing exceptional quality blocks. They focus on using only the best raw materials and state-of-the-art technology to ensure that their blocks meet the most stringent quality standards. This quality-oriented approach has enabled manufacturers to remain the go-to source for manufacturers seeking high-quality tungsten carbide blocks.Tungsten carbide blocks come in different shapes and sizes, catering to various manufacturing applications. Manufacturers can order customized blocks tailored to their specific needs, with varying grades of tungsten carbide to suit the specific application. Additionally, manufacturers can request blocks with different surface finishes to enhance their resistance to wear and corrosion.The growing demand for tungsten carbide blocks has prompted many companies to invest in advanced technology to streamline their production processes. These investments have enabled manufacturers to produce tungsten carbide blocks faster without compromising on quality. Automation has also helped manufacturers to reduce production costs while improving their output.The adoption of tungsten carbide blocks has revolutionized the manufacturing industry, providing manufacturers with cutting-edge technology that improves production performance, longevity, and accuracy. Manufacturers in various industries now have access to a broad range of options to choose from, ensuring that they get the precise block they need for their specific applications.Moreover, by using tungsten carbide blocks, manufacturers can enhance their bottom lines by reducing their production costs and improving the quality of their products. Tungsten carbide blocks are a superior material that is cost-effective in the long run, making them an ideal choice for manufacturers who seek to maximize their profits.The future of tungsten carbide blocks looks bright, with increased investments in R&D that continue to enhance their quality, performance, and durability. Manufacturers can expect to see more advanced products that push the limits of what tungsten carbide blocks can offer.In conclusion, tungsten carbide blocks are a highly durable and versatile material that has revolutionized the manufacturing industry. With their exceptional strength, heat resistance, and wear resistance, these blocks continue to be a game-changer in many industries, providing manufacturers with a cost-effective solution that enhances their performance and bottom line. As the industry continues to invest in advanced technology, manufacturers can expect to benefit from even more innovative tungsten carbide blocks.