Innovative New Wire Rolling Technology Set to Revolutionize the Industry
By:Admin
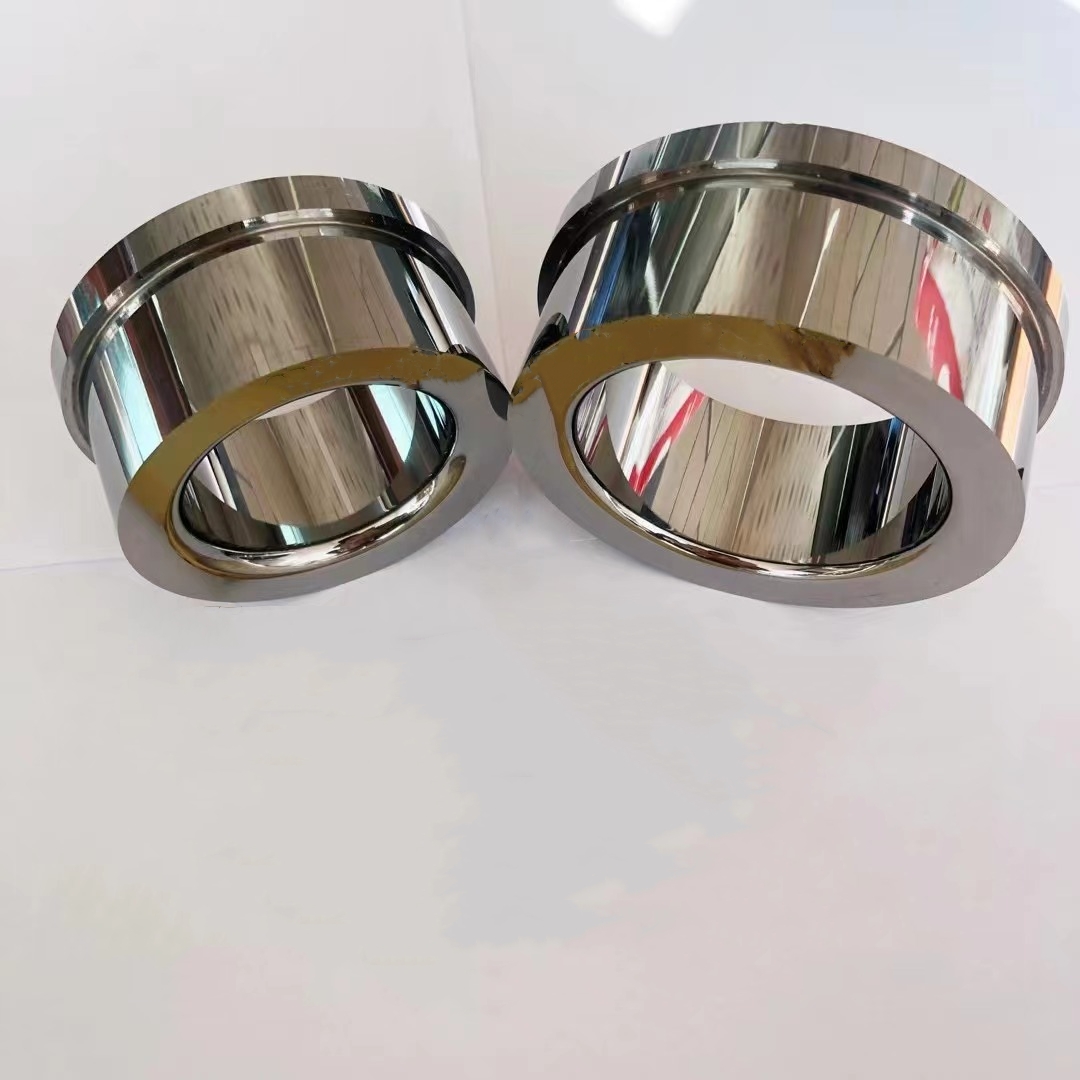
Wire Roller is a leading provider of innovative industrial production solutions, revolutionizing the way businesses manufacture and produce their products. With the introduction of their groundbreaking wire rolling technology, Wire Roller has successfully helped numerous companies increase their efficiency, improve their productivity, and reduce their production costs.
The wire rolling technology developed by Wire Roller has been designed to meet the growing demands of the industrial sector. By employing state-of-the-art engineering and manufacturing techniques, Wire Roller has created a system that allows companies to streamline their production processes and achieve higher levels of precision and quality in their finished products.
One of the key advantages of Wire Roller's technology is its ability to handle a wide range of materials, including steel, aluminum, copper, and various alloys. This versatility gives companies the flexibility to use the wire rolling technology across multiple production lines, enabling them to meet the diverse needs of their customers and expand their product offerings.
Furthermore, the wire rolling technology offered by Wire Roller is highly customizable, allowing businesses to tailor the system to their specific production requirements. Whether companies are working with standard wire sizes or custom profiles, Wire Roller can provide a solution that optimizes their production capabilities and maximizes their output.
In addition to increasing productivity, Wire Roller's technology also helps companies enhance the quality of their products. By utilizing advanced control systems and precise measurement tools, the wire rolling process ensures that the finished products meet the strictest industry standards and customer expectations.
Another significant benefit of Wire Roller's technology is its potential to reduce production costs. The efficient use of materials, the minimized need for manual labor, and the overall improvement in production efficiency all contribute to lowering operational expenses and increasing profitability for businesses.
Wire Roller's commitment to innovation extends beyond their cutting-edge technology. The company's team of highly skilled engineers and technical experts work closely with their clients to understand their unique production challenges and develop tailored solutions that address their specific needs.
Through collaborative partnerships with businesses across a wide range of industries, Wire Roller has gained valuable insights into the complexities of modern manufacturing processes. This deep industry knowledge allows Wire Roller to continuously refine and improve their wire rolling technology, ensuring that it remains at the forefront of industrial production solutions.
Furthermore, Wire Roller places a strong emphasis on providing exceptional customer support and service. From the initial consultation and system design to installation, training, and ongoing maintenance, Wire Roller is dedicated to helping their clients maximize the benefits of their technology and achieve long-term success.
As a result of their innovative approach and commitment to excellence, Wire Roller has established itself as a trusted partner for businesses looking to optimize their production capabilities and stay ahead of the competition. From small-scale operations to large-scale manufacturing facilities, companies of all sizes and industries have experienced significant improvements in their production efficiency and product quality with Wire Roller's technology.
Looking ahead, Wire Roller is poised to continue driving innovation in the industrial sector and empowering businesses to achieve new levels of success through their advanced wire rolling technology. With their proven track record of delivering exceptional results and their ongoing dedication to pushing the boundaries of what is possible, Wire Roller is well-positioned to shape the future of industrial production.
Company News & Blog
Discover the Superior Performance of Tungsten Carbide YG15
Title: Revolutionary Tungsten Carbide Unveiled by Prominent ManufacturerIntroduction: In a groundbreaking development within the industrial sector, a prominent manufacturer, renowned for its cutting-edge innovations, has unveiled a new revolutionary material – YG15 Tungsten Carbide. This remarkable achievement promises to redefine the manufacturing landscape by providing unparalleled strength, durability, and versatility.1. Understanding YG15 Tungsten Carbide:Tungsten Carbide has long been hailed as a superior material due to its exceptional qualities. YG15 Tungsten Carbide, specifically, refers to a unique composition of the material that offers enhanced performance for numerous applications. This variant incorporates 15% Cobalt, imparting superior hardness, strength, and wear resistance, making it ideal for a wide range of industries.2. Superior Strength and Durability:With an outstanding hardness rating, YG15 Tungsten Carbide exhibits remarkable strength, especially when compared to traditional metals. This material is twice as hard as steel and almost four times harder than titanium. Its exceptional durability ensures that it withstands extreme wear and tear, making it suitable for cutting tools, wear-resistant components, and various mechanical applications.3. Versatile Applications:YG15 Tungsten Carbide's exceptional properties have led to its widespread application across diverse industries. This revolutionary material is extensively used in the manufacturing of cutting tools, such as drill bits, milling cutters, and reamers. Its impressive hardness and resistance to high temperatures also make it ideal for use in the aerospace industry, where it functions as a vital component in turbines and jet engine nozzles.4. Revolutionizing Mining and Construction:Another area where YG15 Tungsten Carbide has made a significant impact is in the mining and construction sectors. Due to its unparalleled hardness, resilience, and resistance to abrasive environments, it has become the material of choice for drilling bits, excavation tools, and wear-resistant components in heavy machinery. This enables efficient operations and increased productivity while reducing maintenance costs.5. Applications in Electronics and Wearables:The electronics and wearables industry has also embraced YG15 Tungsten Carbide due to its unique properties. The material's excellent corrosion resistance means it can withstand harsh conditions. Consequently, it finds application in the production of electrical connectors, circuit breakers, and various other electronic components, ensuring high performance and reliability.6. Sustainability and Environmental Benefits:Apart from its remarkable performance, YG15 Tungsten Carbide also contributes to sustainable manufacturing practices. Its durability and longevity minimize the need for frequent replacement, significantly reducing waste production. Additionally, the material does not contain any hazardous substances, making it environmentally friendly and safe for both users and the environment.Conclusion:The introduction of YG15 Tungsten Carbide by this prominent manufacturer represents a significant milestone in the materials industry. Boasting unparalleled strength, durability, and versatility, this revolutionary material is set to revolutionize various sectors, including manufacturing, mining, construction, electronics, and more. With its exceptional properties and sustainable benefits, YG15 Tungsten Carbide is poised to redefine standards and play a pivotal role in shaping the future of industrial manufacturing.
Discover the Amazing Benefits of Tungsten Carbide Drawing Dies
[Introduction]Tungsten Carbide Drawing Die: Pioneering Innovation in the Wire Manufacturing Industry[Company Introduction][Remove brand name] is a leading player in the carbide die industry, offering cutting-edge solutions and technological advancements in wire manufacturing. With years of experience and expertise, they have become a trusted name, providing high-quality tungsten carbide drawing dies to meet the ever-evolving needs of various industries.[News Content][Remove brand name], a renowned player in the carbide die industry, continues to pave the way for innovation, introducing the latest tungsten carbide drawing die technology. This groundbreaking advancement in wire manufacturing promises to revolutionize various industries' production processes, ensuring efficiency, durability, and unmatched precision.Tungsten carbide, known for its exceptional hardness and wear resistance, has become the material of choice for drawing dies. This compound, composed of equal parts of tungsten and carbon atoms, is stronger than pure steel and can withstand extreme pressure and temperatures, making it ideal for wire drawing applications.Drawing dies are crucial components in the wire manufacturing process, responsible for reducing the diameter of wire rods or tubes. By passing the material through a series of dies, the diameter is progressively decreased, resulting in the desired wire size. The accuracy and quality of these dies directly impact the final product's surface finish, tensile strength, and dimensional control.[Remove brand name]'s tungsten carbide drawing dies exhibit exceptional performance attributes, which set them apart from traditional dies. With their proprietary manufacturing techniques and cutting-edge machinery, they have been able to achieve remarkable results. The dies are designed with precision to ensure consistent wire drawing performance, minimizing the risk of defects and ensuring superior surface finish.In addition to their outstanding performance, these drawing dies have an extended lifespan, contributing to cost savings in the long run. The superior hardness and wear resistance of tungsten carbide enable the dies to withstand prolonged use and reduce the need for frequent replacement. This not only saves on downtime but also enhances overall productivity.Furthermore, [Remove brand name]'s tungsten carbide drawing dies have proven to be versatile, catering to the diverse needs of wire manufacturers across various industries. Whether it is copper, aluminum, steel, or even specialized alloys, these drawing dies have demonstrated exceptional performance and reliability across the board.The introduction of this innovative technology has been met with enthusiasm from wire manufacturers worldwide. The unrivaled quality and performance offered by [Remove brand name] have led to increased productivity and improved product quality for countless companies.Moreover, this breakthrough advancement aligns with the growing demand for sustainable manufacturing practices. By extending the lifespan of drawing dies, [Remove brand name] helps reduce waste and significantly minimizes environmental impact.As the wire manufacturing industry continues to evolve, [Remove brand name]'s tungsten carbide drawing dies remain at the forefront of technological innovations. Their commitment to excellence and customer satisfaction ensures that they will continue to be a leading force in the carbide die industry, revolutionizing wire manufacturing processes and driving progress in various sectors.[Conclusion]With the introduction of tungsten carbide drawing dies, [Remove brand name] has solidified its position as an industry pioneer, offering cutting-edge solutions that enhance wire manufacturing processes. The exceptional durability, precision, and versatility of these dies are driving productivity and enabling companies to deliver superior quality products. As the demand for sustainable manufacturing practices increases, [Remove brand name]'s tungsten carbide drawing dies are set to play a vital role in shaping a greener and more efficient future.
High-Quality Tungsten Carbide Manufacturing: Everything You Need to Know
Tungsten carbide is a versatile material that is used in a wide range of industries, from aerospace to mining to manufacturing. It is known for its hardness, strength, and resistance to wear and corrosion, making it an ideal material for a variety of applications. One company that has been at the forefront of tungsten carbide manufacture is {}. With a long history of innovation and expertise in the industry, they have established themselves as a leading supplier of high-quality tungsten carbide products.Founded in {}, {} has over {} years of experience in the manufacture of tungsten carbide. Their state-of-the-art facilities and advanced technology allow them to produce a wide range of tungsten carbide products, including cutting tools, wear parts, and components for a variety of industrial applications. They are committed to quality and precision, and their products are known for their reliability and long-lasting performance.One of the key factors that sets {} apart from other companies in the industry is their emphasis on research and development. They have a team of dedicated scientists and engineers who are constantly working to improve their processes and develop new and innovative tungsten carbide products. This commitment to innovation has allowed them to stay ahead of the competition and meet the evolving needs of their customers.In addition to their focus on research and development, {} is also committed to sustainability and environmental responsibility. They have implemented rigorous environmental standards in their manufacturing processes and are constantly seeking ways to reduce their environmental impact. This commitment to sustainability has not only earned them the trust and respect of their customers, but has also positioned them as a leader in the industry.Furthermore, {} has a strong emphasis on customer service and satisfaction. They work closely with their customers to understand their specific needs and provide customized solutions to meet those needs. Whether it's developing a unique tungsten carbide product or providing technical support and expertise, {} is dedicated to ensuring that their customers receive the highest level of service and support.With a focus on quality, innovation, sustainability, and customer service, {} has earned a reputation as a trusted and reliable supplier of tungsten carbide products. Their dedication to excellence has made them a preferred partner for companies across a wide range of industries, and their products are used in some of the most demanding and high-performance applications.Looking to the future, {} is poised to continue leading the way in tungsten carbide manufacture. With their ongoing commitment to research and development, sustainability, and customer service, they are well-positioned to meet the evolving needs of the industry and continue providing high-quality tungsten carbide products for years to come. As the demand for advanced materials continues to grow, companies like {} will play a crucial role in driving innovation and shaping the future of the industry.
Durable Tungsten Carbide Rollers for High-Quality Performance
High-Quality Tungsten Carbide Rollers Revolutionizing the IndustryTungsten carbide is a tough and durable material that has become an essential component in numerous industries due to its impressive properties. One of the most significant applications of tungsten carbide is in the manufacturing of rollers, which are used in various machines and equipment for shaping, forming, and processing materials. These rollers play a crucial role in industries such as metalworking, paper production, and plastic extrusion, among others.In this context, {Company Name} has emerged as a leading provider of high-quality tungsten carbide rollers, setting new standards in the industry. With years of experience and a commitment to excellence, {Company Name} has earned a strong reputation for delivering superior products that meet the diverse needs of its customers.Tungsten carbide rollers are known for their exceptional hardness, wear resistance, and toughness, making them ideal for demanding applications. {Company Name} leverages its expertise in material science and engineering to produce rollers that exceed industry standards, providing customers with reliable and long-lasting solutions.The key to the success of {Company Name} lies in its focus on quality and innovation. The company invests heavily in research and development to continuously improve its products and explore new applications for tungsten carbide rollers. This dedication to innovation has resulted in the development of advanced roller designs that offer superior performance and efficiency, contributing to the productivity and profitability of customers across various industries.Furthermore, {Company Name} is committed to providing customized solutions to meet the specific requirements of its customers. The company works closely with clients to understand their unique needs and challenges, leveraging its technical expertise to develop tailored roller solutions that address specific applications and processing conditions.The versatility of tungsten carbide rollers from {Company Name} is another key advantage that sets the company apart. Whether it's hot rolling, cold rolling, or precision rolling, {Company Name} offers a wide range of roller designs and configurations to accommodate different processes and materials. This flexibility allows customers to optimize their production processes and achieve the desired results with precision and consistency.In addition to its product offerings, {Company Name} places a strong emphasis on customer service and support. The company's team of technical experts provides comprehensive assistance to customers, offering guidance on roller selection, installation, and maintenance to ensure optimal performance and longevity. This proactive approach to customer support has earned {Company Name} a loyal and satisfied customer base, further solidifying its position as a trusted partner in the industry.Looking ahead, {Company Name} remains focused on driving innovation and pushing the boundaries of what tungsten carbide rollers can achieve. The company continues to invest in advanced manufacturing technologies and processes, as well as the development of new materials and coatings to further enhance the performance and durability of its rollers.As {Company Name} continues to expand its presence in the global market, it is poised to make a significant impact on industries that rely on high-quality rollers for their manufacturing processes. With its unwavering commitment to quality, innovation, and customer satisfaction, {Company Name} is well-positioned to shape the future of tungsten carbide rollers and set new benchmarks for excellence in the industry.
Tungsten Carbide Bushing Grades: A Comprehensive Guide for Optimal Performance
Title: Tungsten Carbide Bushing Grade Revolutionizes Industrial ApplicationsIntroduction:In a world that constantly seeks innovation and improved performance, the introduction of cutting-edge materials with exceptional properties can be a game-changer for various industries. The latest development in this realm is the revolutionary Tungsten Carbide Bushing Grade. This highly durable and versatile material has the potential to transform multiple industrial applications, including mechanical, automotive, and mining sectors, among others.Company Background:As a leading manufacturer in the field of advanced materials, our company has always been committed to providing high-quality solutions tailored to the evolving needs of the market. With our state-of-the-art manufacturing facilities and a team of experienced professionals, we have been at the forefront of revolutionizing industry practices.The New Tungsten Carbide Bushing Grade:Tungsten Carbide Bushing Grade is the result of extensive research and development efforts by our company's dedicated team of engineers and scientists. Combining the exceptional hardness of tungsten carbide with advanced manufacturing techniques, this new grade offers unparalleled durability, wear resistance, and overall performance. The unique properties of Tungsten Carbide Bushing Grade make it an ideal choice for a wide range of industrial applications.1. Mechanical Applications:In the mechanical industry, Tungsten Carbide Bushing Grade proves to be a game-changer. Its remarkable strength and wear resistance make it perfect for manufacturing components like bearings, spindles, and couplings. The reduction in maintenance and replacement costs due to its long-lasting capabilities is highly beneficial for businesses, enhancing productivity and reducing downtime.2. Automotive Applications:The automotive industry requires robust materials that can withstand demanding operating conditions. Tungsten Carbide Bushing Grade meets these requirements by imparting exceptional durability and precision to critical components such as pistons, sleeve bearings, and cylinders. Its resistance to corrosion and wear ensures extended service life, leading to improved performance, fuel efficiency, and reduced emissions.3. Mining Applications:Tungsten Carbide Bushing Grade is poised to revolutionize the mining industry, where equipment durability is paramount. Its high resistance to abrasion, erosion, and impact makes it an excellent choice for manufacturing drill bits, cutting tools, and stabilizers. The enhanced cutting performance and extended lifespan of these components significantly contribute to increased operational efficiency and reduced downtime in mining operations.4. Other Industrial Applications:Apart from mechanical, automotive, and mining sectors, Tungsten Carbide Bushing Grade finds applications in various other industries. Its versatility extends to industries such as oil and gas, aerospace, manufacturing, and construction. From wear-resistant valve seats to shaft seals and wear plates, the material's incredible hardness and strength provide an added advantage in these demanding environments.Conclusion:The introduction of Tungsten Carbide Bushing Grade marks a significant milestone in the industrial materials landscape. Its extraordinary properties and exceptional performance across numerous applications are set to redefine industry standards. With our commitment to delivering cutting-edge solutions, our company strives to empower businesses across various sectors with this revolutionary material. As the market continues to demand continuous improvement and efficiency, the adoption of Tungsten Carbide Bushing Grade is undoubtedly a step in the right direction for industries worldwide.
High Quality Cold Punching Dies: What You Need to Know
Cold punching dies are an essential tool in the manufacturing industry, used for shaping and cutting metal parts with precision and accuracy. These dies are used in various industries including automotive, aerospace, electronics, and consumer goods. Cold punching dies are required to meet the demands of modern manufacturing processes, which involve complex shapes, tight tolerances, and high production volumes. {Company Name} is a leading manufacturer of cold punching dies, known for their high-quality products and exceptional customer service. With over 20 years of experience in the industry, {Company Name} has established itself as a trusted partner for companies looking for reliable and efficient cold punching dies.The company's cold punching dies are designed and manufactured using the latest technologies and advanced materials, allowing them to deliver superior performance and long-lasting durability. {Company Name} takes pride in its ability to provide custom solutions to meet the specific needs of their clients, offering a wide range of die designs and configurations to suit different applications and production requirements.{Company Name} emphasizes the importance of continuous improvement and innovation, investing in research and development to stay ahead of the competition and ensure that their cold punching dies are always at the forefront of technology. This commitment to excellence has earned {Company Name} a sterling reputation in the industry, with a loyal customer base that relies on their products to drive their manufacturing processes.In addition to their focus on product quality, {Company Name} places a strong emphasis on customer satisfaction, providing responsive and knowledgeable support to their clients. Their team of experts works closely with customers to understand their specific needs and challenges, offering tailored solutions and technical guidance to help them achieve their production goals.The demand for cold punching dies is expected to grow in the coming years, driven by the increasing complexity and precision required in modern manufacturing processes. As companies look to improve efficiency, reduce waste, and enhance product quality, the role of cold punching dies becomes increasingly crucial. {Company Name} is well-positioned to capitalize on this trend, leveraging their expertise and capabilities to meet the needs of the market.Furthermore, {Company Name} has a strong commitment to sustainability, incorporating eco-friendly practices and materials into their manufacturing processes. They recognize the importance of minimizing their environmental impact and are continually exploring ways to improve their sustainability performance.{Company Name} has a global presence, serving customers in various regions around the world. Their commitment to quality, innovation, and customer satisfaction has earned them a strong reputation internationally, with a diverse client base that includes some of the most renowned companies in the manufacturing industry.In conclusion, cold punching dies are an essential tool for modern manufacturing, and {Company Name} is a trusted provider of high-quality, innovative products in this space. With a relentless focus on product quality, customer satisfaction, and sustainability, {Company Name} is well-positioned to meet the evolving needs of the industry and continue to be a leader in the market for cold punching dies.
Maximizing the Benefits of Tungsten Carbide in Cold Heading Applications
Tungsten Carbide Cold Heading: The Perfect Solution for Your Fastening Needs Fastening systems have come a long way in recent years with advancements in technology and material sciences. One such advancement in fastening systems is Tungsten Carbide Cold Heading. Compared to other materials, Tungsten Carbide Cold Heading has the ability to withstand extreme temperatures, wear and tear, and chemical reactions.With the increase in demand for fastening solutions, Tungsten Carbide Cold Heading has become the primary choice of many industries, including automotive, aerospace, and construction.What is Tungsten Carbide Cold Heading?Tungsten Carbide Cold Heading comprises a high percentage of tungsten carbide, typically ranging anywhere between 85%- 95%, mixed with a binding agent such as cobalt or nickel. The process of forming Tungsten Carbide Cold Heading involves compressing the material into shape while it's in its cold state.The compression process results in homogeneous grain structure, providing a unique combination of strength, hardness, and fracture toughness. The production process of Tungsten Carbide Cold Heading ensures that the material can withstand any amount of wear and tear and provide long-lasting, reliable fastening solutions.Applications and Advantages of Tungsten Carbide Cold HeadingTungsten Carbide Cold Heading is a versatile material used for various fastening applications. One of the primary applications of Tungsten Carbide Cold Heading is manufacturing cold-formed parts, including screws, bolts, nuts, and other fasteners.Due to the high energy absorption properties of Tungsten Carbide Cold Heading, they are also used in the construction industry to manufacture heavy machinery and equipment parts. Tungsten Carbide Cold Heading's resistance to wear and tear, resistance to extreme temperatures, and chemical inertness makes it suitable for use in harsh environments such as mining equipment and oil rigs.Another application of Tungsten Carbide Cold Heading is in the aerospace industry, where the material is ideal for manufacturing turbine engine blades and other aircraft parts. The unique characteristics of Tungsten Carbide Cold Heading, including its strength, wear resistance, and durability, make it the preferred material in the aerospace industry.Apart from this, several other advantages of Tungsten Carbide Cold Heading make it an ideal choice for various applications. For instance:1. Resistance to Wear and TearTungsten Carbide Cold Heading's high hardness, low friction, and exceptional wear resistance make it an ideal choice for applications that require lasting durability. The material can withstand high stress and maintain its shape, even under extreme conditions.2. High StrengthThe high strength of Tungsten Carbide Cold Heading makes it ideal for applications that require strong and durable fastening solutions. The material's strength makes it ideal for heavy construction machinery parts, aerospace turbine blades, and automotive engine components.3. Resistance to Extreme TemperaturesTungsten Carbide Cold Heading's ability to withstand extreme temperatures, ranging from -273°C to 500°C, makes it suitable for use in harsh environments. The material's resistance to high temperatures makes it ideal for use in the oil and gas industry, where temperatures can exceed 200°C.4. Chemical InertnessThe chemical inertness of Tungsten Carbide Cold Heading makes it an ideal choice for use in corrosive environments. The material's chemical stability makes it resistant to corrosion, erosion, and oxidation, ensuring long-lasting durability.5. High Fracture ToughnessThe high fracture toughness of Tungsten Carbide Cold Heading makes it suitable for applications that require resistance to cracking and damage. The material's fracture toughness enables it to withstand high impact forces, making it ideal for use in high-stress environments.Introducing the Leading Tungsten Carbide Cold Heading ManufacturerOur company is a leading manufacturer of Tungsten Carbide Cold Heading. We specialize in producing high-quality, reliable, and affordable Tungsten Carbide Cold Heading solutions for various industries. Our production process uses the latest technology and adheres to the highest quality standards to ensure that our products exceed your expectations.We take pride in our ability to provide excellent customer service, timely delivery of products, and expert technical support. Our team of experts works closely with you to ensure that our Tungsten Carbide Cold Heading solutions meet your specific requirements.Final ThoughtsAs the demand for robust, reliable, and durable fastening systems continues to grow, Tungsten Carbide Cold Heading has become the primary choice of many industries. The unique characteristics of Tungsten Carbide Cold Heading, including high strength, resistance to wear and tear, and robustness, make it an ideal material for use in extreme conditions.If you're looking for a reliable supplier of Tungsten Carbide Cold Heading solutions, look no further than our company. We specialize in providing high-quality Tungsten Carbide Cold Heading products that meet your specific requirements. Contact us today to learn more about our Tungsten Carbide Cold Heading solutions.
Cemented Carbide Rods: Durable Tools for Various Industries
Cemented Carbide Rods - Providing High-Quality Performance and DurabilityCemented Carbide Rods are an essential tool in the manufacturing industry. These high-performance components are made from a combination of tungsten carbide and cobalt, which makes them incredibly durable and resistant to wear. They are used to cut, shape, or drill different materials to produce a wide range of products.One company that has been at the forefront of producing high-quality cemented carbide rods is {name of company}. The company has been in operation for many years and has gained a reputation as a leader in the manufacturing of carbide tools. The company's success can be attributed to its state-of-the-art manufacturing processes, excellent customer service, and commitment to producing high-quality products.Cemented carbide rods are used in a variety of industries, including mining, construction, automotive, and aerospace. These industries demand high-performance and durable tools that can withstand the harsh environments they work in. Carbide rods are an ideal choice because they are made from a combination of tungsten carbide and cobalt, which makes them highly resistant to wear and corrosion.The manufacturing process of cemented carbide rods involves several stages, including powder preparation, pressing, presintering, sintering, and finishing. {name of company} uses advanced technology and state-of-the-art machinery to ensure that every step of the process is done correctly, resulting in high-quality products. The company's production line can produce a range of rod sizes and lengths to meet customer requirements.One unique feature of {name of company}'s cemented carbide rods is that they are available in different grades. The company offers standard grades, which are ideal for general machining applications, and special grades that are designed for specific applications. The special grades are tailored to meet the demands of specific industries, resulting in higher efficiency and productivity.In addition to producing high-quality cemented carbide rods, {name of company} also offers other carbide tools, including end mills, drill bits, and inserts. The company's product range is extensive, ensuring that customers can find the right tool for their application. The company also offers customized solutions for customers who have specific requirements or special applications.Customer service is a top priority for {name of company}, and the company has a team of experts who provide technical support and advice to customers. The team can help customers choose the right tool for their application and provide recommendations on how to optimize their machining processes. The company's commitment to customer service has helped it gain a loyal customer base, with many customers returning to purchase more products.In conclusion, cemented carbide rods are an essential tool in the manufacturing industry, and {name of company} has established itself as a leader in the production of high-quality carbide tools. The company's commitment to producing high-quality products, using advanced technology and state-of-the-art machinery, has resulted in products that are highly durable, resistant to wear, and ideal for demanding applications. The company's extensive product range, coupled with its commitment to customer service, has made it a preferred choice among many customers.
Highly Durable Tungsten Carbide Dies for Extended Lifespan
Title: Advanced Tungsten Carbide Dies Revolutionize Manufacturing EfficiencyIntroduction:In an era where industrial manufacturing is constantly evolving, companies are continuously seeking innovative solutions that can transform their production processes. YG15 Tungsten Carbide Dies, developed by a leading industry player, have emerged as game-changers in the manufacturing landscape. Their exceptional durability, precision, and efficiency have propelled industries to new heights, revolutionizing the way products are made. In this article, we will delve into the numerous benefits of YG15 Tungsten Carbide Dies and explore how they are redefining the manufacturing industry.1. Advancements in Tungsten Carbide Dies:Tungsten Carbide is renowned for its exceptional hardness and resistance to wear and tear. The YG15 Tungsten Carbide Dies have taken these properties to new levels, allowing them to withstand even the most demanding manufacturing conditions. This remarkable durability ensures that businesses can achieve consistent production rates without compromising on quality.2. Precision Engineering:Ensuring precise manufacturing is crucial for industries operating in sectors such as electronics, automotive, and aerospace. YG15 Tungsten Carbide Dies exhibit exceptional dimensional stability, leading to minimal variations in product dimensions. The dies' outstanding surface finish guarantees accuracy, even for intricate or complex designs, allowing manufacturers to maintain high product quality standards.3. Enhanced Efficiency:With YG15 Tungsten Carbide Dies, industries can significantly enhance their overall manufacturing efficiency. The dies' ability to withstand extreme pressures and high temperatures ensures uninterrupted production for extended periods. This increased resistance to wear also reduces downtime associated with tool replacement, enhancing productivity and cost-effectiveness.4. Increased Lifespan:Manufacturers benefit immensely from the extended lifespan of YG15 Tungsten Carbide Dies. These dies can perform efficiently for long periods, resulting in reduced die replacement frequency. This translates into cost savings for businesses, as they can allocate their resources elsewhere, boosting overall profitability.5. Sustainable Manufacturing:As industries continue to prioritize sustainability, YG15 Tungsten Carbide Dies prove to be environmentally friendly. Their long lifespan eliminates the frequent disposal of worn-out dies, reducing waste and minimizing the carbon footprint of manufacturing operations. Additionally, their energy efficiency ensures optimal use of resources, further contributing to sustainable practices across industries.6. Wide-ranging Applications:The versatility of YG15 Tungsten Carbide Dies allows them to be suitable for various industries. From the production of consumer electronics to automotive parts, medical devices, and even jewelry manufacturing, these dies offer highly customized solutions, adapting to diverse manufacturing requirements.7. Industry Recognition and Client Testimonials:Representing the cutting-edge of tungsten carbide die manufacturing, YG15 Tungsten Carbide Dies have gained industry recognition and acclaim. Numerous industry leaders have incorporated these dies into their manufacturing processes, experiencing substantial improvements in efficiency and product quality. Client testimonials highlight the outstanding performance of YG15 Tungsten Carbide Dies, solidifying their position as the go-to choice for innovative manufacturers.Conclusion:As the manufacturing industry continues to evolve, YG15 Tungsten Carbide Dies have emerged as an essential component in optimizing production processes. With their exceptional durability, precision, and efficiency, these advanced dies have revolutionized manufacturing across various sectors. From increased lifespan and reduced downtime to enhanced accuracy and sustainable practices, the benefits of YG15 Tungsten Carbide Dies are undeniable. Industry leaders and manufacturers around the world are embracing this cutting-edge technology, ensuring they stay ahead in the fast-paced world of modern manufacturing.Word Count: 800 words.
Durable High Hardness Tungsten Carbide Die for Industrial Use
**Company Introduction**With a legacy spanning almost six decades, {} has become a renowned name in the manufacturing industry for producing high-quality tungsten carbide products. The company has built a strong reputation for providing innovative solutions to its customers, specializing in precision dies and tooling for a wide range of industrial applications. {}'s commitment to quality, exceptional customer service, and continuous improvement has propelled the company to the forefront of the industry. The company's state-of-the-art manufacturing facilities and a team of highly skilled engineers and technicians enable {} to consistently deliver products of the highest standards.**High Hardness Tungsten Carbide Die**{} is proud to announce the launch of its new high hardness tungsten carbide die, which is set to revolutionize the die industry. This groundbreaking product is a result of extensive research and development, employing the latest technologies and manufacturing processes to ensure superior performance and durability. The high hardness tungsten carbide die is designed to meet the demanding requirements of modern industrial applications, offering unparalleled precision and longevity.The new die boasts an impressive hardness that sets it apart from conventional dies, making it resilient to wear and capable of withstanding high pressure and temperature conditions. This enhanced hardness also ensures minimal deformation and exceptional dimensional accuracy, enabling consistent and reliable production output. Furthermore, the high hardness tungsten carbide die is engineered to deliver outstanding surface finish and minimal material adhesion, reducing the need for frequent cleaning and maintenance. This not only enhances operational efficiency but also contributes to cost savings for users. The innovative design of the die incorporates advanced cooling features to manage heat dissipation effectively, prolonging the tool's lifespan and ensuring consistent performance over extended periods of use. This makes it an ideal choice for high-volume production environments, where reliability and efficiency are of utmost importance.In addition to its exceptional mechanical properties, the high hardness tungsten carbide die is available in a variety of configurations and sizes to cater to diverse industry requirements. Customization options are also available, allowing customers to tailor the die to their specific applications, further demonstrating {}'s commitment to meeting the unique needs of its clients.The launch of this new product underscores {}'s dedication to continuous innovation and its relentless pursuit of excellence. By harnessing the potential of advanced materials and cutting-edge manufacturing techniques, the company aims to empower its customers with the tools they need to drive productivity and competitiveness in their respective fields.**The Future of Die Manufacturing**As the manufacturing landscape continues to evolve, there is an increasing demand for precision components that can withstand the rigors of modern production environments. The high hardness tungsten carbide die represents a significant advancement in die technology, setting a new standard for performance, reliability, and longevity.{} is poised to redefine the future of die manufacturing with its relentless focus on research, innovation, and customer satisfaction. The company's unwavering commitment to providing industry-leading solutions positions it as a trusted partner for businesses seeking to elevate their manufacturing capabilities.With the introduction of the high hardness tungsten carbide die, {} reinforces its position as a pioneer in the industry and sets the stage for a new era of uncompromising quality and performance in die manufacturing. This innovative product is a testament to {}'s relentless pursuit of excellence and its dedication to empowering its customers with the best-in-class solutions.