High-quality cold forging die for HSS material
By:Admin
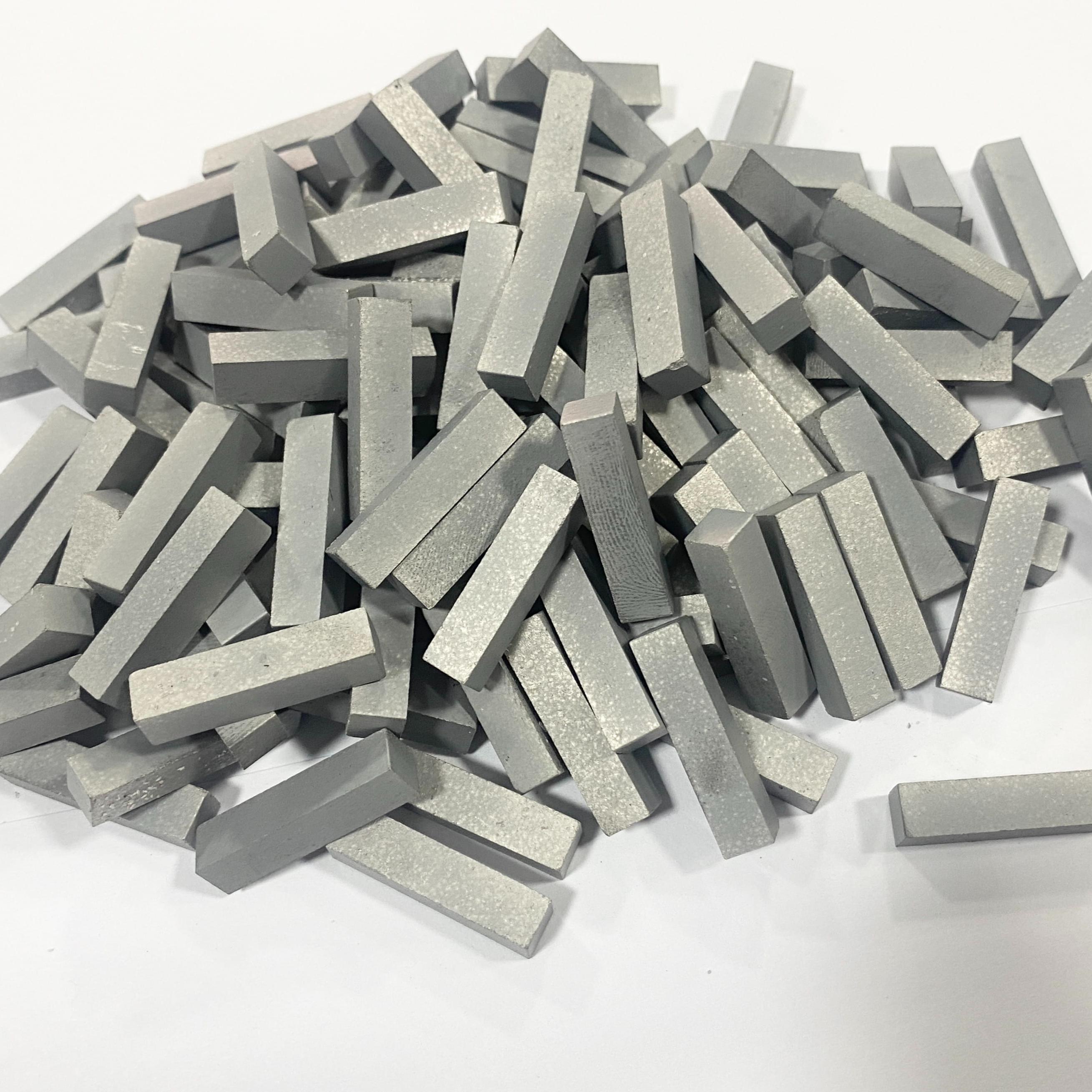
The manufacturing industry has always been driven by innovation and technology. The constant quest to improve efficiency and productivity has led to the development of various new techniques and tools. One such breakthrough in the industry is the HSS cold forging die. This cutting-edge technology has the potential to revolutionize the manufacturing process, making it faster, more efficient, and cost-effective.
HSS cold forging die, made of high-speed steel, is designed to withstand high-pressure and high-temperature operations. This die has the ability to shape and mold materials, such as metal, with precision and accuracy. Its exceptional durability and resistance to wear and tear make it a preferred choice for manufacturers across different industries.
One company that has been at the forefront of developing and providing HSS cold forging dies is [Company Name]. With years of experience and expertise in the field of manufacturing technology, [Company Name] has become a trusted name in the industry. The company's commitment to quality and innovation has enabled it to stay ahead of the competition and meet the evolving needs of its customers.
[Company Name] offers a wide range of HSS cold forging dies, catering to the diverse requirements of its clients. Whether it is for automotive parts, industrial components, or consumer goods, the company has the capability to provide customized solutions that meet the highest standards of quality and performance. Its state-of-the-art manufacturing facilities and a team of skilled professionals ensure that each die is crafted with precision and attention to detail.
The HSS cold forging die offered by [Company Name] has been tested and proven to deliver outstanding results. Its superior strength and toughness enable it to withstand the rigors of the forging process, without compromising on the accuracy and consistency of the finished product. This ensures that manufacturers can produce high-quality parts with minimal downtime and maintenance.
In addition to its product offerings, [Company Name] also provides comprehensive support and services to its clients. From the initial design and development phase to installation and maintenance, the company is committed to ensuring the success of its customers. Its technical expertise and customer-centric approach have made it a preferred partner for businesses seeking reliable and efficient manufacturing solutions.
The introduction of HSS cold forging die has already started to make waves in the manufacturing industry. Its ability to improve productivity, reduce production costs, and enhance the quality of finished products has caught the attention of manufacturers worldwide. With [Company Name] leading the way in providing top-notch HSS cold forging dies, the industry is set to witness a significant transformation in the way parts and components are manufactured.
As the demand for high-quality, precision-engineered parts continues to rise, the role of HSS cold forging die in the manufacturing process will only become more crucial. Its potential to revolutionize the industry and set new benchmarks for efficiency and reliability is undeniable. With [Company Name] at the helm, businesses can expect to experience a new era of manufacturing excellence.
In conclusion, the advent of HSS cold forging die has opened up new possibilities for the manufacturing industry. Its ability to deliver superior results and optimize production processes has the potential to drive growth and innovation. With [Company Name] leading the charge in providing cutting-edge solutions, the future of manufacturing looks brighter than ever.
Company News & Blog
High-Performance Tungsten Carbide Plates for Various Industrial Applications
[Company Name] is proud to introduce its latest product, the YG6 YG8 Tungsten Carbide Plates, which are designed to meet the increasing demand for high-quality and durable tungsten carbide products in the market. These plates are manufactured using advanced technology and high-grade materials to ensure superior performance and reliability in various industrial applications.The YG6 YG8 Tungsten Carbide Plates are ideal for use in the manufacturing of cutting tools, wear parts, and other applications that require high levels of hardness, toughness, and resistance to wear and abrasion. These plates are known for their exceptional hardness and strength, making them ideal for use in harsh and demanding conditions.One of the key features of the YG6 YG8 Tungsten Carbide Plates is their exceptional wear resistance, which makes them suitable for use in high-stress environments where other materials may fail. This makes them an ideal choice for industries such as mining, construction, and metalworking, where tools and equipment are subjected to extreme wear and tear.In addition to their outstanding wear resistance, the YG6 YG8 Tungsten Carbide Plates also offer excellent corrosion resistance, making them suitable for use in corrosive environments. This makes them a versatile and cost-effective choice for a wide range of applications, including the manufacturing of pumps, valves, and other components that are exposed to corrosive substances.The YG6 YG8 Tungsten Carbide Plates are also known for their superior dimensional stability, which ensures that they maintain their shape and size even under high temperature and pressure conditions. This makes them an ideal choice for applications where precision and accuracy are essential, such as the manufacturing of precision tools and equipment.At [Company Name], we are committed to quality and innovation, and the YG6 YG8 Tungsten Carbide Plates are a testament to our dedication to providing our customers with the best products and solutions. We use advanced manufacturing processes and strict quality control measures to ensure that our products meet the highest standards of performance and reliability.In addition to the YG6 YG8 Tungsten Carbide Plates, we offer a wide range of tungsten carbide products to meet the diverse needs of our customers. Our products are widely used in various industries, including aerospace, automotive, oil and gas, and many others, where performance and reliability are essential.We take pride in our ability to provide customized solutions to our customers, and we work closely with them to develop products that meet their specific requirements. Our team of experts is committed to delivering exceptional customer service and technical support to ensure that our customers get the most out of our products.In conclusion, the YG6 YG8 Tungsten Carbide Plates from [Company Name] are a testament to our commitment to quality, innovation, and customer satisfaction. With their exceptional wear resistance, corrosion resistance, and dimensional stability, these plates are an ideal choice for a wide range of industrial applications. We are confident that these plates will exceed our customers' expectations and provide them with the performance and reliability they need.
High-Quality Tungsten Carbide for Punching Applications
Tungsten Carbide for Punching: The Perfect Solution for Precision ToolingFor many industries, the demand for precision tooling solutions that can deliver consistent and accurate results is growing rapidly. Thanks to the latest technological advancements, companies are now able to rely on cutting-edge materials such as tungsten carbide to meet these demanding requirements. One company at the forefront of this innovation is known for providing top-tier tungsten carbide tooling solutions to clients worldwide.As a leading supplier of tungsten carbide products, {} is proud to introduce its high-quality punching solutions. Tungsten carbide is a versatile and durable material that is ideally suited for punching applications due to its exceptional hardness, wear resistance, and toughness. When used in punching tools, tungsten carbide offers superior performance and longevity, making it the perfect choice for precision tooling needs.At {}, we are dedicated to meeting the unique needs of our customers by providing them with innovative and reliable tungsten carbide punching solutions. Our commitment to quality and excellence has made us a trusted partner for companies across a wide range of industries, including automotive, aerospace, medical, and more.One of the key advantages of using tungsten carbide for punching applications is its exceptional hardness. Tungsten carbide is one of the hardest materials available, ranking just below diamond on the Mohs scale. This high level of hardness allows tungsten carbide punching tools to maintain their sharpness and dimensional stability over extended periods of use, resulting in superior performance and increased productivity for our customers.Furthermore, tungsten carbide offers outstanding wear resistance, making it an ideal material for punching tools that are subjected to high-stress applications. Whether it's punching holes in thick metal sheets or forming intricate shapes in various materials, tungsten carbide punching tools can withstand the harshest working conditions without compromising on performance or reliability. This exceptional wear resistance ensures that our customers can rely on our punching solutions for long-term, cost-effective tooling needs.In addition to its hardness and wear resistance, tungsten carbide also exhibits exceptional toughness, which is crucial for withstanding the impact and shock loads experienced during punching operations. This unique combination of properties makes tungsten carbide an ideal material for punching tools, providing our customers with confidence in the durability and longevity of their tooling investments.With our advanced manufacturing capabilities and expertise in tungsten carbide technology, {} is able to deliver custom punching solutions that are tailored to the specific requirements of our customers. Whether it's a standard punch design or a highly complex, intricate tooling application, our team of experts can design and produce precision punching tools that meet the most demanding specifications and tolerances.In conclusion, the use of tungsten carbide for punching applications offers a wide range of benefits, including exceptional hardness, wear resistance, and toughness. As a trusted supplier of tungsten carbide tooling solutions, {} is dedicated to providing our customers with innovative and reliable punching solutions that meet their unique needs. With our commitment to quality, excellence, and customer satisfaction, companies can rely on us to deliver top-tier tungsten carbide punching tools that set new standards for precision and performance in the industry.For more information about our tungsten carbide punching solutions and other cutting-edge tooling products, please visit {}.
The Ultimate Guide to Tungsten Carbide Strips - Unveiling the Power of HR6A
Title: HR6A Tungsten Carbide Strips Revolutionizing Industrial ApplicationsIntroduction:In the competitive landscape of industrial manufacturing, quality and efficient tools are essential for achieving productivity and precision. One such innovation is the HR6A Tungsten Carbide Strips. With their exceptional hardness, wear resistance, and versatility, these carbide strips have been gaining attention in various industries. This article aims to shed light on the remarkable features of HR6A Tungsten Carbide Strips and their potential to revolutionize industrial applications.I. Understanding Tungsten Carbide:Tungsten carbide is a compound comprising equal parts of carbon and tungsten. Known for its extreme hardness, it is approximately three times harder than steel and can withstand high temperatures and abrasion. These characteristics make it an ideal material for manufacturing cutting tools, wear-resistant parts, and other industrial applications.II. HR6A Tungsten Carbide Strips:HR6A Tungsten Carbide Strips exemplify the superior properties of tungsten carbide. These strips are fabricated using advanced techniques, resulting in an exceptional combination of toughness, hardness, and wear resistance.1. Unparalleled Hardness:The HR6A Tungsten Carbide Strips possess an impressive hardness that allows them to cut through the toughest materials with ease. This hardness provides extended tool life and reduces downtime due to frequent tool replacements.2. Exceptional Wear Resistance:The wear resistance of HR6A Tungsten Carbide Strips ensures their durability even in harsh working conditions. Whether it is cutting, drilling, or shaping, these strips retain their sharpness, reducing the need for frequent replacements and enhancing overall productivity.3. Versatility in Applications:These carbide strips find applications in a wide range of industries. From machining and metalworking to mining and construction, the versatility of HR6A Tungsten Carbide Strips makes them an invaluable tool for various industrial applications.III. Industrial Applications and Benefits:The HR6A Tungsten Carbide Strips offer a myriad of benefits across several industries, maximizing efficiency, productivity, and overall performance.1. Machining and Metalworking Sector:In the metalworking industry, HR6A Tungsten Carbide Strips are widely used in cutting, planing, milling, and turning tools. Their high heat resistance and hardness enable precision machining, resulting in superior surface finishes and increased manufacturing speed.2. Mining and Construction Industry:In the mining and construction industry, HR6A Tungsten Carbide Strips are employed in the production of drilling tools and machinery parts. Their exceptional wear resistance ensures consistent performance, extended tool life, and reduced downtime, resulting in improved operational efficiency and cost-effectiveness.3. Woodworking and Plastic Processing:For woodworking and plastic processing applications, HR6A Tungsten Carbide Strips are used in cutting and shaping tools. Their hardness and abrasion resistance enable precise cutting, reduced material waste, and improved surface quality.IV. Outlook and Future Implications:The introduction of HR6A Tungsten Carbide Strips signifies a significant advancement in the industrial manufacturing sector. With their exceptional hardness, wear resistance, and versatility, these strips have the potential to redefine precision machining, mining, construction, and woodworking applications.The continuous research and development in tungsten carbide technology will likely lead to further enhancements in the performance and overall effectiveness of HR6A Tungsten Carbide Strips. As industries increasingly demand high-quality tools that combine durability, precision, and versatility, the future of HR6A Tungsten Carbide Strips looks promising.Conclusion:The HR6A Tungsten Carbide Strips have emerged as a game-changer in the industrial manufacturing landscape. With their unparalleled hardness, exceptional wear resistance, and versatility in various applications, these carbide strips are elevating the standards of precision machining, mining, construction, woodworking, and more. As the industry continues to embrace innovative solutions, HR6A Tungsten Carbide Strips will undoubtedly play a vital role in shaping the future of industrial applications.
Discover the Advantages of Carbide Inserts for Turning Tasks
Carbide Inserts for Turning Applications: The Future of Machining{Company Name} has recently introduced its newest line of carbide inserts for turning applications. These innovative inserts are designed to meet the demands of various cutting processes, and can be used for machining of many different types of materials. Carbide inserts have long been a preferred option for machining, and the latest product from {Company Name} has set a new standard in the industry.Carbide inserts are perfect for turning applications because they offer superior wear resistance. With their high level of hardness, these inserts can easily handle high-speed turning and continuous cutting processes. The new line of {Company Name} carbide inserts is made from a special grade of carbide that ensures maximum resistance to wear, heat, and corrosion. This unique formulation makes these inserts extremely durable, ensuring a longer tool life and lower operating costs.The new carbide inserts from {Company Name} are designed with specific geometries to improve machining performance. The inserts are also available in a range of coatings that are tailored to various applications. These coatings offer increased wear resistance, and they can provide better chip control and improved surface finish. The coatings are also highly wear-resistant, which helps to prolong the life of the inserts.The new {Company Name} carbide inserts are designed for advanced turning applications, such as finish turning, roughing, and semi-finishing operations. These inserts are also ideal for use in high-speed machining, where precision and reliability are crucial. With their exceptional hardness and wear resistance, {Company Name} carbide inserts can tackle a wide range of materials, including hardened steel, cast iron, and non-ferrous metals."We are proud to introduce our latest line of carbide inserts for turning applications," said the spokesperson from {Company Name}. "These inserts are the result of years of research and development, and we believe that they will set a new standard in the industry. Our carbide inserts offer superior performance in terms of wear resistance and machining performance, and they are designed to meet the demands of even the most challenging cutting processes."{Company Name} has a long track record of providing high-quality machining solutions to its customers. With its latest line of carbide inserts, the company has cemented its position as a leading provider of advanced cutting tools. The carbide inserts are manufactured using the latest technology and machining processes, and they are subjected to rigorous quality control procedures to ensure consistent performance.In addition to its new line of carbide inserts, {Company Name} also offers a range of other cutting tools and accessories. The company's product range includes drills, reamers, milling cutters, and tool holders, among other items. All of these products are designed to meet the demanding needs of modern manufacturing processes, and they are manufactured to the highest standards of quality and durability.Whether you are looking for a solution to improve your machining performance or simply looking for high-quality cutting tools, {Company Name} has the tools you need. The company's team of experts can provide guidance and support in selecting the right tools for your application, ensuring that you get the best possible value for your investment.In conclusion, the new line of carbide inserts from {Company Name} is a game-changer for turning applications. These innovative inserts offer superior wear resistance, machining performance, and durability, making them the go-to option for modern manufacturing processes. With its commitment to quality and customer service, {Company Name} is poised to become the leading provider of advanced cutting tools and accessories in the industry.
High-Quality Tungsten Carbide Pellet: A Versatile and Durable Material for Various Applications
Tungsten Carbide Pellet - The Future of Cutting ToolsTungsten carbide is a material that has been revolutionizing the field of cutting tools. Known for its exceptional hardness and wear resistance, tungsten carbide is used in a wide range of applications, from mining and drilling to manufacturing and construction. One company that has been at the forefront of this cutting-edge technology is {}. With their innovative tungsten carbide pellets, they have been setting new standards in the industry.Founded in {}, {} has been a leading manufacturer and supplier of tungsten carbide products for the past {} years. Their state-of-the-art production facilities and commitment to research and development have allowed them to consistently deliver high-quality products to their customers. They have built a solid reputation for providing innovative solutions for a variety of industries, including mining, construction, and metalworking.One of the key products that {} offers is their tungsten carbide pellets. These pellets are made from a mixture of tungsten and carbon powders, which are compressed and sintered at high temperatures to create a dense, hard, and wear-resistant material. The resulting pellets are then used to manufacture cutting tools, such as drills, end mills, and inserts, that are capable of withstanding the most demanding applications.The use of tungsten carbide in cutting tools offers several advantages over traditional materials. First and foremost, the hardness of tungsten carbide allows for higher cutting speeds and feeds, resulting in increased productivity and efficiency. Additionally, its exceptional wear resistance ensures a longer tool life, reducing the frequency of tool changes and associated downtime. This not only saves time and money but also increases the overall reliability of the cutting process.Furthermore, tungsten carbide has a high fracture toughness, making it less prone to chipping and breaking, even in the toughest machining conditions. This means that tools made from tungsten carbide can be used for a wider range of applications, and can handle more demanding cutting tasks without compromising performance or tool life.The team at {} is continuously working to improve their tungsten carbide pellets, conducting rigorous testing and analysis to ensure the highest quality and performance. They also collaborate closely with their customers to develop custom solutions that meet specific requirements and address unique challenges. This customer-centric approach has allowed {} to build strong, long-lasting relationships with their clients, who rely on them for cutting-edge products and technical expertise.In addition to their commitment to quality and innovation, {} is also dedicated to sustainability and environmental responsibility. They adhere to strict environmental standards in their manufacturing processes and continuously seek ways to minimize their impact on the environment. This includes investing in energy-efficient technologies, recycling materials, and reducing waste, all while maintaining the highest standards of product quality and performance.As the demand for high-performance cutting tools continues to grow, the importance of tungsten carbide in the manufacturing industry cannot be overstated. With its exceptional hardness, wear resistance, and toughness, tungsten carbide is poised to play a vital role in the future of cutting tool technology. Companies like {} are leading the way in developing and producing tungsten carbide products that push the boundaries of what is possible in the world of cutting tools.In conclusion, tungsten carbide pellets are at the forefront of cutting tool technology, offering unmatched performance and durability. With companies like {} leading the charge in innovation and quality, the future of cutting tools looks brighter than ever. As the manufacturing industry continues to evolve, tungsten carbide will undoubtedly remain a crucial material for meeting the demands of the modern world.
Carbide Wire Drawing Dies: Everything You Need to Know
Carbide Wire Drawing Dies - The Ultimate Solution for Wire Drawing ProcessesWire drawing is a critical process in the manufacturing of various wire products, including cables, electrical wires, and metal cords. This process involves pulling a metal wire through a series of dies to reduce its diameter and increase its length. To ensure the efficiency and quality of this process, the choice of wire drawing dies is of utmost importance.In this regard, the use of carbide wire drawing dies has emerged as a game-changer in the industry. Carbide, a compound of carbon and metal, is well-known for its exceptional hardness and wear resistance, making it an ideal material for wire drawing dies. With the ability to withstand high temperatures and maintain its shape under extreme pressure, carbide wire drawing dies offer superior performance and longevity compared to traditional die materials.One company that has been at the forefront of providing high-quality carbide wire drawing dies is {}. With decades of experience and expertise in the field, {} has established itself as a trusted manufacturer and supplier of carbide tools and dies for various industrial applications.With a state-of-the-art manufacturing facility and a team of skilled engineers and technicians, {} is capable of producing a wide range of carbide wire drawing dies to meet the diverse needs of its customers. From standard round wire dies to shaped dies for special applications, the company offers a comprehensive range of die designs to cater to the specific requirements of wire drawing operations.The key to the superior performance of {}'s carbide wire drawing dies lies in the precision engineering and advanced technology used in their production. By leveraging the latest CNC machining and grinding techniques, the company is able to achieve ultra-precise dimensions and surface finishes on its dies, ensuring smooth wire drawing processes and minimal downtime for its customers.In addition to their exceptional quality, {}'s carbide wire drawing dies are also known for their cost-effectiveness and sustainability. With their extended lifespan and minimal need for replacements, these dies help businesses reduce their overall production costs and environmental impact, making them a preferred choice for wire drawing operations worldwide.Furthermore, {} offers a range of value-added services to support its customers in optimizing the performance of its carbide wire drawing dies. This includes die maintenance and refurbishment, die design consulting, and technical support to troubleshoot any challenges in the wire drawing process. By providing comprehensive solutions, the company aims to ensure the long-term success of its customers and their wire drawing operations.As the demand for high-quality wire products continues to rise in various industries, the importance of reliable and efficient wire drawing processes cannot be overstated. With carbide wire drawing dies from {}, manufacturers can achieve the precision, consistency, and durability needed to meet the stringent requirements of modern wire applications.In conclusion, carbide wire drawing dies have revolutionized the wire drawing industry, offering superior performance, longevity, and cost-effectiveness. With its commitment to quality, innovation, and customer satisfaction, {} has positioned itself as a leading provider of carbide wire drawing dies, empowering businesses to excel in their wire drawing operations and stay ahead in the competitive market.
Top-Notch Tungsten Carbide Roll Rings: A Game-Changer in Industrial Applications
Tungsten Carbide Roll Rings Maximize Performance and Productivity in Steel MillsSteel mills are highly competitive and demanding environments that require the highest standards of performance and efficiency. One of the key components that determine the success of a steel mill is the quality of its rolls, which are essential for achieving precise, consistent, and reliable results. This is where tungsten carbide roll rings come into play, providing a superior solution for maximizing performance and productivity in steel rolling processes.Tungsten carbide roll rings are made of a highly durable and wear-resistant material that can withstand extreme temperatures, pressures, and stresses. They are designed to deliver exceptional strength, hardness, and toughness, making them ideal for use in demanding applications that require high precision and accuracy. These benefits are especially important for steel mills, which rely heavily on rolls to shape and refine their products.At the same time, tungsten carbide roll rings offer a number of advantages over other materials used in roll manufacturing. For example, they provide superior resistance to wear, corrosion, and deformation, which can prolong the lifespan of the rolls and reduce maintenance and replacement costs. They also offer high levels of accuracy, repeatability, and consistency, which are essential for ensuring product quality and consistency.In addition, tungsten carbide roll rings are highly versatile and can be customized to meet the specific needs of different steel rolling processes. They can be designed in various shapes, sizes, and configurations, depending on the type of steel being processed, the rolling speeds and forces involved, and other factors. This flexibility allows steel mills to optimize their operations and achieve the best results possible.To meet these demands, the leading manufacturer of tungsten carbide roll rings has developed innovative solutions that combine advanced materials, engineering, and manufacturing expertise. With over 20 years of experience in the industry, the company has established itself as a trusted and reliable supplier of roll rings to steel mills around the world.The company's tungsten carbide roll rings are produced using a sophisticated process that ensures consistent quality and performance. The rolls are made of high-purity tungsten carbide powders, which are blended with other materials to achieve the desired properties. The mixture is then compacted under high pressure, sintered at high temperatures, and machined to the required dimensions. The result is a high-quality roll ring that meets the most demanding specifications.To guarantee the performance and durability of its roll rings, the company uses advanced testing and inspection methods. These include hardness testing, microstructure analysis, dimensional measurement, and visual inspection. The rigorous quality control procedures ensure that each roll ring meets the highest standards of quality and reliability.Moreover, the company provides comprehensive support services to its customers, including on-site installation, training, and maintenance. This ensures that steel mills can maximize the benefits of tungsten carbide roll rings and achieve the best results possible. With its commitment to innovation, quality, and customer satisfaction, the company has become a preferred supplier of roll rings to steel mills worldwide.In conclusion, tungsten carbide roll rings have become a critical component in the steel industry, providing exceptional performance, durability, and versatility. With the support of a leading supplier of tungsten carbide roll rings, steel mills can optimize their operations and achieve the highest levels of productivity and efficiency. As the steel industry continues to evolve, tungsten carbide roll rings will play an increasingly important role in shaping its future.
Discover the Benefits of Coldheading in Manufacturing Processes
Coldheading is a crucial process in the manufacturing industry that is used to form metal parts. This process involves shaping a metal blank at room temperature using high pressure and force to create a desired shape. Coldheading can be done using many different methods, such as extruding, upsetting, and coining.One company that has been leading the way in the coldheading industry is {}. They specialize in providing coldheading solutions for a wide range of industries, including automotive, aerospace, and construction. With state-of-the-art equipment and a team of experienced professionals, they are able to produce high-quality coldheaded parts that meet the strictest industry standards.The process of coldheading begins with the selection of a metal blank, typically made from materials such as steel, aluminum, or brass. The blank is then placed into a coldheading machine, where it is subjected to extreme pressure and force. As the metal is forced into a die, it takes on the shape of the die, resulting in a coldheaded part with precise dimensions and a smooth finish.Coldheading is a highly efficient process that allows for the production of complex parts with minimal material waste. This makes it an ideal solution for the mass production of components such as bolts, screws, and rivets. The coldheading process also results in parts with improved mechanical properties, such as increased strength and durability.In addition to coldheading, {} also offers a range of secondary operations to further enhance the quality and functionality of coldheaded parts. These operations may include heat treatment, plating, and machining, to name a few. This comprehensive approach allows {} to deliver fully finished parts that are ready for use in a variety of applications.With a commitment to innovation and continuous improvement, {} continues to invest in the latest technology and equipment to stay at the forefront of the coldheading industry. Their dedication to quality and precision has earned them a reputation as a reliable partner for businesses seeking coldheaded parts of the highest caliber.One of the key advantages of partnering with {} is their ability to provide customized coldheading solutions to meet the unique needs of their clients. Whether it's a specific material requirement, a complex part design, or a tight production schedule, {} has the expertise and resources to deliver tailored solutions that exceed expectations.In conclusion, coldheading is a critical process in the manufacturing industry that plays a vital role in shaping metal parts for various applications. {} has established itself as a leader in the coldheading industry, offering a comprehensive range of solutions for businesses in diverse sectors. With their commitment to quality, innovation, and customer satisfaction, {} continues to set the standard for excellence in coldheading.
High-Quality Tungsten Carbide Bushing Dies: A Must-Have for Precision Machining
Tungsten Carbide Bushing Die, a critical component used in various industrial applications, is an essential part of the manufacturing process for a wide range of products. These bushing dies are known for their high strength, toughness, and resistance to wear, making them an ideal choice for demanding applications. One company that has been at the forefront of producing high-quality Tungsten Carbide Bushing Dies is {Company Name}. With years of experience and a strong commitment to innovation and quality, {Company Name} has established itself as a leader in the industry.{Company Name} was founded in {year} and has since grown to become a trusted name in the manufacturing of Tungsten Carbide Bushing Dies and other precision components. The company's state-of-the-art manufacturing facilities are equipped with the latest technologies and machinery, allowing them to produce high-precision components with tight tolerances and exceptional surface finishes.One of the key factors that set {Company Name} apart from its competitors is its focus on continuous research and development. The company invests heavily in R&D to explore new materials, manufacturing techniques, and designs that can further enhance the performance and durability of their products. This relentless pursuit of innovation has allowed {Company Name} to stay ahead of the curve and consistently deliver cutting-edge solutions to its customers.In addition to their commitment to innovation, {Company Name} also places a strong emphasis on quality control. Every Tungsten Carbide Bushing Die that rolls out of their production line undergoes rigorous testing to ensure that it meets the highest standards of quality and performance. This dedication to quality has earned {Company Name} a reputation for reliability and consistency, making them the go-to choice for many industrial manufacturers.Another key strength of {Company Name} is its team of highly skilled and experienced engineers and technicians. These professionals bring a wealth of knowledge and expertise to the table, allowing {Company Name} to tackle even the most complex engineering challenges with confidence. Whether it's customizing a bushing die to meet specific customer requirements or developing new solutions for emerging industry needs, the team at {Company Name} is always up to the task.Aside from their technical capabilities, {Company Name} is also known for its exceptional customer service. The company takes pride in building strong, long-lasting relationships with its clients, working closely with them to understand their needs and provide tailored solutions that address their unique requirements. This customer-centric approach has earned {Company Name} the trust and loyalty of many satisfied clients, cementing its position as a preferred partner in the industry.Looking ahead, {Company Name} remains committed to pushing the boundaries of what is possible in the field of Tungsten Carbide Bushing Dies and precision components. The company continues to explore new opportunities for growth and expansion, with a keen eye on emerging trends and technologies. Whether it's delving into new markets, expanding their product lineup, or further refining their manufacturing processes, {Company Name} is poised to lead the way forward.In conclusion, Tungsten Carbide Bushing Dies are a critical component in many industrial applications, and {Company Name} has emerged as a leading producer of these precision components. With a strong focus on innovation, quality, and customer satisfaction, {Company Name} has established itself as a trusted partner for many manufacturers. As the company continues to evolve and expand its capabilities, it is well-positioned to shape the future of the industry and meet the evolving needs of its clients.
High-Quality Cold Forging Nut Die for Efficient Manufacturing
Carbide Cold Forging Nut Die Revolutionizes Manufacturing IndustryIn the world of manufacturing, innovation is key to staying ahead of the game. One company that is pushing the boundaries of what is possible in the manufacturing industry is [Company Name]. Their latest innovation, the Carbide Cold Forging Nut Die, is set to revolutionize the way nuts are produced.The Carbide Cold Forging Nut Die is a game changer for the manufacturing industry. It is a die made from carbide, a durable and tough material that is perfect for withstanding the high pressures and temperatures involved in cold forging. This die is designed to be used in cold forging machines to produce nuts that are of the highest quality.Cold forging is the process of shaping metal using extremely high pressures without the need for extreme heat. This process produces parts that are stronger and have a better surface finish than parts made using traditional manufacturing methods. The Carbide Cold Forging Nut Die takes this process to the next level, producing nuts that are not only of the highest quality, but also more cost-effective to produce.[Company Name] has been a leader in the manufacturing industry for over 30 years. They have a reputation for pushing the boundaries of what is possible in manufacturing and for producing high-quality, innovative products for their customers. The Carbide Cold Forging Nut Die is just the latest example of their commitment to innovation and excellence in manufacturing.The company's team of engineers and designers worked tirelessly to develop the Carbide Cold Forging Nut Die. They drew on their years of experience in the industry and their extensive knowledge of materials and manufacturing processes to create a die that is truly revolutionary. The result is a product that is durable, efficient, and precise, and that is already generating a lot of interest from manufacturers around the world.One of the key benefits of the Carbide Cold Forging Nut Die is its durability. Unlike traditional dies, which can wear out quickly under the extreme pressures and temperatures involved in cold forging, the Carbide Cold Forging Nut Die is designed to last for much longer. This means that manufacturers can produce more nuts before needing to replace the die, saving time and money in the long run.Another benefit of the Carbide Cold Forging Nut Die is its precision. The die is designed to produce nuts that are uniform in size and shape, with a perfect surface finish every time. This level of precision is difficult to achieve with traditional manufacturing methods, making the Carbide Cold Forging Nut Die a game changer for manufacturers who require the highest quality nuts for their products.The Carbide Cold Forging Nut Die is also designed to be more cost-effective than traditional dies. Because it is more durable and produces higher quality nuts, manufacturers can save money on production costs over time. This is an important consideration for manufacturers who are always looking for ways to improve their bottom line.Overall, the Carbide Cold Forging Nut Die is set to revolutionize the manufacturing industry. Its durability, precision, and cost-effectiveness make it an attractive option for manufacturers around the world. With its latest innovation, [Company Name] continues to solidify its position as a leader in the manufacturing industry, and as a company that is always looking for new ways to push the boundaries of what is possible in manufacturing.