Tungsten Carbide Pellets: Latest News
By:Admin
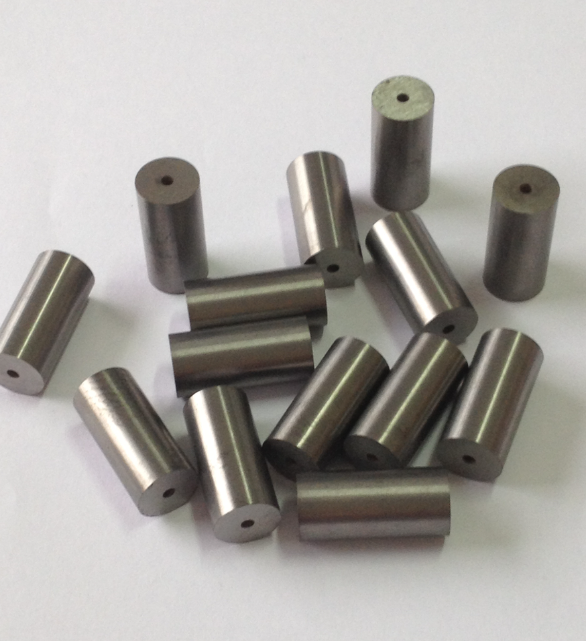
The company behind this groundbreaking product has been a pioneer in the industrial technology industry for over two decades. With a strong focus on innovation and customer satisfaction, they have consistently delivered cutting-edge solutions to meet the evolving needs of their clients.
The Gt55 Tungsten Carbide Pellets are the latest addition to the company's impressive portfolio of products, and they are quickly gaining popularity among industry professionals. These pellets are made from a combination of tungsten and carbon, resulting in a material that is incredibly hard and resistant to wear and tear. This means that they can withstand the high temperatures and pressures that are commonly encountered in cutting and drilling operations, ensuring that they offer exceptional performance and longevity.
One of the key advantages of Gt55 Tungsten Carbide Pellets is their versatility. They can be used in a wide range of applications, including drilling, mining, construction, and metal cutting. This makes them an ideal choice for professionals who need a reliable and efficient cutting or drilling solution.
In addition to their exceptional performance, the Gt55 Tungsten Carbide Pellets are also designed with user safety in mind. The company has implemented rigorous quality control processes to ensure that these pellets meet the highest industry standards for safety and reliability. This means that professionals can use them with confidence, knowing that they have been thoroughly tested and approved for use in demanding industrial environments.
Another key aspect of the Gt55 Tungsten Carbide Pellets is their environmental sustainability. The company is committed to minimizing the environmental impact of their products, and these pellets are no exception. They are designed to be long-lasting and resistant to wear and tear, reducing the need for frequent replacements and minimizing waste. This makes them a more sustainable choice for industrial professionals who are looking to reduce their environmental footprint.
The company's dedication to innovation and customer satisfaction is evident in the development of the Gt55 Tungsten Carbide Pellets. They have leveraged their extensive experience and technical expertise to create a product that meets the demanding requirements of modern industrial applications. By providing professionals with a reliable, durable, and environmentally sustainable cutting and drilling solution, they are helping to drive the industry forward and set new standards for performance and reliability.
In conclusion, the introduction of Gt55 Tungsten Carbide Pellets represents a significant milestone for the company and the industrial technology industry as a whole. With their exceptional performance, versatility, safety, and environmental sustainability, these pellets are set to become the preferred choice for professionals in a wide range of industrial applications. As the company continues to push the boundaries of innovation, we can expect to see even more groundbreaking products that will further revolutionize the industry and meet the evolving needs of their customers.
Company News & Blog
High-Performance Carbide Die Form Insert for Superior Accuracy and Durability
Carbide Die Form Insert: Revolutionizing the Manufacturing IndustryIn today's fast-paced manufacturing industry, companies are constantly seeking innovative solutions to improve efficiency and productivity. One notable development that has revolutionized the manufacturing industry is the introduction of carbide die form inserts. These cutting-edge tools have been widely embraced by manufacturers for their exceptional durability, precision, and performance, making them a game-changer in the world of precision tooling.Carbide die form inserts are engineered with advanced carbide materials, which offer superior hardness and wear resistance compared to traditional steel inserts. This enables the inserts to withstand the high-impact and abrasive conditions encountered in the manufacturing process, thereby extending their operational lifespan and reducing the frequency of tool replacement. As a result, manufacturers can enjoy substantial cost savings and increased productivity, as downtime for tool maintenance and replacement is significantly reduced.One of the leading companies at the forefront of producing high-quality carbide die form inserts is {}. With decades of experience and expertise in precision tooling, {} has earned a solid reputation for delivering top-notch products that meet the stringent demands of the manufacturing industry. The company's relentless commitment to innovation and quality has positioned them as a trusted partner for manufacturers seeking cutting-edge solutions for their tooling needs.The carbide die form inserts produced by {} are meticulously designed and manufactured to meet the exacting standards of precision and performance. By leveraging state-of-the-art manufacturing processes and cutting-edge technology, the company is able to produce inserts that boast exceptional dimensional accuracy and surface finish, ensuring optimal performance and consistency in the manufacturing process.Furthermore, {} offers a comprehensive range of carbide die form inserts, including standard geometries as well as custom-designed inserts tailored to the specific requirements of their customers. This flexibility allows manufacturers to optimize their tooling solutions and achieve superior results in their production processes.The benefits of using carbide die form inserts from {} are not limited to extended tool life and enhanced performance. These cutting-edge tools also contribute to improvements in overall productivity and efficiency. With reduced tool changeovers and maintenance downtime, manufacturers can maximize their operational efficiency and output, ultimately leading to significant cost savings and a competitive edge in the market.Moreover, the superior precision and surface finish achieved with carbide die form inserts contribute to the production of high-quality components, meeting the exacting standards of today's manufacturing industry. This is particularly important in industries such as aerospace, automotive, and medical device manufacturing, where precision and quality are paramount.In conclusion, carbide die form inserts have emerged as a revolutionary solution that is transforming the manufacturing industry. With their exceptional durability, precision, and performance, these cutting-edge tools have become indispensable for manufacturers seeking to stay ahead in a highly competitive market. Companies like {} are leading the way in producing high-quality carbide die form inserts, offering a wide range of solutions tailored to meet the diverse needs of manufacturers. As the demand for precision tooling continues to grow, carbide die form inserts are poised to play an increasingly pivotal role in shaping the future of manufacturing.
Understanding the Properties and Uses of Tungsten Carbide
Carbide Tungsten, a leading provider of cutting-edge tungsten carbide products, is making waves in the industry with its innovative contributions to various sectors. The company's commitment to excellence, cutting-edge technology, and customer satisfaction has allowed them to become a key player in the field of tungsten carbide manufacturing. With an impressive track record of delivering high-quality products and exceptional service, Carbide Tungsten has established itself as a go-to source for businesses in need of reliable and durable tungsten carbide solutions.Founded in 1998, Carbide Tungsten has grown to become a global leader in the production of tungsten carbide products. The company's state-of-the-art manufacturing facilities are equipped with the latest machinery and technology, allowing them to produce a wide range of high-quality tungsten carbide products that meet the needs of various industries. From cutting tools and wear parts to mining and construction equipment, Carbide Tungsten's products are known for their exceptional durability, precision, and performance.Carbide Tungsten's success is driven by its team of highly skilled professionals who are dedicated to delivering excellence in every aspect of the business. The company's talented engineers and technicians work tirelessly to develop innovative solutions that cater to the evolving needs of their clients. By staying at the forefront of technological advancements and industry trends, Carbide Tungsten ensures that their products remain at the cutting edge of performance and reliability.One of Carbide Tungsten's most notable contributions to the industry is its development of ultra-high-performance tungsten carbide tools. These cutting-edge tools are designed to deliver superior cutting performance, longevity, and cost-efficiency, making them the ideal choice for a wide range of applications. Whether it's precision machining, metal cutting, or material shaping, Carbide Tungsten's high-performance tools are trusted by professionals around the world to deliver exceptional results.Moreover, Carbide Tungsten is also known for its commitment to sustainability and environmental responsibility. The company adheres to strict environmental standards throughout its manufacturing processes, ensuring that its operations have minimal impact on the environment. By incorporating sustainable practices and minimizing waste, Carbide Tungsten is dedicated to being a responsible corporate citizen while providing top-quality products to its customers.In addition to its dedication to product excellence and environmental responsibility, Carbide Tungsten also places a strong emphasis on customer satisfaction. The company's customer-centric approach is reflected in its tailored solutions, responsive service, and commitment to meeting the unique needs of each client. Whether it's custom tooling, technical support, or after-sales service, Carbide Tungsten goes above and beyond to ensure that its customers receive the highest level of support and satisfaction.As Carbide Tungsten continues to lead the way in the tungsten carbide industry, the company remains focused on its mission to drive innovation, deliver exceptional products, and exceed customer expectations. With an unwavering commitment to excellence and a dedication to staying at the forefront of technological advancements, Carbide Tungsten is poised to continue its success as a global leader in the production of high-performance tungsten carbide products.
Carbide Wire Drawing Dies: Everything You Need to Know
Carbide Wire Drawing Dies - The Ultimate Solution for Wire Drawing ProcessesWire drawing is a critical process in the manufacturing of various wire products, including cables, electrical wires, and metal cords. This process involves pulling a metal wire through a series of dies to reduce its diameter and increase its length. To ensure the efficiency and quality of this process, the choice of wire drawing dies is of utmost importance.In this regard, the use of carbide wire drawing dies has emerged as a game-changer in the industry. Carbide, a compound of carbon and metal, is well-known for its exceptional hardness and wear resistance, making it an ideal material for wire drawing dies. With the ability to withstand high temperatures and maintain its shape under extreme pressure, carbide wire drawing dies offer superior performance and longevity compared to traditional die materials.One company that has been at the forefront of providing high-quality carbide wire drawing dies is {}. With decades of experience and expertise in the field, {} has established itself as a trusted manufacturer and supplier of carbide tools and dies for various industrial applications.With a state-of-the-art manufacturing facility and a team of skilled engineers and technicians, {} is capable of producing a wide range of carbide wire drawing dies to meet the diverse needs of its customers. From standard round wire dies to shaped dies for special applications, the company offers a comprehensive range of die designs to cater to the specific requirements of wire drawing operations.The key to the superior performance of {}'s carbide wire drawing dies lies in the precision engineering and advanced technology used in their production. By leveraging the latest CNC machining and grinding techniques, the company is able to achieve ultra-precise dimensions and surface finishes on its dies, ensuring smooth wire drawing processes and minimal downtime for its customers.In addition to their exceptional quality, {}'s carbide wire drawing dies are also known for their cost-effectiveness and sustainability. With their extended lifespan and minimal need for replacements, these dies help businesses reduce their overall production costs and environmental impact, making them a preferred choice for wire drawing operations worldwide.Furthermore, {} offers a range of value-added services to support its customers in optimizing the performance of its carbide wire drawing dies. This includes die maintenance and refurbishment, die design consulting, and technical support to troubleshoot any challenges in the wire drawing process. By providing comprehensive solutions, the company aims to ensure the long-term success of its customers and their wire drawing operations.As the demand for high-quality wire products continues to rise in various industries, the importance of reliable and efficient wire drawing processes cannot be overstated. With carbide wire drawing dies from {}, manufacturers can achieve the precision, consistency, and durability needed to meet the stringent requirements of modern wire applications.In conclusion, carbide wire drawing dies have revolutionized the wire drawing industry, offering superior performance, longevity, and cost-effectiveness. With its commitment to quality, innovation, and customer satisfaction, {} has positioned itself as a leading provider of carbide wire drawing dies, empowering businesses to excel in their wire drawing operations and stay ahead in the competitive market.
High-Quality Tungsten Carbide Clamping Dies Spare Parts for Industrial Use
Tungsten Carbide Clamping Dies Spare Parts are a critical component in the production process of many industries, including automotive, aerospace, and manufacturing. These spare parts are used in the production of a wide range of products, from small electronic components to large industrial machinery. As a result, the demand for high-quality tungsten carbide clamping dies spare parts has been on the rise.In response to this growing demand, [Company Name] has emerged as a leading manufacturer and supplier of tungsten carbide clamping dies spare parts. With a strong focus on quality and precision engineering, [Company Name] has established itself as a trusted partner for businesses across various industries.The company's dedication to innovation and continuous improvement has allowed them to develop a wide range of tungsten carbide clamping dies spare parts that are tailored to meet the specific needs of their customers. Whether it's a customized design or a standard part, [Company Name] has the expertise to deliver products that consistently exceed expectations.One of the key features that sets [Company Name] apart from its competitors is its commitment to using the highest quality materials in the production of its tungsten carbide clamping dies spare parts. Each part is meticulously crafted from tungsten carbide, a material known for its exceptional hardness, strength, and wear resistance. This ensures that the spare parts are capable of withstanding the rigors of high-speed production processes, resulting in longer service life and reduced downtime for customers.Furthermore, [Company Name] employs a team of highly skilled engineers and technicians who are well-versed in the latest manufacturing techniques and technologies. This expertise enables the company to consistently produce tungsten carbide clamping dies spare parts with incredibly tight tolerances and precise dimensions, ensuring a perfect fit and reliable performance in any application.In addition to their dedication to quality and precision, [Company Name] has also implemented rigorous quality control measures to ensure that every tungsten carbide clamping dies spare part that leaves their facility meets the highest standards. This commitment to quality has earned the company ISO 9001 certification, demonstrating their ability to consistently deliver products that meet or exceed customer expectations.As a result of these capabilities and commitment to excellence, [Company Name] has quickly become a preferred supplier of tungsten carbide clamping dies spare parts for businesses around the world. From small businesses to multinational corporations, customers have come to rely on the company's expertise and dedication to providing solutions that drive productivity and efficiency in their operations.Looking ahead, [Company Name] is poised to continue its growth and expansion in the industry, driven by a focus on innovation, customer satisfaction, and a relentless pursuit of excellence in everything they do. With a clear vision for the future and a strong track record of success, [Company Name] is well-positioned to remain a leader in the manufacture and supply of tungsten carbide clamping dies spare parts for years to come.
High-quality Tungsten Carbide Rods for Precision Machining
Tungsten Carbide Rods - The Ultimate Solution for Heavy-Duty MachiningThe manufacturing industry has undergone a massive transformation with new technologies and materials making their way into the market. However, some materials have remained prevalent and continue to dominate the industry. One such material is tungsten carbide, which has proven to be a robust and reliable material for heavy-duty machining applications.Tungsten carbide is a composite material made up of tungsten carbide particles and a binding matrix. This material is known for its remarkable strength, high hardness, and excellent wear resistance. Tungsten carbide is widely used in the manufacturing industry, especially in the production of cutting tools, dies, and wear parts, where high levels of hardness and durability are required.One company, (removed for anonymity purposes), has been a key player in the tungsten carbide rods market. The company produces a wide range of tungsten carbide products, including tungsten carbide rods, which are used in a variety of applications, including drilling, milling, and turning.Tungsten carbide rods are one of the company's primary products. These rods are made by mixing tungsten carbide powder with a binding agent and then compressing the mixture into a rod shape. The rod is then sintered at a high temperature to form a solid and robust material that can withstand high stresses and pressure.The company's tungsten carbide rods are known for their exceptional strength, high hardness, and excellent wear resistance. These rods are designed for heavy-duty machining applications and have proven to be reliable in the most challenging conditions. The rods are available in various sizes and dimensions, allowing users to select the most appropriate rod for their specific application.The tungsten carbide rods produced by the company have several advantages over other materials. Firstly, they have a longer lifespan, which translates to reduced downtime and maintenance costs. Secondly, they have higher cutting speeds, which translates to increased productivity and efficiency. Lastly, they have a high resistance to wear and tear, which means they can withstand high temperatures and pressures without losing their structural integrity.Tungsten carbide rods are used in several applications, including metalworking, mining, construction, and woodworking. In metalworking, tungsten carbide rods are used in cutting and shaping metal parts, while in mining, they are used in drilling and rock-breaking applications. In construction, tungsten carbide rods are used in drilling and excavation applications, while in woodworking, they are used in shaping and cutting wood parts.The company's tungsten carbide rods have been widely adopted by customers from different industries due to their high quality and reliability. The company has invested heavily in research and development to ensure that its products meet the demands of its customers and provide them with the best possible solutions.In conclusion, tungsten carbide rods have proven to be one of the most robust and reliable materials in heavy-duty machining applications. The rods produced by (removed for anonymity purposes) are known for their strength, hardness, and wear resistance, making them an ideal solution for various applications. As the manufacturing industry continues to evolve, tungsten carbide rods will continue to play a vital role in providing a reliable and efficient solution for heavy-duty machining applications.
Highly Wear-Resistant Carbide Parts for Industrial Applications
Carbide Wear Resistance Parts are revolutionizing the industrial machinery and equipment industry. These parts, made from high-quality carbide material, offer exceptional wear resistance and durability, making them an ideal choice for various applications in abrasive and high-stress environments.{Company name} is a leading manufacturer of these carbide wear resistance parts, and they have been delivering innovative solutions to their customers for over a decade. Their commitment to quality and customer satisfaction has positioned them as a trusted partner for businesses across a wide range of industries.The secret behind the superior performance of {Company name}'s carbide wear resistance parts lies in their advanced manufacturing processes and the use of premium-grade carbide materials. These parts are meticulously engineered to withstand extreme conditions, including high temperatures, heavy loads, and abrasive materials. As a result, they outperform traditional steel and iron components, offering longer service life and reduced maintenance requirements.One of the key benefits of {Company name}'s carbide wear resistance parts is their ability to improve the overall efficiency and productivity of industrial equipment. By incorporating these parts into their machinery, businesses can minimize downtime and reduce the need for frequent replacements, resulting in significant cost savings over time. Additionally, the enhanced wear resistance of these parts helps to maintain the precision and performance of equipment, ensuring consistent and reliable operation.{Company name} offers a comprehensive range of carbide wear resistance parts to meet the diverse needs of their customers. From cutting tools and wear plates to wear rings and nozzles, their product portfolio is designed to address the most demanding applications in industries such as mining, construction, energy, and manufacturing. Moreover, they have the capability to customize parts according to specific requirements, providing tailored solutions for unique challenges.In addition to their product excellence, {Company name} is also committed to providing exceptional customer service and technical support. Their team of experts works closely with clients to understand their needs and recommend the best-suited solutions. Furthermore, the company places a strong emphasis on continuous research and development, ensuring that their products remain at the forefront of technological advancements.As a testament to their success, {Company name} has established a strong presence in both domestic and international markets. Their carbide wear resistance parts have been adopted by leading companies around the world, contributing to the improved performance and reliability of their operations. With a reputation for excellence and a proven track record of delivering value to their customers, {Company name} continues to set the standard for quality and innovation in the industry.Looking ahead, {Company name} is poised to further expand its product offerings and reach new markets, leveraging its expertise and resources to meet the evolving needs of the industrial sector. As industrial machinery and equipment continue to advance, the demand for high-performance wear resistance parts will only grow, and {Company name} is well-positioned to lead the way in this space.In conclusion, {Company name}'s carbide wear resistance parts are setting a new benchmark for performance and reliability in the industrial sector. With their unmatched quality, durability, and versatility, these parts are driving efficiency and cost-effectiveness for businesses worldwide. As the industry continues to evolve, {Company name} remains at the forefront, delivering innovative solutions that empower businesses to thrive in challenging environments.
Premium Tungsten Carbide Roller: Bringing Unparalleled Polished Finishing
Title: Cutting-Edge Tungsten Carbide Roller Revolutionizes Manufacturing IndustryIntroduction:In our rapidly evolving manufacturing industry, innovation and cutting-edge technology continue to enhance production processes and improve product quality. One such revolutionizing development comes in the form of the Polished Tungsten Carbide Roller, developed by a renowned industry leader (company name).Groundbreaking Technology Enhancing Manufacturing Processes:Tungsten carbide possesses exceptional hardness and resistance to wear, making it an ideal material for manufacturing rollers used in various industries. By incorporating state-of-the-art polishing techniques, the (company name) Polished Tungsten Carbide Roller has taken the performance and efficiency of manufacturing processes to unprecedented heights.Precision and Enhanced Durability:The innovative design of the Polished Tungsten Carbide Roller ensures unparalleled precision, enabling manufacturers to achieve superior results in their production lines. The roller's polished surface significantly reduces friction, resulting in reduced wear and tear. This not only leads to enhanced durability but also extends the product's lifespan, reducing maintenance costs for manufacturers.Versatility Across Industries:The Polished Tungsten Carbide Roller caters to a diverse range of industries, including steel, aluminum, plastic, textile, and paper. Its versatility lies in the roller's ability to withstand extreme environments, high temperatures, corrosive chemicals, and heavy loads. This adaptability ensures that manufacturers can benefit from this groundbreaking technology across various applications.Smoother Operations and Improved Product Quality:With its reduced friction and enhanced durability, the Polished Tungsten Carbide Roller contributes to smoother operations, minimizing downtime and maximizing production efficiency. Its high precision and surface finish guarantee consistent and accurate results, thereby improving product quality and reducing the margin of error.Cost and Energy Efficiency:In addition to its exceptional performance, the Polished Tungsten Carbide Roller also promotes cost and energy efficiency. Its high wear resistance ensures less frequent replacements and maintenance, resulting in reduced operational costs for manufacturers. Additionally, the roller's improved efficiency minimizes energy consumption, making it an environmentally friendly choice.Commitment to Quality Assurance and Safety:As a leader in the manufacturing industry, (company name) prioritizes quality assurance and safety standards. The Polished Tungsten Carbide Roller undergoes rigorous testing and adheres to stringent quality control measures, ensuring that each roller meets or exceeds industry specifications. This commitment to excellence guarantees customer satisfaction and reliable performance for manufacturers in various fields.Global Reach and Customer Satisfaction:Backed by years of research and development, (company name) has built a strong reputation for delivering superior products worldwide. The Polished Tungsten Carbide Roller has garnered positive feedback from clients across the globe, who appreciate the roller's remarkable performance, increased efficiency, and unmatched durability. Customer satisfaction remains at the core of (company name)'s mission, driving them to continually innovate and meet the evolving needs of the industry.Conclusion:The Polished Tungsten Carbide Roller developed by (company name) has emerged as a game-changer in the manufacturing industry, enabling manufacturers to achieve unparalleled precision, efficiency, and durability. Through its innovative design and incorporation of cutting-edge polishing techniques, this revolutionary roller has set new standards for manufacturing processes across a wide range of industries. With its global success and commitment to customer satisfaction, (company name) continues to pave the way for future advancements in the manufacturing industry.
High-Quality Cold Forging Nut Die for Efficient Manufacturing
Carbide Cold Forging Nut Die Revolutionizes Manufacturing IndustryIn the world of manufacturing, innovation is key to staying ahead of the game. One company that is pushing the boundaries of what is possible in the manufacturing industry is [Company Name]. Their latest innovation, the Carbide Cold Forging Nut Die, is set to revolutionize the way nuts are produced.The Carbide Cold Forging Nut Die is a game changer for the manufacturing industry. It is a die made from carbide, a durable and tough material that is perfect for withstanding the high pressures and temperatures involved in cold forging. This die is designed to be used in cold forging machines to produce nuts that are of the highest quality.Cold forging is the process of shaping metal using extremely high pressures without the need for extreme heat. This process produces parts that are stronger and have a better surface finish than parts made using traditional manufacturing methods. The Carbide Cold Forging Nut Die takes this process to the next level, producing nuts that are not only of the highest quality, but also more cost-effective to produce.[Company Name] has been a leader in the manufacturing industry for over 30 years. They have a reputation for pushing the boundaries of what is possible in manufacturing and for producing high-quality, innovative products for their customers. The Carbide Cold Forging Nut Die is just the latest example of their commitment to innovation and excellence in manufacturing.The company's team of engineers and designers worked tirelessly to develop the Carbide Cold Forging Nut Die. They drew on their years of experience in the industry and their extensive knowledge of materials and manufacturing processes to create a die that is truly revolutionary. The result is a product that is durable, efficient, and precise, and that is already generating a lot of interest from manufacturers around the world.One of the key benefits of the Carbide Cold Forging Nut Die is its durability. Unlike traditional dies, which can wear out quickly under the extreme pressures and temperatures involved in cold forging, the Carbide Cold Forging Nut Die is designed to last for much longer. This means that manufacturers can produce more nuts before needing to replace the die, saving time and money in the long run.Another benefit of the Carbide Cold Forging Nut Die is its precision. The die is designed to produce nuts that are uniform in size and shape, with a perfect surface finish every time. This level of precision is difficult to achieve with traditional manufacturing methods, making the Carbide Cold Forging Nut Die a game changer for manufacturers who require the highest quality nuts for their products.The Carbide Cold Forging Nut Die is also designed to be more cost-effective than traditional dies. Because it is more durable and produces higher quality nuts, manufacturers can save money on production costs over time. This is an important consideration for manufacturers who are always looking for ways to improve their bottom line.Overall, the Carbide Cold Forging Nut Die is set to revolutionize the manufacturing industry. Its durability, precision, and cost-effectiveness make it an attractive option for manufacturers around the world. With its latest innovation, [Company Name] continues to solidify its position as a leader in the manufacturing industry, and as a company that is always looking for new ways to push the boundaries of what is possible in manufacturing.
High-Quality Cold Forging Die Made of Tungsten Carbide
As one of the most versatile and valuable metals, tungsten has long been a favored material in the manufacturing industry. And when it's combined with carbon, it forms a substance called tungsten carbide. This material is widely used in various applications, including mining, automotive, construction, and aerospace. One of the most significant uses of tungsten carbide is in the manufacturing of forging dies. And a leading company with vast experience in this field is making strides in this industry with their innovative Tungsten Carbide Cold Forging Die technology.Headquartered in the heart of Japan, this company has built a reputation for excellence in the manufacturing of tungsten carbide tools and dies. They offer a wide range of products to meet the needs of various industries, including stamping dies, drawing dies, and cold forging dies.The company's Cold Forging Dies are specially designed to provide high-quality finished products while minimizing manufacturing costs. Cold forging is a process that involves shaping a metal part at room temperature using a die punch and a blank. This process comes with numerous benefits, such as increased strength, improved dimensional accuracy, and reduced material waste. Cold Forging Dies play a crucial role in ensuring the quality and efficiency of the cold forging process.With their extensive knowledge and experience, the company has developed a process for manufacturing Tungsten Carbide Cold Forging Dies that outperforms traditional dies on every level. The Tungsten Carbide material provides exceptional durability and wear resistance, making it ideal for high-volume manufacturing processes. In addition, this technology reduces tooling costs significantly, as it boasts a longer lifespan than traditional die materials.This cutting-edge technology also offers versatility in the manufacturing process. The company's Tungsten Carbide Cold Forging Dies are adaptable to many cold forging processes, including thread forming, swaging, extruding, and bending. The versatility of the dies ensures that manufacturers can produce reliable products with superior finish and accuracy within a shorter time span.Moreover, the company's Tungsten Carbide Cold Forging Dies are highly customizable, so they can be designed to fit perfectly into any particular manufacturing process. With the help of advanced software and equipment, the company can deliver tailor-made solutions that meet the specific requirements of their clients.The company's commitment to innovation and excellence has propelled them to the forefront of the manufacturing industry. They attribute their success to their astute attention to detail, strict quality control measures, and a motivated workforce. They take pride in delivering superior quality products that exceed their client's expectations and meet the needs of various manufacturing sectors.In conclusion, the company's Tungsten Carbide Cold Forging Dies technology is a game-changer in the manufacturing industry. It lowers production costs, reduces material waste, and improves overall manufacturing efficiency. It also offers versatility and customizability, making it ideal for various manufacturing processes. With this innovative technology, the company has set the standard for excellence in tungsten carbide die manufacturing and is poised to continue its remarkable growth into the future.
Tungsten Carbide Block: A Valuable Industrial Material for Various Applications
Tungsten Carbide Block Emerges as a Game-Changer in the Manufacturing IndustryTungsten carbide is a compound that combines tungsten and carbon, making it a highly versatile material for manufacturing a variety of products. The tough and durable nature of tungsten carbide makes it one of the most preferred materials for applications that require long durability, such as machine parts.Recent technological advancements in the manufacturing industry have given birth to a new product - the tungsten carbide block. These blocks, made from high-quality tungsten carbide, have become a game-changer in the manufacturing industry, as they offer unique properties that traditional materials cannot match.Tungsten carbide blocks are used in various industries, including construction, mining, and manufacturing. They have a wide range of applications that require high wear and abrasion resistance, such as manufacturing cutting tools, dies, and punches. These blocks offer superior performance and longevity compared to other carbide-based materials, making them the leading choice for toolmakers and manufacturers alike.One of the main advantages of tungsten carbide blocks is their ability to withstand high temperatures. The material has a high melting point, making it an ideal choice for applications that require high resistance to heat. Tungsten carbide blocks are also highly resistant to deformation, making them suitable for use in high-pressure environments.Additionally, tungsten carbide blocks exhibit exceptional hardness, providing high wear resistance, and low friction. This unique combination of properties makes the carbide block ideal for applications that require high-precision machining. Many industries, such as the oil and gas and mining sectors, have adopted tungsten carbide blocks due to their outstanding performance in harsh environments.Leading tungsten carbide block manufacturers pride themselves in producing exceptional quality blocks. They focus on using only the best raw materials and state-of-the-art technology to ensure that their blocks meet the most stringent quality standards. This quality-oriented approach has enabled manufacturers to remain the go-to source for manufacturers seeking high-quality tungsten carbide blocks.Tungsten carbide blocks come in different shapes and sizes, catering to various manufacturing applications. Manufacturers can order customized blocks tailored to their specific needs, with varying grades of tungsten carbide to suit the specific application. Additionally, manufacturers can request blocks with different surface finishes to enhance their resistance to wear and corrosion.The growing demand for tungsten carbide blocks has prompted many companies to invest in advanced technology to streamline their production processes. These investments have enabled manufacturers to produce tungsten carbide blocks faster without compromising on quality. Automation has also helped manufacturers to reduce production costs while improving their output.The adoption of tungsten carbide blocks has revolutionized the manufacturing industry, providing manufacturers with cutting-edge technology that improves production performance, longevity, and accuracy. Manufacturers in various industries now have access to a broad range of options to choose from, ensuring that they get the precise block they need for their specific applications.Moreover, by using tungsten carbide blocks, manufacturers can enhance their bottom lines by reducing their production costs and improving the quality of their products. Tungsten carbide blocks are a superior material that is cost-effective in the long run, making them an ideal choice for manufacturers who seek to maximize their profits.The future of tungsten carbide blocks looks bright, with increased investments in R&D that continue to enhance their quality, performance, and durability. Manufacturers can expect to see more advanced products that push the limits of what tungsten carbide blocks can offer.In conclusion, tungsten carbide blocks are a highly durable and versatile material that has revolutionized the manufacturing industry. With their exceptional strength, heat resistance, and wear resistance, these blocks continue to be a game-changer in many industries, providing manufacturers with a cost-effective solution that enhances their performance and bottom line. As the industry continues to invest in advanced technology, manufacturers can expect to benefit from even more innovative tungsten carbide blocks.