High-Quality Tungsten Carbide Molding Dies for Precision Manufacturing
By:Admin
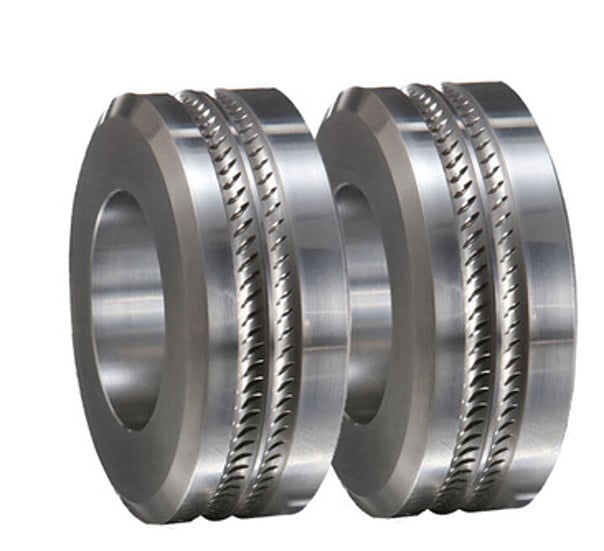
{Company} has been a key player in the manufacturing industry for over 30 years, specializing in the production of tungsten carbide products. Their expertise in this area has allowed them to develop cutting-edge molding dies that have set new standards for quality and performance.
Tungsten carbide is a composite material composed of tungsten carbide particles held together by a metal binder, typically cobalt. This unique combination of materials gives tungsten carbide molding dies their exceptional hardness and wear resistance, making them ideal for use in high-stress manufacturing environments.
One of the primary uses of tungsten carbide molding dies is in the production of metal and plastic components through the process of cold-heading and cold-forming. These dies are essential for shaping and forming materials such as steel, aluminum, and copper with precision and efficiency. The superior hardness and wear resistance of tungsten carbide ensure that these dies maintain their cutting edge and dimensional accuracy over prolonged use, resulting in higher productivity and reduced downtime for manufacturers.
In addition to cold-heading and cold-forming applications, tungsten carbide molding dies are also widely used in the production of ceramics, glass, and other non-metallic materials. The exceptional hardness and thermal conductivity of tungsten carbide make it an ideal material for shaping and forming these materials with a high degree of precision.
{Company} has been at the forefront of developing custom tungsten carbide molding dies to meet the specific needs of their clients. Their team of experienced engineers and technicians work closely with customers to design and produce dies that are tailored to their unique specifications and requirements. This level of customization has enabled {company} to establish itself as a trusted partner for manufacturers in a wide range of industries, including automotive, aerospace, medical, and consumer goods.
The commitment to quality and innovation at {company} is evident in their state-of-the-art manufacturing facilities, where the latest technology and advanced equipment are employed to produce tungsten carbide molding dies of the highest caliber. Stringent quality control measures are implemented at every stage of the production process to ensure that the dies meet the strictest standards for performance and durability.
Furthermore, {company} places a strong emphasis on research and development to stay ahead of the curve in the rapidly evolving manufacturing industry. Their investment in cutting-edge technologies and continuous improvement initiatives has led to the development of new and innovative solutions that push the boundaries of what is possible with tungsten carbide molding dies.
The impact of tungsten carbide molding dies on the manufacturing industry cannot be overstated. Their exceptional durability, precision, and versatility have made them an indispensable tool for manufacturers seeking to improve their productivity and product quality. As a leading manufacturer of these groundbreaking tools, {company} continues to drive innovation and set new benchmarks for excellence in the industry.
In conclusion, tungsten carbide molding dies represent a significant advancement in the manufacturing industry. Their exceptional durability, precision, and versatility make them an essential tool for a wide range of applications, from cold-heading and cold-forming to the production of non-metallic materials. {Company} stands at the forefront of this technology, leveraging their expertise and state-of-the-art facilities to produce high-quality tungsten carbide molding dies that meet the unique needs of their clients. With a commitment to innovation and continuous improvement, {company} is poised to lead the way in shaping the future of manufacturing with tungsten carbide molding dies.
Company News & Blog
Highly Wear-Resistant Carbide Parts for Industrial Applications
Carbide Wear Resistance Parts are revolutionizing the industrial machinery and equipment industry. These parts, made from high-quality carbide material, offer exceptional wear resistance and durability, making them an ideal choice for various applications in abrasive and high-stress environments.{Company name} is a leading manufacturer of these carbide wear resistance parts, and they have been delivering innovative solutions to their customers for over a decade. Their commitment to quality and customer satisfaction has positioned them as a trusted partner for businesses across a wide range of industries.The secret behind the superior performance of {Company name}'s carbide wear resistance parts lies in their advanced manufacturing processes and the use of premium-grade carbide materials. These parts are meticulously engineered to withstand extreme conditions, including high temperatures, heavy loads, and abrasive materials. As a result, they outperform traditional steel and iron components, offering longer service life and reduced maintenance requirements.One of the key benefits of {Company name}'s carbide wear resistance parts is their ability to improve the overall efficiency and productivity of industrial equipment. By incorporating these parts into their machinery, businesses can minimize downtime and reduce the need for frequent replacements, resulting in significant cost savings over time. Additionally, the enhanced wear resistance of these parts helps to maintain the precision and performance of equipment, ensuring consistent and reliable operation.{Company name} offers a comprehensive range of carbide wear resistance parts to meet the diverse needs of their customers. From cutting tools and wear plates to wear rings and nozzles, their product portfolio is designed to address the most demanding applications in industries such as mining, construction, energy, and manufacturing. Moreover, they have the capability to customize parts according to specific requirements, providing tailored solutions for unique challenges.In addition to their product excellence, {Company name} is also committed to providing exceptional customer service and technical support. Their team of experts works closely with clients to understand their needs and recommend the best-suited solutions. Furthermore, the company places a strong emphasis on continuous research and development, ensuring that their products remain at the forefront of technological advancements.As a testament to their success, {Company name} has established a strong presence in both domestic and international markets. Their carbide wear resistance parts have been adopted by leading companies around the world, contributing to the improved performance and reliability of their operations. With a reputation for excellence and a proven track record of delivering value to their customers, {Company name} continues to set the standard for quality and innovation in the industry.Looking ahead, {Company name} is poised to further expand its product offerings and reach new markets, leveraging its expertise and resources to meet the evolving needs of the industrial sector. As industrial machinery and equipment continue to advance, the demand for high-performance wear resistance parts will only grow, and {Company name} is well-positioned to lead the way in this space.In conclusion, {Company name}'s carbide wear resistance parts are setting a new benchmark for performance and reliability in the industrial sector. With their unmatched quality, durability, and versatility, these parts are driving efficiency and cost-effectiveness for businesses worldwide. As the industry continues to evolve, {Company name} remains at the forefront, delivering innovative solutions that empower businesses to thrive in challenging environments.
5 Things to Consider When Shopping for a New Mill Roller
[Company Name] Introduces New Mill Roller technology to Revolutionize the Manufacturing IndustryIn the fast-paced world of manufacturing, innovation and efficiency are key factors in staying ahead of the competition. [Company Name], a leading provider of industrial solutions, has once again demonstrated its commitment to cutting-edge technology with the introduction of its new mill roller.The mill roller plays a critical role in various industries such as agricultural, food processing, and chemical manufacturing. It is responsible for grinding, crushing, or cutting materials to the desired size, making it a vital component in the production process. With the demand for high-quality products and faster production times on the rise, [Company Name] recognized the need for a more advanced and efficient mill roller technology.The new mill roller developed by [Company Name] is a game-changer in the industry. It is equipped with state-of-the-art features that are designed to enhance performance, reliability, and productivity. The innovative design and engineering of the mill roller allow for precise and consistent results, ensuring a higher quality of output. Additionally, the technology utilized in the new mill roller significantly reduces energy consumption, making it an environmentally friendly solution for manufacturers.One of the key highlights of the new mill roller is its versatility. It can accommodate a wide range of materials, from grains and spices to minerals and chemicals, making it suitable for various applications across different industries. This versatility not only provides flexibility for manufacturers but also increases the overall efficiency of the production process.The new mill roller is also designed with ease of maintenance in mind. With a focus on reducing downtime and maximizing uptime, [Company Name] has incorporated features that simplify the maintenance and servicing of the equipment. This ensures that production lines can operate at peak performance without the hassle of frequent breakdowns or costly repairs.The introduction of the new mill roller by [Company Name] marks a significant milestone in the manufacturing industry. It sets a new standard for efficiency, reliability, and quality, catering to the evolving needs of producers worldwide. By embracing this cutting-edge technology, manufacturers can now streamline their operations and deliver superior products to their customers.In addition to the new mill roller, [Company Name] offers a comprehensive range of industrial solutions that cater to various sectors, including mining, construction, and agriculture. Its commitment to delivering innovative and sustainable technologies has earned it a reputation as a trusted partner for businesses seeking to enhance their production processes.With a global presence and a team of experts dedicated to research and development, [Company Name] continues to push the boundaries of what is possible in the manufacturing industry. Its investment in advanced technologies, such as the new mill roller, demonstrates its unwavering commitment to providing cutting-edge solutions that drive progress and success for its clients.The launch of the new mill roller is a testament to [Company Name]'s dedication to innovation and customer satisfaction. As it continues to expand its portfolio of groundbreaking technologies, the company remains a driving force in the evolution of the manufacturing sector. By harnessing the power of advanced engineering and design, [Company Name] is poised to empower manufacturers with the tools they need to thrive in a competitive and rapidly changing market.In conclusion, the introduction of the new mill roller by [Company Name] represents a leap forward in the manufacturing industry. Its advanced features, versatility, and focus on efficiency and reliability position it as a game-changer for producers seeking to elevate their production processes. With [Company Name]'s unwavering commitment to innovation and excellence, the future of manufacturing looks brighter than ever.
High-Quality Tungsten Carbide Cold Heading Dies for Efficient Production
Tungsten Carbide Cold Heading Dies: Revolutionizing the Manufacturing IndustryIn the manufacturing industry, precision and durability are key factors for achieving high-quality products. Cold heading dies play a crucial role in shaping metal wires and rods into intricate shapes and sizes to meet the demands of various industries such as automotive, construction, and electronics. With the advancement of technology, tungsten carbide cold heading dies have emerged as the game-changer in the manufacturing sector.Tungsten carbide is a compound composed of tungsten and carbon atoms, known for its exceptional hardness and resistance to wear and corrosion. These properties make tungsten carbide an ideal material for cold heading dies, offering superior performance and extended lifespan compared to traditional die materials. As a result, manufacturers can achieve higher production efficiency and cost savings in the long run.One company at the forefront of producing high-quality tungsten carbide cold heading dies is [Company Name]. With decades of experience in the industry, the company has established itself as a leading provider of precision tooling solutions for various manufacturing processes. Their commitment to innovation and continuous improvement has led to the development of advanced tungsten carbide dies that meet the demands of modern manufacturing operations.The key advantage of tungsten carbide cold heading dies lies in their ability to withstand extreme pressure and wear, making them suitable for high-speed and high-volume production environments. This results in enhanced productivity and reduced downtime for die maintenance and replacement, ultimately driving down manufacturing costs. Additionally, the superior wear resistance of tungsten carbide ensures consistent product quality and dimensional accuracy, meeting the stringent requirements of end-use applications.Furthermore, tungsten carbide cold heading dies enable manufacturers to expand their capabilities in producing complex and intricate part geometries. The exceptional hardness of the material allows for precise forming and shaping of metals, contributing to the production of high-precision components for a wide range of industries. This versatility opens up new opportunities for manufacturers to explore innovative designs and engineering solutions, meeting the evolving needs of the market.In addition to their performance benefits, tungsten carbide cold heading dies contribute to environmental sustainability by reducing waste and energy consumption. The extended lifespan of these dies minimizes the need for frequent replacements, leading to less material waste and lower carbon footprint in the manufacturing process. Furthermore, the efficiency gains achieved through the use of tungsten carbide dies result in energy savings, aligning with the global push towards greener manufacturing practices.As the demand for high-quality and complex metal components continues to grow, the adoption of tungsten carbide cold heading dies is set to become a standard in the manufacturing industry. Companies like [Company Name] are playing a pivotal role in driving this transition, providing manufacturers with reliable and advanced tooling solutions to meet the evolving demands of the market.In conclusion, tungsten carbide cold heading dies are revolutionizing the manufacturing industry, offering unmatched performance, durability, and versatility for shaping metal components. With [Company Name]'s expertise and dedication to innovation, manufacturers can leverage the benefits of tungsten carbide dies to achieve higher productivity, cost savings, and environmental sustainability. The widespread adoption of these advanced tooling solutions is set to drive the next wave of efficiency and precision in the manufacturing sector.
High-Quality Cold Heading Dies for YG25C Material
YG25C Cold Heading Dies Show Outstanding Performance in Precision ManufacturingWith the advancement of technology and the demand for precision engineering, the manufacturing industry has been constantly pushing the boundaries to achieve higher levels of accuracy and efficiency. Cold heading, a process used to form metal parts at room temperature, plays a crucial role in this pursuit of precision manufacturing. And in the world of cold heading dies, YG25C has emerged as a powerful player with its outstanding performance and reliability.Cold heading dies are essential tools used in the production of fasteners, such as screws, bolts, and nuts, as well as various automotive and aerospace components. These dies are subjected to extreme pressure and wear during the cold heading process, making their toughness and durability crucial to the quality of the final product. YG25C cold heading dies have proven to be reliable and effective in meeting these demands, making them a popular choice among manufacturers.The success of YG25C cold heading dies can be attributed to a combination of factors, including the superior properties of the material and advanced manufacturing techniques. YG25C is a grade of cemented carbide that is known for its high hardness, good wear resistance, and excellent toughness. These qualities make it an ideal material for cold heading dies, as it can withstand the extreme conditions of the cold heading process and maintain its shape and performance over time.In addition to the material itself, the manufacturing process also plays a significant role in the quality of YG25C cold heading dies. The company behind YG25C cold heading dies has invested heavily in state-of-the-art equipment and technology to ensure that each die is produced with precision and consistency. This commitment to quality manufacturing has earned YG25C a reputation for reliability and performance in the industry.Furthermore, the company's dedication to research and development has led to continuous improvements in the design and performance of YG25C cold heading dies. By leveraging the latest advancements in materials science and engineering, the company has been able to develop dies that offer superior performance, longer tool life, and greater cost-efficiency for manufacturers.A key advantage of YG25C cold heading dies is their versatility and ability to handle a wide range of materials, including steel, aluminum, copper, and titanium. This flexibility makes them an attractive choice for manufacturers working with diverse materials and looking to streamline their production processes. Whether it's mass-producing standard fasteners or creating complex, custom parts, YG25C cold heading dies have proven to be up to the task.Beyond the technical aspects, the company's commitment to customer service and support has also contributed to the success of YG25C cold heading dies. With a dedicated team of experts and technicians, the company provides extensive technical assistance, training, and after-sales support to help manufacturers optimize the performance of YG25C cold heading dies in their specific production environments.In conclusion, YG25C cold heading dies have established themselves as a leading choice for manufacturers seeking precision, reliability, and efficiency in their cold heading processes. With their exceptional material properties, advanced manufacturing techniques, and commitment to continuous improvement, YG25C cold heading dies are set to play a key role in the future of precision manufacturing. As the demand for high-quality, complex metal components continues to grow, YG25C cold heading dies are poised to meet the challenges of the industry head-on.
Top Uses and Benefits of Tungsten Carbide – Your Guide to this Hard Metal
As the world continues to progress, advancements in technology and industry are constantly being made. One of the most important components in this growth is the materials used for industrial manufacturing. Tungsten carbide, a material that has been used in various industries for decades, continues to be a vital material that is widely used due to its superior strength and durability. One of the leading manufacturers of tungsten carbide is the company {removed for privacy}, which has become a renowned company thanks to its high-quality tungsten carbide products.{Removed for privacy} has been in the industry since 2010 and has since then continued to grow and expand its products and services. Its primary focus is to provide high-quality tungsten carbide products and services to various industries such as aerospace, automotive, energy, and many more. The company has been able to maintain its position as a leading manufacturer of tungsten carbide due to its attention to detail, high-quality standards, and rigorous testing processes.One of the company's flagship products is the Yg8 tungsten carbide, which is widely used in various industries. Yg8 tungsten carbide is unique due to its highly abrasive nature, which makes it suitable for applications that require high wear resistance. The material is also known for its superior toughness, making it highly resistant to impact and deformation. The Yg8 tungsten carbide is produced using a carefully crafted process, which guarantees its resilience and strength, making it an ideal material for drilling, mining, and other industrial applications.The Yg8 tungsten carbide is made of a combination of tungsten and carbon, which are both highly durable materials. Tungsten carbide is formed when tungsten is combined with carbon at extreme heat, which creates a highly robust and durable material. A significant advantage of tungsten carbide is its ability to withstand extreme temperatures, making it suitable for high-temperature industrial applications.The Yg8 tungsten carbide manufactured by {removed for privacy} has many advantages compared to other materials. For instance, Yg8 tungsten carbide maintains its strength and rigidity even in extreme temperatures and harsh environments, which makes it ideal for industries such as oil and gas, where high levels of wear and tear are prevalent. It is also resistant to corrosion, which makes it ideal for use in marine and saltwater applications.Apart from its superior strength and durability, Yg8 tungsten carbide is also highly resistant to deformation, chip formation, and breakage. Additionally, the material is highly versatile, and can be molded into various shapes and sizes, making it ideal for creating complex tooling structures. Furthermore, {removed for privacy} offers customized solutions for specific industrial needs, ensuring that clients receive products that meet their specific requirements.One of the primary uses of tungsten carbide is in cutting tools such as drills, milling cutters, and other machining tools. Due to its highly abrasive nature, Yg8 tungsten carbide is ideal for these applications, making it the preferred material for manufacturing cutting tools. Additionally, Yg8 tungsten carbide is also widely used in the manufacturing of high-quality wear parts for various industrial applications. These include parts used in pumps, valves, mining machinery, and many more.The Yg8 tungsten carbide manufactured by {removed for privacy} is also highly resistant to fatigue and wear, making it ideal for applications where wear and tear are prevalent. The material's high resilience to fatigue ensures that machinery and equipment can run for extended periods without the risk of breakdowns, ensuring that industries can maintain their production processes without interruptions.In conclusion, Yg8 tungsten carbide is a highly versatile, highly durable, and effective material that has found wide applications in various industries. {Removed for privacy} continues to be at the forefront of manufacturing and supplying high-quality tungsten carbide products to various industries globally. With its attention to detail, rigorous testing processes, and custom solutions, {removed for privacy} is the perfect partner for industries that require high-quality tungsten carbide products and services.
Tungsten Carbide Sleeves for YG8 and YG12 Applications
[Company Name], a leader in the manufacturing and supply of high-quality tungsten carbide products, has recently introduced two new products to its extensive line of cutting tools and wear parts. The YG8 and YG12 Tungsten Carbide Sleeves are the latest additions to the company's portfolio, offering customers enhanced performance and durability for a wide range of industrial applications.Tungsten carbide is well-known for its exceptional hardness, wear resistance, and strength, making it an ideal material for demanding industrial environments. The YG8 and YG12 Tungsten Carbide Sleeves are designed to provide superior protection and performance in high-stress applications such as mining, oil and gas drilling, and construction.The YG8 Tungsten Carbide Sleeve is formulated with a precise combination of tungsten carbide and cobalt, resulting in a high-performance material that is capable of withstanding extreme wear and abrasion. This makes it an ideal choice for use in downhole tools, pumps, and other components that are subjected to harsh operating conditions. The YG8 Sleeve is available in a range of sizes and configurations to suit various equipment requirements.Meanwhile, the YG12 Tungsten Carbide Sleeve is engineered for applications that demand even higher levels of toughness and impact resistance. With a higher cobalt content and a specialized manufacturing process, the YG12 Sleeve offers exceptional resistance to chipping, fracturing, and thermal cycling. This makes it well-suited for use in cutting tools, fluid control valves, and other critical components where reliability is paramount.Both the YG8 and YG12 Tungsten Carbide Sleeves are precision-machined to tight tolerances, ensuring a perfect fit and maximum effectiveness in their intended applications. They are also capable of being customized with various surface treatments and coatings to further enhance their performance and longevity.[Company Name] has established a strong reputation for delivering top-quality tungsten carbide products to customers worldwide. With state-of-the-art manufacturing facilities and a team of experienced engineers and metallurgists, the company is committed to providing innovative solutions that address the evolving needs of the industrial sector."Our YG8 and YG12 Tungsten Carbide Sleeves demonstrate our ongoing dedication to product development and customer satisfaction," said a spokesperson for [Company Name]. "These new offerings represent the latest advancements in tungsten carbide technology, providing our customers with reliable solutions that deliver exceptional performance in the most challenging environments."In addition to the YG8 and YG12 Tungsten Carbide Sleeves, [Company Name] offers a comprehensive range of tungsten carbide products, including cutting inserts, wear parts, and tooling components. The company also provides custom machining and engineering services to support specialized requirements and applications.With a commitment to quality, innovation, and technical expertise, [Company Name] is poised to continue leading the way in the global market for tungsten carbide solutions. The introduction of the YG8 and YG12 Tungsten Carbide Sleeves reaffirms the company's dedication to pushing the boundaries of performance and reliability in industrial applications, and underscores its position as a trusted partner for businesses seeking cutting-edge solutions for their most demanding challenges.
Durable Tungsten Carbide Wire Rolls for Industrial Applications
Tungsten Carbide Wire Rolls are a vital component in the wire drawing industry, playing a crucial role in the production of various metal wires. These rolls are well-known for their exceptional durability, wear resistance, and high performance, making them the preferred choice for wire drawing applications.{Company Name} is a leading manufacturer and supplier of Tungsten Carbide Wire Rolls, offering a wide range of products tailored to meet the specific needs of wire drawing operations. With a strong focus on quality, innovation, and customer satisfaction, {Company Name} has established itself as a trusted partner for wire drawing companies worldwide.Tungsten Carbide Wire Rolls, also known as TC Rolls, are widely used in the wire drawing process to reduce the cross-sectional area of a wire while simultaneously increasing its length. This process involves pulling a metal wire through a series of dies, with TC Rolls playing a critical role in ensuring smooth, consistent, and efficient wire drawing operations. The exceptional hardness of Tungsten Carbide enables these rolls to withstand the high pressures and abrasion encountered during wire drawing, resulting in a longer service life and reduced downtime for maintenance.{Company Name}'s Tungsten Carbide Wire Rolls are manufactured using state-of-the-art technology and high-quality materials to ensure superior performance and reliability. The company's team of skilled engineers and experts work closely with wire drawing companies to understand their specific requirements and provide customized solutions that meet their unique production needs. Whether it's for drawing stainless steel, aluminum, copper, or other metal wires, {Company Name} offers a comprehensive range of TC Rolls designed to deliver exceptional results.In addition to their outstanding durability, Tungsten Carbide Wire Rolls from {Company Name} are also designed to optimize wire drawing processes, resulting in improved efficiency and cost savings for wire drawing companies. The precise and uniform profile of these rolls ensures consistent wire quality, reducing the need for post-processing and improving overall productivity. Furthermore, {Company Name} offers a range of surface treatments and coatings for TC Rolls to further enhance their performance and extend their service life, providing customers with a cost-effective and sustainable solution for their wire drawing operations.With a commitment to continuous improvement and innovation, {Company Name} is at the forefront of developing advanced Tungsten Carbide Wire Rolls that push the boundaries of wire drawing technology. By leveraging the latest manufacturing techniques and materials, the company is able to offer TC Rolls with enhanced wear resistance, surface finish, and dimensional accuracy, setting new benchmarks for performance and quality in the wire drawing industry.In conclusion, Tungsten Carbide Wire Rolls from {Company Name} are the preferred choice for wire drawing companies looking to optimize their production processes and achieve superior results. With a focus on quality, innovation, and customer satisfaction, {Company Name} continues to set the standard for TC Rolls, providing wire drawing companies with a reliable and high-performance solution for their wire drawing operations. As the demand for high-quality metal wires continues to grow, {Company Name} remains committed to supporting the wire drawing industry with cutting-edge solutions that drive success and sustainability.
The Ultimate Guide to Tungsten Carbide Sleeves: Everything You Need to Know
Tungsten Carbide Sleeves: Revolutionizing the Industrial SectorIn today's rapidly evolving industrial landscape, companies are constantly in search of innovative solutions that can enhance their operational efficiency, mitigate risks, and reduce costs. One such groundbreaking solution making waves in the industry is the Tungsten Carbide Sleeve. Renowned for its remarkable durability and versatility, Tungsten Carbide Sleeves are playing a pivotal role in revolutionizing multiple industrial sectors.Tungsten Carbide Sleeves, manufactured using cutting-edge technology, are designed to withstand extreme working conditions. The high hardness, wear resistance, and excellent thermal stability of this material make it an ideal choice for a wide range of applications, including oil and gas drilling, mining, metalworking, and automotive manufacturing.The emergence of Tungsten Carbide Sleeves has been a game-changer for the oil and gas industry. Drilling operations in this sector often encounter highly abrasive and corrosive environments, where equipment failure can lead to catastrophic consequences. Tungsten Carbide Sleeves provide the necessary protection, extending the lifespan of drilling tools and reducing costly downtime. Their exceptional hardness and wear resistance enable these sleeves to endure relentless drilling, resulting in enhanced drilling efficiency and productivity.Similarly, the mining industry has also reaped the benefits of Tungsten Carbide Sleeves. Mining operations involve handling abrasive materials, which can cause rapid wear and tear on equipment. By implementing Tungsten Carbide Sleeves, mining companies have experienced a significant reduction in maintenance costs and improved equipment performance. These sleeves not only enhance the lifespan of mining tools but also contribute to increased mining productivity.The metalworking sector, which encompasses diverse industries such as aerospace, automotive, and machining, has also embraced Tungsten Carbide Sleeves as a game-changing solution. The exceptional hardness and wear resistance of these sleeves make them an excellent choice for cutting and machining applications. They ensure precision and accuracy, resulting in high-quality finished products. Additionally, Tungsten Carbide Sleeves provide thermal stability, reducing the risk of thermal deformation during high-speed machining processes. This has enabled companies to enhance their manufacturing capabilities and meet the ever-increasing demands of their customers.Automotive manufacturing, a sector constantly striving for innovation and efficiency, has also witnessed the transformative power of Tungsten Carbide Sleeves. The high wear resistance of these sleeves has prolonged the life of critical automotive components, such as engine valves and pistons. This has not only reduced the need for frequent replacements but also contributed to improved engine performance and fuel efficiency. Moreover, Tungsten Carbide Sleeves ensure precision and quality during the manufacturing process, contributing to the overall reliability and safety of vehicles.One company at the forefront of Tungsten Carbide Sleeve manufacturing is . With a commitment to innovation and a passion for excellence, has become a trusted name in the industry. Their state-of-the-art manufacturing facility, combined with a team of highly skilled engineers, ensures superior quality and performance of their Tungsten Carbide Sleeves. utilizes advanced technologies and stringent quality control processes to produce Tungsten Carbide Sleeves that exceed industry standards. Their sleeves undergo rigorous testing to ensure durability, exceptional wear resistance, and compatibility with various applications. With a focus on customer satisfaction, offers customized solutions to meet specific requirements, regardless of the industry.As the demand for high-performance materials continues to grow, Tungsten Carbide Sleeves have emerged as a game-changing solution across multiple industrial sectors. With their exceptional durability, wear resistance, and thermal stability, these sleeves are revolutionizing the way businesses operate. As companies strive for efficiency, cost reduction, and innovation, Tungsten Carbide Sleeves prove to be an indispensable asset in achieving a competitive edge in the global market.In conclusion, the emergence of Tungsten Carbide Sleeves has revolutionized the industrial sector by providing exceptional durability, wear resistance, and thermal stability. Their diverse applications in oil and gas drilling, mining, metalworking, and automotive manufacturing have paved the way for increased operational efficiency, reduced costs, and improved productivity. As leads the way in Tungsten Carbide Sleeve manufacturing, businesses can harness the transformative power of these sleeves to stay at the forefront of innovation and achieve sustainable growth.
Enhance Your Turning Applications with High-Performance Carbide Inserts
Carbide Inserts for Turning Applications Offer Enhanced Durability and PrecisionCarbide inserts for turning applications have emerged as one of the popular cutting tools in the manufacturing industry. These inserts are designed with high-performance materials, which enhance their durability and precision capabilities. Carbide inserts are cutting-edge technology tools that can be used for turning, milling, drilling, and other cutting applications.A leading manufacturer and supplier of carbide inserts has recently introduced a range of carbide inserts for turning applications. The company's new products are designed to cater to the needs of all manufacturing industries, ensuring that clients receive superior quality and precision tools.The company has been providing the manufacturing industry with premium quality carbide inserts for more than a decade. Their team of experts has vast experience in the field of machining technology, and they employ innovative techniques to produce cutting-edge products that cater to the needs of the clients.Carbide inserts are widely used in turning applications because of their superior quality and precision capabilities. They are made from a combination of tungsten carbide and cobalt, which makes them harder than high-speed steel. Carbide inserts are also resistant to high temperatures, ensuring that they can withstand the heat generated during the cutting process.The company's new line of carbide inserts for turning applications is designed to offer improved performance, higher durability, and precision. The new range is available in different grades and designs, making it suitable for multiple turning applications, from roughing to finishing. The range includes inserts, inserts with chipbreakers, and inserts for heavy-duty roughing, among others.The company's carbide inserts for turning applications are highly versatile and can be used for a wide range of materials. They are ideal for cutting hard materials like steel, stainless steel, cast iron, and exotic alloys. The inserts' smooth finish and stable performance ensure that there is no chipping or breakage during the cutting process, which makes them ideal for industrial applications.Carbide inserts are designed to provide high accuracy and precision. The inserts' cutting edge produces a smooth finish, making it ideal for applications that require a high degree of precision. Additionally, carbide inserts are designed to produce chips that are easy to manage and dispose of, thus reducing the machine's downtime.The new range of carbide inserts for turning applications from the company is also cost-effective. Carbide inserts are designed to last longer than high-speed steel, which reduces the need for frequent changes and replacement. Additionally, the company's cost-effective pricing policy ensures that clients can obtain high-quality, reliable carbide inserts at an affordable price.The company's carbide inserts for turning applications are also environmentally friendly. Carbide inserts produce chips that can be recycled, which reduces manufacturing waste and environmental pollution. The company's products are designed with environmental responsibility in mind, and they are committed to reducing the carbon footprint associated with manufacturing.The company's carbide inserts for turning applications are easy to use and maintain. The inserts' high-performance materials make them resistant to wear and tear, which means less maintenance is required. Additionally, the company provides extensive technical support to ensure that clients can achieve the best results from their products.The company's commitment to client satisfaction is evident in the quality of their products and services. They have a team of experts who are always available to provide technical support and advice on the best carbide inserts for specific applications. The company also offers customized carbide inserts, ensuring that clients can obtain products that cater to their specific needs.In conclusion, carbide inserts for turning applications from the company are a game-changer in the manufacturing industry. They offer enhanced durability, precision, and versatility, making them ideal for a wide range of turning applications. The company's commitment to quality and affordability ensures that clients can obtain high-quality products at an affordable price, while their eco-friendly approach reduces manufacturing waste and environmental pollution.
Durable Cemented Carbide Finish Plates for High-Performance Applications
Cemented Carbide Finish Plates, a Key Product of Leading Manufacturer {}Cemented carbide finish plates are a crucial component in a wide range of industrial applications, and they play a significant role in ensuring the efficiency and precision of various machining processes. A leading manufacturer in the industry, {} is at the forefront of producing high-quality cemented carbide finish plates that meet the stringent requirements of its global customer base.With a strong focus on research and development, {} has continuously invested in cutting-edge technologies and innovative processes to produce cemented carbide finish plates that offer exceptional performance and durability. The company's commitment to quality and excellence has solidified its position as a trusted supplier of cemented carbide finish plates to industries such as automotive, aerospace, oil and gas, and general engineering.One of the key features of {}'s cemented carbide finish plates is their superior wear resistance, which enables them to withstand the extreme conditions and high stress encountered during machining operations. This outstanding durability not only extends the operational life of the finish plates but also contributes to the overall productivity and cost-effectiveness of the manufacturing processes in which they are used.In addition to their exceptional wear resistance, {}'s cemented carbide finish plates are also known for their high hardness and excellent thermal stability. These properties are essential for maintaining the dimensional accuracy and surface finish of machined components, particularly in high-precision applications where tight tolerances and smooth surface textures are critical.Furthermore, {} offers a diverse range of cemented carbide finish plates with varying compositions and geometries to meet the specific needs of different machining operations. Whether it's for turning, milling, or drilling applications, customers can rely on {} to provide customized solutions that optimize their manufacturing processes and enhance the quality of their end products.As a responsible manufacturer, {} is also committed to sustainability and environmental stewardship in the production of its cemented carbide finish plates. The company adheres to stringent environmental standards and employs eco-friendly practices to minimize its carbon footprint and reduce waste generation, ensuring that its operations are not only efficient but also environmentally conscious.Moreover, {} places a strong emphasis on customer satisfaction and service, providing comprehensive technical support and consultation to help customers select the most suitable cemented carbide finish plates for their specific applications. The company's team of experts works closely with customers to understand their requirements and challenges, offering valuable insights and solutions that drive operational efficiency and product quality.In line with its dedication to innovation and continuous improvement, {} is constantly exploring new opportunities to advance the capabilities of its cemented carbide finish plates, whether through the development of new materials, the enhancement of manufacturing processes, or the integration of advanced coatings and surface treatments.Looking ahead, {} remains committed to maintaining its leadership in the production of high-performance cemented carbide finish plates while exploring new frontiers in material science and engineering. With a strong foundation of expertise, state-of-the-art facilities, and a customer-centric approach, {} is well-positioned to meet the evolving demands of the industry and drive the next wave of advancements in cemented carbide technology.