Tungsten Carbide Cold Heading Die for YG8 Material
By:Admin
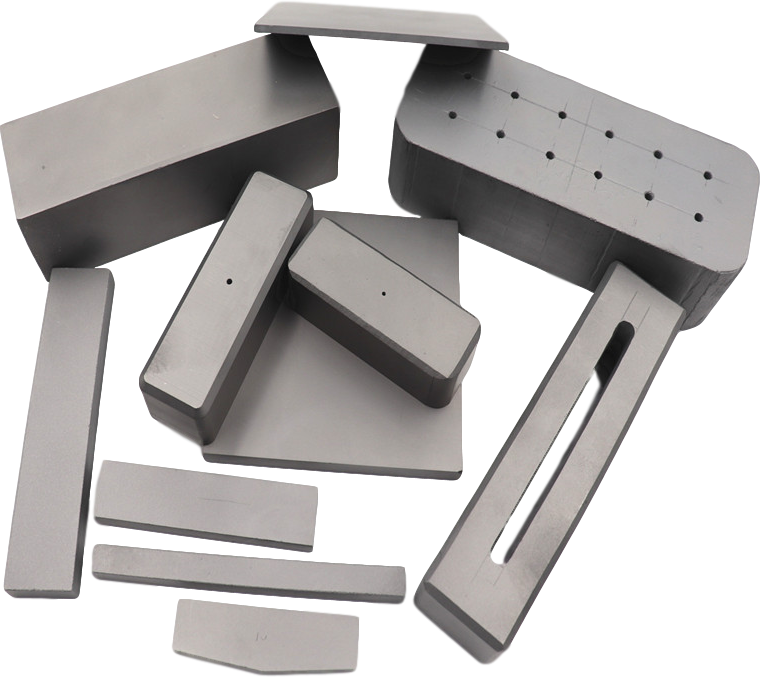
Cold heading is a process that involves the shaping of metal blanks using a punch and die. This process is widely used in the production of bolts, screws, and other fasteners, as well as in the automotive, aerospace, and construction industries. The quality and accuracy of the cold heading dies used in this process are crucial in determining the quality of the finished products.
The YG8 tungsten carbide cold heading dies have gained widespread recognition for their exceptional performance and durability. Tungsten carbide is a hard and dense material that is renowned for its high strength, wear resistance, and thermal conductivity. These properties make it an ideal choice for cold heading dies, as it can withstand the high pressures and repeated impacts involved in the cold heading process.
The YG8 grade of tungsten carbide is particularly well-suited for cold heading applications, as it offers a balance of hardness and toughness. This allows the dies to maintain their sharpness and dimensional accuracy even after prolonged use, resulting in consistent and high-quality production output.
Furthermore, the YG8 tungsten carbide cold heading dies are designed to minimize the risk of breakage and deformation, which can lead to costly downtime and tooling replacement. This reliability is essential for manufacturers seeking to maximize productivity and efficiency in their cold heading operations.
In addition to their exceptional performance, the YG8 tungsten carbide cold heading dies are also known for their versatility. They can be customized to produce a wide range of fastener types and sizes, allowing manufacturers to meet diverse production requirements with a single set of dies. This capability has made the YG8 tungsten carbide cold heading dies a preferred choice for many leading manufacturers in the industry.
One company that has been at the forefront of producing high-quality YG8 tungsten carbide cold heading dies is [Company Name]. With a strong focus on research and development, [Company Name] has been able to leverage the latest advancements in material science and manufacturing technology to create innovative solutions for the cold heading industry.
[Company Name] has built a solid reputation for its commitment to quality and customer satisfaction. The company's team of experienced engineers and technicians work closely with clients to understand their specific cold heading requirements and provide tailored solutions that optimize production efficiency and reduce overall costs.
Moreover, [Company Name] has invested heavily in state-of-the-art manufacturing facilities and quality control processes to ensure that its YG8 tungsten carbide cold heading dies meet the highest standards of precision and reliability. This dedication to excellence has earned [Company Name] the trust and confidence of customers across the globe.
In conclusion, the development of YG8 tungsten carbide cold heading dies has significantly raised the bar for cold heading performance and efficiency. With their outstanding durability, precision, and versatility, these dies have become a game-changer for manufacturers seeking to enhance their cold heading operations.
As industry leaders like [Company Name] continue to push the boundaries of innovation, the future looks promising for the cold heading industry, with the potential for even more advanced materials and technologies to further improve production processes and expand the capabilities of cold heading operations.
Company News & Blog
The Ultimate Guide to Tungsten Carbide Strips - Unveiling the Power of HR6A
Title: HR6A Tungsten Carbide Strips Revolutionizing Industrial ApplicationsIntroduction:In the competitive landscape of industrial manufacturing, quality and efficient tools are essential for achieving productivity and precision. One such innovation is the HR6A Tungsten Carbide Strips. With their exceptional hardness, wear resistance, and versatility, these carbide strips have been gaining attention in various industries. This article aims to shed light on the remarkable features of HR6A Tungsten Carbide Strips and their potential to revolutionize industrial applications.I. Understanding Tungsten Carbide:Tungsten carbide is a compound comprising equal parts of carbon and tungsten. Known for its extreme hardness, it is approximately three times harder than steel and can withstand high temperatures and abrasion. These characteristics make it an ideal material for manufacturing cutting tools, wear-resistant parts, and other industrial applications.II. HR6A Tungsten Carbide Strips:HR6A Tungsten Carbide Strips exemplify the superior properties of tungsten carbide. These strips are fabricated using advanced techniques, resulting in an exceptional combination of toughness, hardness, and wear resistance.1. Unparalleled Hardness:The HR6A Tungsten Carbide Strips possess an impressive hardness that allows them to cut through the toughest materials with ease. This hardness provides extended tool life and reduces downtime due to frequent tool replacements.2. Exceptional Wear Resistance:The wear resistance of HR6A Tungsten Carbide Strips ensures their durability even in harsh working conditions. Whether it is cutting, drilling, or shaping, these strips retain their sharpness, reducing the need for frequent replacements and enhancing overall productivity.3. Versatility in Applications:These carbide strips find applications in a wide range of industries. From machining and metalworking to mining and construction, the versatility of HR6A Tungsten Carbide Strips makes them an invaluable tool for various industrial applications.III. Industrial Applications and Benefits:The HR6A Tungsten Carbide Strips offer a myriad of benefits across several industries, maximizing efficiency, productivity, and overall performance.1. Machining and Metalworking Sector:In the metalworking industry, HR6A Tungsten Carbide Strips are widely used in cutting, planing, milling, and turning tools. Their high heat resistance and hardness enable precision machining, resulting in superior surface finishes and increased manufacturing speed.2. Mining and Construction Industry:In the mining and construction industry, HR6A Tungsten Carbide Strips are employed in the production of drilling tools and machinery parts. Their exceptional wear resistance ensures consistent performance, extended tool life, and reduced downtime, resulting in improved operational efficiency and cost-effectiveness.3. Woodworking and Plastic Processing:For woodworking and plastic processing applications, HR6A Tungsten Carbide Strips are used in cutting and shaping tools. Their hardness and abrasion resistance enable precise cutting, reduced material waste, and improved surface quality.IV. Outlook and Future Implications:The introduction of HR6A Tungsten Carbide Strips signifies a significant advancement in the industrial manufacturing sector. With their exceptional hardness, wear resistance, and versatility, these strips have the potential to redefine precision machining, mining, construction, and woodworking applications.The continuous research and development in tungsten carbide technology will likely lead to further enhancements in the performance and overall effectiveness of HR6A Tungsten Carbide Strips. As industries increasingly demand high-quality tools that combine durability, precision, and versatility, the future of HR6A Tungsten Carbide Strips looks promising.Conclusion:The HR6A Tungsten Carbide Strips have emerged as a game-changer in the industrial manufacturing landscape. With their unparalleled hardness, exceptional wear resistance, and versatility in various applications, these carbide strips are elevating the standards of precision machining, mining, construction, woodworking, and more. As the industry continues to embrace innovative solutions, HR6A Tungsten Carbide Strips will undoubtedly play a vital role in shaping the future of industrial applications.
The Advantages and Applications of Cemented Carbide YG15: A Comprehensive Guide
In recent news, a cemented carbide manufacturer has made significant progress in the development of their product - YG15 (brand name removed). The YG15 cemented carbide is a highly durable and wear-resistant material that is widely used in the manufacturing industry for various components.The YG15 cemented carbide is an alloy made from a combination of tungsten carbide and cobalt powder, which is blended together and then subjected to a sintering process to produce a solid, hard-wearing material. The YG15 cemented carbide has been tested against various types of wear and tear, including abrasion, corrosion, and impact, and has been found to be highly resistant against all forms of wear and tear.One of the unique features of YG15 cemented carbide is its excellent resistance to abrasion. Abrasion is a type of wear that is caused by the rubbing or scraping of two surfaces against each other, which can result in the surface becoming rough and dull. This type of wear can be particularly problematic in industrial applications, where components are subjected to constant abrasion, leading to high levels of wear and tear.YG15 cemented carbide is also highly resistant to corrosion, which is the process of materials gradually deteriorating due to exposure to environmental factors such as moisture, temperature, and chemicals. This makes YG15 cemented carbide an ideal material for use in harsh environments, such as those found in the oil and gas industry, where components are exposed to corrosive fluids.In addition to its excellent resistance to wear and tear, YG15 cemented carbide is also known for its high strength and durability. This makes it an ideal material for use in high-stress applications, such as those found in the aerospace and automotive industries.One of the key benefits of YG15 cemented carbide is its ability to be shaped and formed into various components. This makes it a versatile material that can be used to manufacture a wide range of products, including cutting tools, wear parts, and industrial machinery components.The manufacturer of YG15 cemented carbide prides itself on producing a high-quality product that is consistently reliable and meets the needs of its customers. The company has invested heavily in research and development to ensure that its products are at the forefront of technological advancements.In addition to providing high-quality products, the manufacturer of YG15 cemented carbide places a great deal of emphasis on customer service and support. This includes providing expert advice on product selection, as well as offering technical support and troubleshooting services to help customers get the most out of their products.Overall, YG15 cemented carbide is a highly durable and wear-resistant material that is widely used in the manufacturing industry for various components. Its excellent resistance to abrasion and corrosion, as well as its high strength and durability, make it an ideal material for use in high-stress applications. With its consistent reliability and commitment to customer service and support, the manufacturer of YG15 cemented carbide is a trusted and respected name in the industry.
Durable and Versatile Cemented Carbide Brazed Flakes - A Must-Have for Industrial Applications
Cemented Carbide Brazed Flakes have revolutionized the metalworking industry with their superior cutting performance and durability. These innovative tools are made by brazing small pieces of cemented carbide onto a larger substrate, creating a strong and reliable cutting edge that can withstand high temperatures and heavy loads. One company at the forefront of this technology is {}. With decades of experience in the development and manufacturing of cutting tools, {} has established itself as a leader in the industry. The company's dedication to quality and innovation has led to the creation of a wide range of cutting tools, including Cemented Carbide Brazed Flakes, that have been instrumental in improving the efficiency and productivity of metalworking operations across the globe.The success of {} can be attributed to its state-of-the-art manufacturing facilities and a team of highly skilled engineers and technicians who are constantly pushing the boundaries of cutting tool technology. These resources have allowed the company to develop and produce Cemented Carbide Brazed Flakes that are unmatched in performance and reliability.One of the key benefits of Cemented Carbide Brazed Flakes is their ability to maintain their cutting edge even when working with the most abrasive and challenging materials. Whether it is machining hardened steel, cast iron, or high-temperature alloys, these cutting tools deliver exceptional performance and longevity, ultimately reducing downtime and increasing productivity for metalworking operations.Furthermore, {}'s Cemented Carbide Brazed Flakes are designed to provide precise and consistent cutting results, ensuring that each workpiece meets the required specifications. This level of accuracy and reliability is crucial in industries such as aerospace, automotive, and mold and die making, where components must meet strict tolerances and quality standards.The durability of Cemented Carbide Brazed Flakes also contributes to significant cost savings for metalworking companies. With longer tool life and reduced frequency of tool changes, businesses can minimize their tooling expenses and improve their overall operational efficiency. Additionally, the consistent performance of these cutting tools leads to higher-quality machined components, reducing scrap rates and rework, ultimately boosting the bottom line for metalworking operations.In addition to the technical superiority of its Cemented Carbide Brazed Flakes, {} offers unparalleled customer support and technical expertise. The company's team of application engineers and sales professionals work closely with customers to understand their unique machining challenges and provide tailored solutions that optimize their cutting processes. This level of customer commitment has earned {} a reputation as a trusted partner for metalworking companies around the world.Looking ahead, {} remains committed to advancing the capabilities of Cemented Carbide Brazed Flakes and other cutting tool technologies. The company continues to invest in research and development, exploring new materials, coating technologies, and geometries to further enhance the performance and versatility of its cutting tools. By staying at the forefront of innovation, {} ensures that its customers have access to the most advanced cutting solutions to meet the evolving demands of the metalworking industry.In conclusion, Cemented Carbide Brazed Flakes from {} have become an indispensable tool for metalworking operations worldwide. With their exceptional performance, durability, and precision, these cutting tools have revolutionized the way components are machined, delivering unparalleled efficiency and cost savings. Backed by the expertise and support of {}, these cutting tools are set to continue driving innovation and productivity in the metalworking industry for years to come.
Tungsten Carbide Block: A Valuable Industrial Material for Various Applications
Tungsten Carbide Block Emerges as a Game-Changer in the Manufacturing IndustryTungsten carbide is a compound that combines tungsten and carbon, making it a highly versatile material for manufacturing a variety of products. The tough and durable nature of tungsten carbide makes it one of the most preferred materials for applications that require long durability, such as machine parts.Recent technological advancements in the manufacturing industry have given birth to a new product - the tungsten carbide block. These blocks, made from high-quality tungsten carbide, have become a game-changer in the manufacturing industry, as they offer unique properties that traditional materials cannot match.Tungsten carbide blocks are used in various industries, including construction, mining, and manufacturing. They have a wide range of applications that require high wear and abrasion resistance, such as manufacturing cutting tools, dies, and punches. These blocks offer superior performance and longevity compared to other carbide-based materials, making them the leading choice for toolmakers and manufacturers alike.One of the main advantages of tungsten carbide blocks is their ability to withstand high temperatures. The material has a high melting point, making it an ideal choice for applications that require high resistance to heat. Tungsten carbide blocks are also highly resistant to deformation, making them suitable for use in high-pressure environments.Additionally, tungsten carbide blocks exhibit exceptional hardness, providing high wear resistance, and low friction. This unique combination of properties makes the carbide block ideal for applications that require high-precision machining. Many industries, such as the oil and gas and mining sectors, have adopted tungsten carbide blocks due to their outstanding performance in harsh environments.Leading tungsten carbide block manufacturers pride themselves in producing exceptional quality blocks. They focus on using only the best raw materials and state-of-the-art technology to ensure that their blocks meet the most stringent quality standards. This quality-oriented approach has enabled manufacturers to remain the go-to source for manufacturers seeking high-quality tungsten carbide blocks.Tungsten carbide blocks come in different shapes and sizes, catering to various manufacturing applications. Manufacturers can order customized blocks tailored to their specific needs, with varying grades of tungsten carbide to suit the specific application. Additionally, manufacturers can request blocks with different surface finishes to enhance their resistance to wear and corrosion.The growing demand for tungsten carbide blocks has prompted many companies to invest in advanced technology to streamline their production processes. These investments have enabled manufacturers to produce tungsten carbide blocks faster without compromising on quality. Automation has also helped manufacturers to reduce production costs while improving their output.The adoption of tungsten carbide blocks has revolutionized the manufacturing industry, providing manufacturers with cutting-edge technology that improves production performance, longevity, and accuracy. Manufacturers in various industries now have access to a broad range of options to choose from, ensuring that they get the precise block they need for their specific applications.Moreover, by using tungsten carbide blocks, manufacturers can enhance their bottom lines by reducing their production costs and improving the quality of their products. Tungsten carbide blocks are a superior material that is cost-effective in the long run, making them an ideal choice for manufacturers who seek to maximize their profits.The future of tungsten carbide blocks looks bright, with increased investments in R&D that continue to enhance their quality, performance, and durability. Manufacturers can expect to see more advanced products that push the limits of what tungsten carbide blocks can offer.In conclusion, tungsten carbide blocks are a highly durable and versatile material that has revolutionized the manufacturing industry. With their exceptional strength, heat resistance, and wear resistance, these blocks continue to be a game-changer in many industries, providing manufacturers with a cost-effective solution that enhances their performance and bottom line. As the industry continues to invest in advanced technology, manufacturers can expect to benefit from even more innovative tungsten carbide blocks.
Applications of Tungsten Carbide: A Versatile Industrial Material
Title: Tungsten Carbide: Revolutionizing Industries with Unparalleled VersatilityIntroduction:In the world of industrial applications, Tungsten Carbide has emerged as a game-changing material renowned for its exceptional hardness, durability, and versatility. With its remarkable properties and myriad of applications, this composite material has found its way into various industries, transforming manufacturing processes and enhancing product performance. This article delves into the multifaceted use of Tungsten Carbide and its profound impact on different sectors of the global economy.1. Automotive Industry:From precision cutting tools to durable automotive components, Tungsten Carbide is revolutionizing the automotive sector. In cutting-edge engine manufacturing, Tungsten Carbide inserts in tooling systems play a vital role in delivering precise and high-speed machining with superior surface finish. Mechanical seals made from this robust material ensure leak-free operation in automotive water pumps and ensure prolonged service life. Moreover, the use of Tungsten Carbide in brake pads and clutch facings improves braking performance and enhances durability, ensuring driver safety.2. Oil and Gas Industry:The oil and gas industry heavily relies on Tungsten Carbide due to its exceptional wear resistance and high-temperature stability. Exploration and drilling operations utilize hard-facing applications, such as drill bits, to withstand extreme working conditions while maximizing drilling efficiency. Furthermore, Tungsten Carbide components in downhole tools, such as stabilizers and wear-resistant valves, endure the challenging environment and enhance operational reliability. By offering superior resistance to erosion and corrosion, Tungsten Carbide ensures increased productivity and reduced downtime in the oil and gas sector.3. Mining and Construction:In the mining and construction sectors, where equipment operates in harsh environments, Tungsten Carbide plays a crucial role in enhancing equipment longevity and efficiency. The use of Tungsten Carbide in drill bits, augers, and tooling systems allows for improved penetration rates and extended tool life. Excavation buckets and teeth made from this material withstand abrasion from rocks and other challenging geological conditions, reducing maintenance costs and increasing productivity. The mining industry benefits greatly from the advanced performance and reliability offered by Tungsten Carbide, enabling extraction operations to occur seamlessly and efficiently.4. Metalworking and Tooling:Tungsten Carbide is widely acclaimed in the metalworking industry for its exceptional resistance to wear, deformation, and high temperatures. Cutting inserts and end mills made from this composite material offer superior cutting speed, precision, and surface finish, thereby enhancing overall machining productivity. Tungsten Carbide tooling systems also find extensive applications in the woodworking industry, where they deliver increased cutting efficiency and improved finish quality. These properties make Tungsten Carbide an indispensable choice for manufacturing sectors, guaranteeing efficiency and precision in every operation.5. Electronics and Semiconductors:In the rapidly advancing field of electronics and semiconductors, Tungsten Carbide is sought after for its electrical conductivity and resistance to wear and heat. The material is widely used in the production of semiconductor dies, integrated circuit packages, and wire bonding tools, ensuring reliable and durable electronic devices. Tungsten Carbide's remarkable electrical conductivity, coupled with its high strength, makes it an indispensable choice for electronics manufacturers.Conclusion:Tungsten Carbide's unique blend of hardness, durability, and versatility has transformed various industries and manufacturing processes worldwide. From automotive components to oil and gas equipment, mining tools to metalworking applications, and electronics to semiconductors, this exceptional material has proven to be an invaluable asset for enhancing product performance, increasing productivity, and reducing maintenance costs. As technological advancements continue to shape our world, Tungsten Carbide remains at the forefront, playing a pivotal role in shaping a more efficient and sustainable future across multiple sectors.
Maximizing the Benefits of Tungsten Carbide in Cold Heading Applications
Tungsten Carbide Cold Heading: The Perfect Solution for Your Fastening Needs Fastening systems have come a long way in recent years with advancements in technology and material sciences. One such advancement in fastening systems is Tungsten Carbide Cold Heading. Compared to other materials, Tungsten Carbide Cold Heading has the ability to withstand extreme temperatures, wear and tear, and chemical reactions.With the increase in demand for fastening solutions, Tungsten Carbide Cold Heading has become the primary choice of many industries, including automotive, aerospace, and construction.What is Tungsten Carbide Cold Heading?Tungsten Carbide Cold Heading comprises a high percentage of tungsten carbide, typically ranging anywhere between 85%- 95%, mixed with a binding agent such as cobalt or nickel. The process of forming Tungsten Carbide Cold Heading involves compressing the material into shape while it's in its cold state.The compression process results in homogeneous grain structure, providing a unique combination of strength, hardness, and fracture toughness. The production process of Tungsten Carbide Cold Heading ensures that the material can withstand any amount of wear and tear and provide long-lasting, reliable fastening solutions.Applications and Advantages of Tungsten Carbide Cold HeadingTungsten Carbide Cold Heading is a versatile material used for various fastening applications. One of the primary applications of Tungsten Carbide Cold Heading is manufacturing cold-formed parts, including screws, bolts, nuts, and other fasteners.Due to the high energy absorption properties of Tungsten Carbide Cold Heading, they are also used in the construction industry to manufacture heavy machinery and equipment parts. Tungsten Carbide Cold Heading's resistance to wear and tear, resistance to extreme temperatures, and chemical inertness makes it suitable for use in harsh environments such as mining equipment and oil rigs.Another application of Tungsten Carbide Cold Heading is in the aerospace industry, where the material is ideal for manufacturing turbine engine blades and other aircraft parts. The unique characteristics of Tungsten Carbide Cold Heading, including its strength, wear resistance, and durability, make it the preferred material in the aerospace industry.Apart from this, several other advantages of Tungsten Carbide Cold Heading make it an ideal choice for various applications. For instance:1. Resistance to Wear and TearTungsten Carbide Cold Heading's high hardness, low friction, and exceptional wear resistance make it an ideal choice for applications that require lasting durability. The material can withstand high stress and maintain its shape, even under extreme conditions.2. High StrengthThe high strength of Tungsten Carbide Cold Heading makes it ideal for applications that require strong and durable fastening solutions. The material's strength makes it ideal for heavy construction machinery parts, aerospace turbine blades, and automotive engine components.3. Resistance to Extreme TemperaturesTungsten Carbide Cold Heading's ability to withstand extreme temperatures, ranging from -273°C to 500°C, makes it suitable for use in harsh environments. The material's resistance to high temperatures makes it ideal for use in the oil and gas industry, where temperatures can exceed 200°C.4. Chemical InertnessThe chemical inertness of Tungsten Carbide Cold Heading makes it an ideal choice for use in corrosive environments. The material's chemical stability makes it resistant to corrosion, erosion, and oxidation, ensuring long-lasting durability.5. High Fracture ToughnessThe high fracture toughness of Tungsten Carbide Cold Heading makes it suitable for applications that require resistance to cracking and damage. The material's fracture toughness enables it to withstand high impact forces, making it ideal for use in high-stress environments.Introducing the Leading Tungsten Carbide Cold Heading ManufacturerOur company is a leading manufacturer of Tungsten Carbide Cold Heading. We specialize in producing high-quality, reliable, and affordable Tungsten Carbide Cold Heading solutions for various industries. Our production process uses the latest technology and adheres to the highest quality standards to ensure that our products exceed your expectations.We take pride in our ability to provide excellent customer service, timely delivery of products, and expert technical support. Our team of experts works closely with you to ensure that our Tungsten Carbide Cold Heading solutions meet your specific requirements.Final ThoughtsAs the demand for robust, reliable, and durable fastening systems continues to grow, Tungsten Carbide Cold Heading has become the primary choice of many industries. The unique characteristics of Tungsten Carbide Cold Heading, including high strength, resistance to wear and tear, and robustness, make it an ideal material for use in extreme conditions.If you're looking for a reliable supplier of Tungsten Carbide Cold Heading solutions, look no further than our company. We specialize in providing high-quality Tungsten Carbide Cold Heading products that meet your specific requirements. Contact us today to learn more about our Tungsten Carbide Cold Heading solutions.
High Quality Tungsten Carbide Wire Drawing Die for Industrial Use
Tungsten Carbide Wire Drawing Die is a crucial component in the wire drawing process, used to pull a metal wire through a specific shape and size. This die is essential in various industries such as automotive, aerospace, electronics, and construction, where high precision and quality wire products are required. With the increasing demand for high-performance wire drawing dies, {Company Name} continues to be a leading provider of tungsten carbide wire drawing dies, offering superior quality and reliable performance.{Company Name} has been a pioneering force in the development and manufacturing of tungsten carbide wire drawing dies for many years. The company has established a strong reputation for delivering high-quality products that meet and exceed the expectations of its customers. With a dedicated team of engineers, technicians, and experts, {Company Name} is committed to continuous innovation and improvement in the design and production of tungsten carbide wire drawing dies.The tungsten carbide wire drawing dies offered by {Company Name} are known for their exceptional strength, wear resistance, and durability. These qualities make them the ideal choice for demanding wire drawing applications, where the die needs to withstand high stress, pressure, and temperature. The superior hardness and toughness of tungsten carbide ensure that the wire drawing dies maintain their shape and dimensions, resulting in consistent and precise wire products.{Company Name} takes great pride in its state-of-the-art manufacturing facilities, equipped with advanced machinery and technology for producing tungsten carbide wire drawing dies of the highest quality. The company's production processes are carefully controlled and monitored to ensure that each die meets the strictest standards for performance and reliability. Additionally, {Company Name} conducts thorough quality testing and inspection to guarantee that every wire drawing die leaving its facility is flawless and ready for use.One of the key advantages of {Company Name}'s tungsten carbide wire drawing dies is their versatility and compatibility with a wide range of metals and alloys. Whether it's steel, aluminum, copper, or any other metal, these dies are designed to deliver exceptional results across different wire drawing applications. This flexibility makes them a preferred choice for manufacturers and producers in various industries who rely on high-quality wire products for their operations.{Company Name} understands the importance of providing superior customer support and service. The company's dedicated team of experts is always available to assist customers with their specific requirements and technical inquiries. Whether it's custom die designs, material recommendations, or troubleshooting assistance, {Company Name} is committed to ensuring that its customers receive the highest level of support and satisfaction.In conclusion, {Company Name} continues to be at the forefront of the industry as a leading provider of tungsten carbide wire drawing dies. With a focus on innovation, quality, and customer satisfaction, the company has established a strong presence and reputation in the market. By offering superior products and exceptional service, {Company Name} remains the preferred choice for businesses and industries seeking high-performance wire drawing dies for their operations.
High-Performance Tungsten Carbide Rollers for Industrial Applications
In the global world of industrial manufacturing, the need for tough and durable equipment is essential for any business to succeed and stay ahead of the competition. One product that meets these demands of the industry is the industrial tungsten carbide rollers (need remove brand name). Tungsten carbide rollers are used in various manufacturing processes such as wire flattening, metal stamping, chemically aggressive materials handling, and many more.These rollers are made of tungsten carbide, which is a strong, hard, and corrosion-resistant material. Tungsten carbide is combined with cobalt or nickel to produce a composite material that can withstand harsh environmental conditions and, at the same time, offer the much-needed durability for industrial applications.The industrial tungsten carbide rollers have become a vital component in the manufacturing process, providing high-precision, high-speed, and high-quality solutions in various industries. The rollers are designed to withstand rugged use and are resistant to wear, corrosion, and impact. Tungsten carbide rollers have unmatched durability, making them the perfect choice for high-stress applications in the industrial sector.One of the leading manufacturers of industrial tungsten carbide rollers, (need remove brand name), has been providing high-quality products for many years. The company uses advanced technology and a team of experts in the field to ensure that their rollers meet the highest standards and quality required by various industries.(need remove brand name) has a reputation for producing customized solutions depending on the specific needs of their clients. They understand that each industrial process is unique, and clients have diverse expectations that they must meet. They work with their clients to ensure that the rollers provided are customized to meet the specific needs of their clients' applications.One of the primary features that set (need remove brand name)'s industrial tungsten carbide rollers apart from others is the ability to maintain tight tolerances in size, roundness, and concentricity. The company uses state-of-the-art machinery combined with a team of dedicated experts to ensure that every roller produced is consistent in shape and size. This precision means that the rollers can handle high speeds and high loads without compromising the quality of the end product.Another outstanding feature that makes (need remove brand name)'s tungsten carbide rollers top in the market is their resistance to wear. These rollers can last several times longer than standard steel rollers, which makes them a cost-saving option for many industries. The rollers work efficiently through various abrasive and corrosive environments, providing a longer service life.(need remove brand name) is also known for their excellent customer service. They have a team of experts who are always ready to offer advice to their clients on the best product options for their specific applications. The team is also available to provide after-sales service, including installation, maintenance, and repair of their products.In conclusion, the industrial tungsten carbide rollers (need remove brand name) are a game-changer for many industries worldwide. Their unmatched durability, precision, resistance to wear, and corrosion make them the perfect choice for high-performance applications. (need remove brand name) has taken the market as leaders in the production of these rollers by offering customized solutions that meet a wide range of industrial applications. For businesses that value long-lasting equipment to enhance their manufacturing process, (need remove brand name)'s industrial tungsten carbide rollers are a perfect choice.
Discover the Superiority of Tungsten Carbide Wire Drawing Dies in the News
[Company name], a leading manufacturer of tungsten carbide wire drawing dies, is revolutionizing the wire drawing industry with its innovative and high-performance products. With a strong commitment to quality, reliability, and customer satisfaction, the company has become a trusted name in the industry.Tungsten carbide wire drawing dies are crucial components used in the manufacturing process of various wires. These dies are known for their exceptional hardness, wear resistance, and durability, making them ideal for drawing high-quality wires of different diameters. [Company name]'s extensive lineup of tungsten carbide wire drawing dies caters to the diverse needs of various industries, including automotive, electronics, telecommunications, and construction.The company's extensive experience and expertise in the field of manufacturing wire drawing dies have enabled them to develop cutting-edge solutions that meet the rigorous demands of the industry. Their team of engineers and technicians is dedicated to continuous research and development, ensuring that their products are at the forefront of technological advancements.One of the key features of [Company name]'s tungsten carbide wire drawing dies is their superior surface finish, which ensures smooth wire drawing operations. The dies are meticulously engineered to minimize surface defects and reduce wire breakage, resulting in improved production efficiency and cost-effectiveness.Moreover, [Company name] understands that every customer has unique requirements and specifications. Therefore, they offer customized solutions tailored to the specific needs of each client. Whether it is a specific wire shape, size, or coating requirement, the company's experts work closely with the clients to design and manufacture dies that meet their exact specifications.In addition to their commitment to quality, [Company name]'s commitment to environmental sustainability is commendable. They adhere to strict environmental standards throughout their manufacturing processes, ensuring minimal impact on the environment. Their sustainable practices and responsible approach have earned them certifications and recognition from various regulatory bodies.Furthermore, customer satisfaction is at the core of [Company name]'s business ethos. The company strives to provide exceptional service and support to its customers, ensuring that their needs are met promptly and efficiently. Their dedicated customer service team is readily available to address any queries or concerns, ensuring a seamless experience for their clients.To stay ahead in a highly competitive market, [Company name] also invests in cutting-edge technology and machinery. Their state-of-the-art manufacturing facilities are equipped with the latest equipment, enabling them to produce wire drawing dies with unmatched precision and quality.As a testament to their commitment to excellence, [Company name] has earned a stellar reputation in the industry. Their products are known for their outstanding performance, durability, and long service life. Countless satisfied customers testify to the superior quality and reliability of [Company name]'s tungsten carbide wire drawing dies.With their unwavering dedication to innovation, quality, and customer satisfaction, [Company name] continues to be a leader in the tungsten carbide wire drawing dies industry. The company's relentless pursuit of excellence and commitment to meeting the evolving needs of its customers ensure that it will remain at the forefront of the industry for years to come.As demand for high-quality wires continues to grow across various industries, [Company name]'s tungsten carbide wire drawing dies are set to play a crucial role in meeting this demand. With their superior performance, unmatched quality, and exceptional customer support, [Company name] is poised to shape the future of the wire drawing industry.
Benefits of Cemented Carbide Rolls in Industrial Applications
Cemented Carbide Roll: A Game-Changer In The World Of Industrial ManufacturingIndustrial manufacturing is one of the most important sectors of every economy. It is responsible for the production of goods that are essential to human life, such as automobiles, electronics, and even food products. The manufacturing process involves a wide range of machinery, each of which plays a critical role in ensuring that the products meet the required standards.One of the most crucial components of the machinery used in industrial manufacturing is the roll. A roll is a cylinder-shaped part that helps in shaping and forming materials like sheet metal, plastic, and paper. One of the most advanced rolls in the world of industrial manufacturing is the cemented carbide roll.Introduction to Cemented Carbide RollThe cemented carbide roll is a roll that is widely used in industrial manufacturing. It is hailed as one of the best rolls in terms of performance. The cemented carbide roll is made from tungsten carbide or tungsten carbide and cobalt. These materials make the roll hard and durable, which makes them ideal for use in industrial manufacturing.Cemented carbide rolls are used in various industries, including steel, aluminum, and paper production. They are mostly used in hot rolling mills, where they play a critical role in shaping and forming materials like sheet metal, steel wire, and other similar materials.Features of Cemented Carbide RollOne of the standout features of cemented carbide rolls is their hardness. Cemented carbide rolls are made from materials that have a high melting point, making them extremely resistant to wear, corrosion, and other forms of damage. The rolls can operate in varying temperatures without experiencing any damage.Cemented carbide rolls are also known for their durability. These rolls have a long service life compared to other types of rolls. They can continue working for years without requiring replacement or repairs, which significantly reduces maintenance costs.Another important feature of cemented carbide rolls is their high accuracy. These rolls are made to precision, which ensures that the materials they produce meet the required specifications. The accuracy of cemented carbide rolls results in better quality products, which translates to higher profit margins.Benefits of Cemented Carbide RollCemented carbide rolls have numerous benefits, making them an ideal choice for industrial manufacturing. One of the main benefits of cemented carbide rolls is that they require less frequent replacement and repairs compared to other types of rolls. This significantly reduces maintenance costs, which translates to higher profits for manufacturers.Cemented carbide rolls are also known for their high accuracy, which leads to better quality products. This, in turn, leads to high customer satisfaction and repeat business. Manufacturers that use cemented carbide rolls have a competitive advantage over their competitors who use other types of rolls.Another benefit of cemented carbide rolls is their ability to operate in varying temperatures. These rolls can withstand high temperatures without experiencing any damage, making them ideal for use in hot rolling mills. This ability to operate at high temperatures improves the efficiency of the manufacturing process, which translates to higher productivity and profits.ConclusionIn conclusion, cemented carbide rolls are a game-changer in the world of industrial manufacturing. These rolls are ideal for use in hot rolling mills, where they play a critical role in shaping and forming materials like sheet metal, steel wire, and other similar materials. They are known for their hardness, durability, high accuracy, and ability to operate in varying temperatures. These features and benefits make cemented carbide rolls an ideal choice for manufacturers looking to improve their efficiency, reduce maintenance costs, and produce high-quality products.