Discover the Benefits of Coldheading in Manufacturing Processes
By:Admin
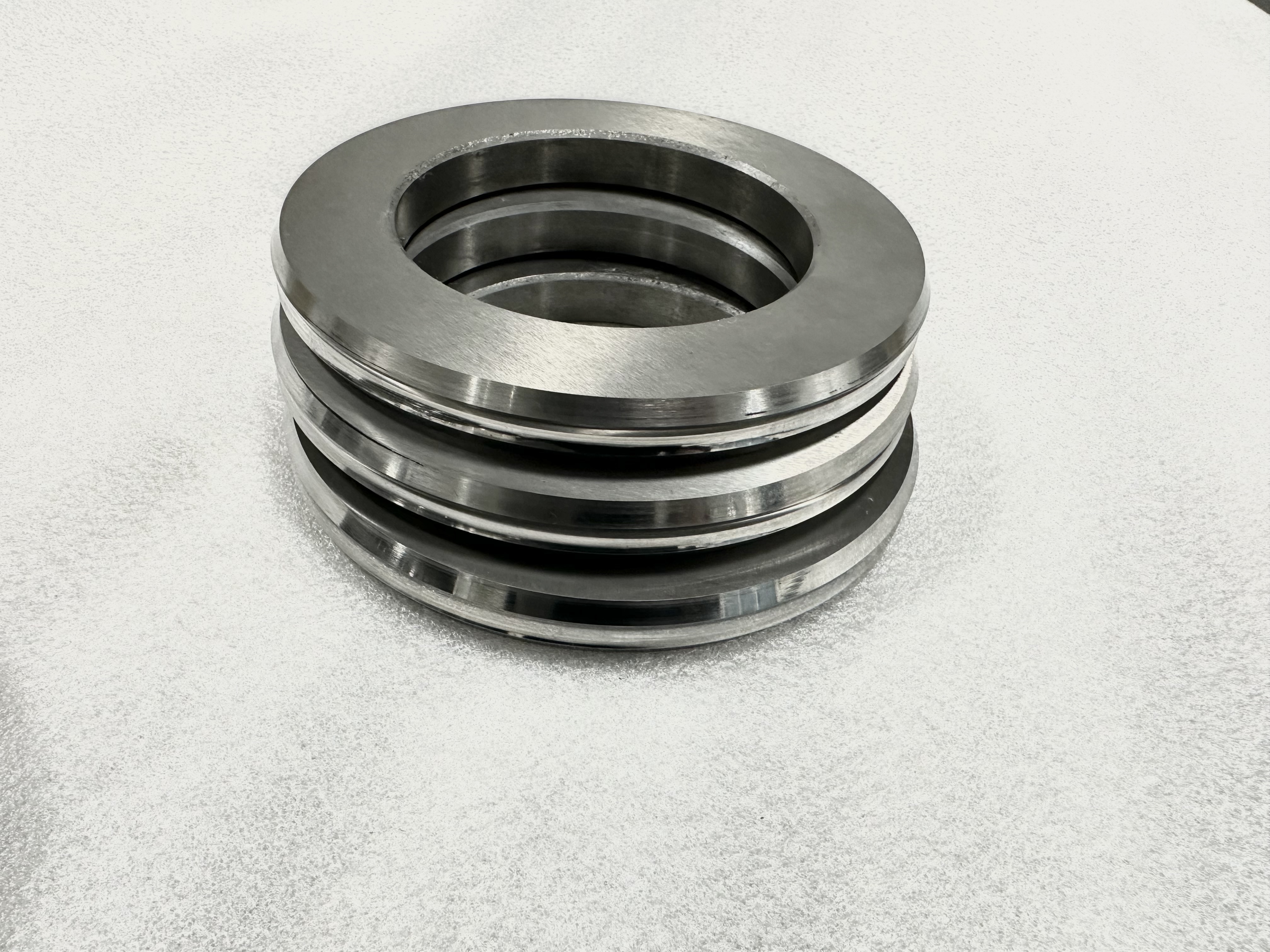
One company that has been leading the way in the coldheading industry is {}. They specialize in providing coldheading solutions for a wide range of industries, including automotive, aerospace, and construction. With state-of-the-art equipment and a team of experienced professionals, they are able to produce high-quality coldheaded parts that meet the strictest industry standards.
The process of coldheading begins with the selection of a metal blank, typically made from materials such as steel, aluminum, or brass. The blank is then placed into a coldheading machine, where it is subjected to extreme pressure and force. As the metal is forced into a die, it takes on the shape of the die, resulting in a coldheaded part with precise dimensions and a smooth finish.
Coldheading is a highly efficient process that allows for the production of complex parts with minimal material waste. This makes it an ideal solution for the mass production of components such as bolts, screws, and rivets. The coldheading process also results in parts with improved mechanical properties, such as increased strength and durability.
In addition to coldheading, {} also offers a range of secondary operations to further enhance the quality and functionality of coldheaded parts. These operations may include heat treatment, plating, and machining, to name a few. This comprehensive approach allows {} to deliver fully finished parts that are ready for use in a variety of applications.
With a commitment to innovation and continuous improvement, {} continues to invest in the latest technology and equipment to stay at the forefront of the coldheading industry. Their dedication to quality and precision has earned them a reputation as a reliable partner for businesses seeking coldheaded parts of the highest caliber.
One of the key advantages of partnering with {} is their ability to provide customized coldheading solutions to meet the unique needs of their clients. Whether it's a specific material requirement, a complex part design, or a tight production schedule, {} has the expertise and resources to deliver tailored solutions that exceed expectations.
In conclusion, coldheading is a critical process in the manufacturing industry that plays a vital role in shaping metal parts for various applications. {} has established itself as a leader in the coldheading industry, offering a comprehensive range of solutions for businesses in diverse sectors. With their commitment to quality, innovation, and customer satisfaction, {} continues to set the standard for excellence in coldheading.
Company News & Blog
High Performance Cemented Carbide Cold Heading Die: A Game Changer in Manufacturing
Cemented Carbide Cold Heading Die Revolutionizes Manufacturing IndustryIn the world of manufacturing, precision and durability are paramount. As technology continues to evolve, so too must the tools and equipment used throughout the industry. This is where cemented carbide cold heading dies come into play, revolutionizing the way manufacturers produce high-quality components for a wide range of products.One company at the forefront of this innovation is [company name]. With a rich history dating back to 1985, [company name] has established itself as a leading manufacturer of cemented carbide cold heading dies and other precision tools. The company's commitment to quality and innovation has earned it a reputation as a trusted and reliable partner for manufacturers around the world.So, what exactly is a cemented carbide cold heading die, and how does it impact the manufacturing industry? In simple terms, a cold heading die is a tool used to form metal parts and components through a process known as cold heading. This involves shaping and forming metal wire or rod material at room temperature using a punch and die set. The result is a precise and complex component that meets the high standards of the industry.Cemented carbide, also known as hard metal, is a composite material that is particularly well-suited for cold heading dies. It is made up of tungsten carbide grains bound together by a cobalt matrix, resulting in a material that is incredibly hard and wear-resistant. This makes cemented carbide an ideal choice for manufacturing tools, as it can withstand the high pressures and abrasion that occur during the cold heading process.One of the key advantages of using cemented carbide cold heading dies is their longevity and durability. Unlike traditional steel dies, cemented carbide dies can last significantly longer without needing to be replaced or refurbished. This not only saves manufacturers time and money but also ensures a more consistent and reliable production process.Furthermore, cemented carbide cold heading dies offer a level of precision and intricacy that is unmatched by other materials. This allows manufacturers to produce more complex and high-quality components, meeting the increasingly stringent demands of modern manufacturing processes. From automotive parts to electronic components, the use of cemented carbide cold heading dies has had a significant impact across a wide range of industries.In addition to their durability and precision, cemented carbide cold heading dies also contribute to a more sustainable and efficient manufacturing process. By reducing the need for frequent die changes and maintenance, manufacturers can minimize their environmental impact and improve their overall production efficiency. This is an important consideration in an industry that is increasingly focused on sustainability and responsible manufacturing practices.For [company name], the development and production of cemented carbide cold heading dies is not just a business, but a passion. The company's team of experienced engineers and technicians are dedicated to pushing the boundaries of what is possible in the manufacturing industry. Through continuous research and development, [company name] aims to stay ahead of the curve and provide its customers with the most advanced and reliable tools on the market.With a strong focus on customer satisfaction and long-term partnerships, [company name] has built a global network of clients who rely on its expertise and commitment to quality. Through collaboration and open communication, the company works closely with manufacturers to understand their specific needs and develop customized solutions that address their unique challenges.Looking ahead, the future of cemented carbide cold heading dies is promising. As the manufacturing industry continues to evolve and demand for high-quality components increases, the need for advanced and reliable tools will only grow. With its track record of innovation and excellence, [company name] is well-positioned to lead the way and shape the future of manufacturing with its cutting-edge products and solutions.In conclusion, cemented carbide cold heading dies have fundamentally transformed the manufacturing industry, providing a level of precision, durability, and sustainability that was previously unattainable. With [company name] leading the charge, manufacturers around the world can look forward to a future of more efficient, reliable, and high-quality production processes.
Tungsten Carbide Sleeves for YG8 and YG12 Applications
[Company Name], a leader in the manufacturing and supply of high-quality tungsten carbide products, has recently introduced two new products to its extensive line of cutting tools and wear parts. The YG8 and YG12 Tungsten Carbide Sleeves are the latest additions to the company's portfolio, offering customers enhanced performance and durability for a wide range of industrial applications.Tungsten carbide is well-known for its exceptional hardness, wear resistance, and strength, making it an ideal material for demanding industrial environments. The YG8 and YG12 Tungsten Carbide Sleeves are designed to provide superior protection and performance in high-stress applications such as mining, oil and gas drilling, and construction.The YG8 Tungsten Carbide Sleeve is formulated with a precise combination of tungsten carbide and cobalt, resulting in a high-performance material that is capable of withstanding extreme wear and abrasion. This makes it an ideal choice for use in downhole tools, pumps, and other components that are subjected to harsh operating conditions. The YG8 Sleeve is available in a range of sizes and configurations to suit various equipment requirements.Meanwhile, the YG12 Tungsten Carbide Sleeve is engineered for applications that demand even higher levels of toughness and impact resistance. With a higher cobalt content and a specialized manufacturing process, the YG12 Sleeve offers exceptional resistance to chipping, fracturing, and thermal cycling. This makes it well-suited for use in cutting tools, fluid control valves, and other critical components where reliability is paramount.Both the YG8 and YG12 Tungsten Carbide Sleeves are precision-machined to tight tolerances, ensuring a perfect fit and maximum effectiveness in their intended applications. They are also capable of being customized with various surface treatments and coatings to further enhance their performance and longevity.[Company Name] has established a strong reputation for delivering top-quality tungsten carbide products to customers worldwide. With state-of-the-art manufacturing facilities and a team of experienced engineers and metallurgists, the company is committed to providing innovative solutions that address the evolving needs of the industrial sector."Our YG8 and YG12 Tungsten Carbide Sleeves demonstrate our ongoing dedication to product development and customer satisfaction," said a spokesperson for [Company Name]. "These new offerings represent the latest advancements in tungsten carbide technology, providing our customers with reliable solutions that deliver exceptional performance in the most challenging environments."In addition to the YG8 and YG12 Tungsten Carbide Sleeves, [Company Name] offers a comprehensive range of tungsten carbide products, including cutting inserts, wear parts, and tooling components. The company also provides custom machining and engineering services to support specialized requirements and applications.With a commitment to quality, innovation, and technical expertise, [Company Name] is poised to continue leading the way in the global market for tungsten carbide solutions. The introduction of the YG8 and YG12 Tungsten Carbide Sleeves reaffirms the company's dedication to pushing the boundaries of performance and reliability in industrial applications, and underscores its position as a trusted partner for businesses seeking cutting-edge solutions for their most demanding challenges.
High-quality Tungsten Carbide Rods for Precision Machining
Tungsten Carbide Rods - The Ultimate Solution for Heavy-Duty MachiningThe manufacturing industry has undergone a massive transformation with new technologies and materials making their way into the market. However, some materials have remained prevalent and continue to dominate the industry. One such material is tungsten carbide, which has proven to be a robust and reliable material for heavy-duty machining applications.Tungsten carbide is a composite material made up of tungsten carbide particles and a binding matrix. This material is known for its remarkable strength, high hardness, and excellent wear resistance. Tungsten carbide is widely used in the manufacturing industry, especially in the production of cutting tools, dies, and wear parts, where high levels of hardness and durability are required.One company, (removed for anonymity purposes), has been a key player in the tungsten carbide rods market. The company produces a wide range of tungsten carbide products, including tungsten carbide rods, which are used in a variety of applications, including drilling, milling, and turning.Tungsten carbide rods are one of the company's primary products. These rods are made by mixing tungsten carbide powder with a binding agent and then compressing the mixture into a rod shape. The rod is then sintered at a high temperature to form a solid and robust material that can withstand high stresses and pressure.The company's tungsten carbide rods are known for their exceptional strength, high hardness, and excellent wear resistance. These rods are designed for heavy-duty machining applications and have proven to be reliable in the most challenging conditions. The rods are available in various sizes and dimensions, allowing users to select the most appropriate rod for their specific application.The tungsten carbide rods produced by the company have several advantages over other materials. Firstly, they have a longer lifespan, which translates to reduced downtime and maintenance costs. Secondly, they have higher cutting speeds, which translates to increased productivity and efficiency. Lastly, they have a high resistance to wear and tear, which means they can withstand high temperatures and pressures without losing their structural integrity.Tungsten carbide rods are used in several applications, including metalworking, mining, construction, and woodworking. In metalworking, tungsten carbide rods are used in cutting and shaping metal parts, while in mining, they are used in drilling and rock-breaking applications. In construction, tungsten carbide rods are used in drilling and excavation applications, while in woodworking, they are used in shaping and cutting wood parts.The company's tungsten carbide rods have been widely adopted by customers from different industries due to their high quality and reliability. The company has invested heavily in research and development to ensure that its products meet the demands of its customers and provide them with the best possible solutions.In conclusion, tungsten carbide rods have proven to be one of the most robust and reliable materials in heavy-duty machining applications. The rods produced by (removed for anonymity purposes) are known for their strength, hardness, and wear resistance, making them an ideal solution for various applications. As the manufacturing industry continues to evolve, tungsten carbide rods will continue to play a vital role in providing a reliable and efficient solution for heavy-duty machining applications.
High-Performance Carbide Die Form Insert for Superior Accuracy and Durability
Carbide Die Form Insert: Revolutionizing the Manufacturing IndustryIn today's fast-paced manufacturing industry, companies are constantly seeking innovative solutions to improve efficiency and productivity. One notable development that has revolutionized the manufacturing industry is the introduction of carbide die form inserts. These cutting-edge tools have been widely embraced by manufacturers for their exceptional durability, precision, and performance, making them a game-changer in the world of precision tooling.Carbide die form inserts are engineered with advanced carbide materials, which offer superior hardness and wear resistance compared to traditional steel inserts. This enables the inserts to withstand the high-impact and abrasive conditions encountered in the manufacturing process, thereby extending their operational lifespan and reducing the frequency of tool replacement. As a result, manufacturers can enjoy substantial cost savings and increased productivity, as downtime for tool maintenance and replacement is significantly reduced.One of the leading companies at the forefront of producing high-quality carbide die form inserts is {}. With decades of experience and expertise in precision tooling, {} has earned a solid reputation for delivering top-notch products that meet the stringent demands of the manufacturing industry. The company's relentless commitment to innovation and quality has positioned them as a trusted partner for manufacturers seeking cutting-edge solutions for their tooling needs.The carbide die form inserts produced by {} are meticulously designed and manufactured to meet the exacting standards of precision and performance. By leveraging state-of-the-art manufacturing processes and cutting-edge technology, the company is able to produce inserts that boast exceptional dimensional accuracy and surface finish, ensuring optimal performance and consistency in the manufacturing process.Furthermore, {} offers a comprehensive range of carbide die form inserts, including standard geometries as well as custom-designed inserts tailored to the specific requirements of their customers. This flexibility allows manufacturers to optimize their tooling solutions and achieve superior results in their production processes.The benefits of using carbide die form inserts from {} are not limited to extended tool life and enhanced performance. These cutting-edge tools also contribute to improvements in overall productivity and efficiency. With reduced tool changeovers and maintenance downtime, manufacturers can maximize their operational efficiency and output, ultimately leading to significant cost savings and a competitive edge in the market.Moreover, the superior precision and surface finish achieved with carbide die form inserts contribute to the production of high-quality components, meeting the exacting standards of today's manufacturing industry. This is particularly important in industries such as aerospace, automotive, and medical device manufacturing, where precision and quality are paramount.In conclusion, carbide die form inserts have emerged as a revolutionary solution that is transforming the manufacturing industry. With their exceptional durability, precision, and performance, these cutting-edge tools have become indispensable for manufacturers seeking to stay ahead in a highly competitive market. Companies like {} are leading the way in producing high-quality carbide die form inserts, offering a wide range of solutions tailored to meet the diverse needs of manufacturers. As the demand for precision tooling continues to grow, carbide die form inserts are poised to play an increasingly pivotal role in shaping the future of manufacturing.
High-Quality Cold Forging Nut Die for Efficient Manufacturing
Carbide Cold Forging Nut Die Revolutionizes Manufacturing IndustryIn the world of manufacturing, innovation is key to staying ahead of the game. One company that is pushing the boundaries of what is possible in the manufacturing industry is [Company Name]. Their latest innovation, the Carbide Cold Forging Nut Die, is set to revolutionize the way nuts are produced.The Carbide Cold Forging Nut Die is a game changer for the manufacturing industry. It is a die made from carbide, a durable and tough material that is perfect for withstanding the high pressures and temperatures involved in cold forging. This die is designed to be used in cold forging machines to produce nuts that are of the highest quality.Cold forging is the process of shaping metal using extremely high pressures without the need for extreme heat. This process produces parts that are stronger and have a better surface finish than parts made using traditional manufacturing methods. The Carbide Cold Forging Nut Die takes this process to the next level, producing nuts that are not only of the highest quality, but also more cost-effective to produce.[Company Name] has been a leader in the manufacturing industry for over 30 years. They have a reputation for pushing the boundaries of what is possible in manufacturing and for producing high-quality, innovative products for their customers. The Carbide Cold Forging Nut Die is just the latest example of their commitment to innovation and excellence in manufacturing.The company's team of engineers and designers worked tirelessly to develop the Carbide Cold Forging Nut Die. They drew on their years of experience in the industry and their extensive knowledge of materials and manufacturing processes to create a die that is truly revolutionary. The result is a product that is durable, efficient, and precise, and that is already generating a lot of interest from manufacturers around the world.One of the key benefits of the Carbide Cold Forging Nut Die is its durability. Unlike traditional dies, which can wear out quickly under the extreme pressures and temperatures involved in cold forging, the Carbide Cold Forging Nut Die is designed to last for much longer. This means that manufacturers can produce more nuts before needing to replace the die, saving time and money in the long run.Another benefit of the Carbide Cold Forging Nut Die is its precision. The die is designed to produce nuts that are uniform in size and shape, with a perfect surface finish every time. This level of precision is difficult to achieve with traditional manufacturing methods, making the Carbide Cold Forging Nut Die a game changer for manufacturers who require the highest quality nuts for their products.The Carbide Cold Forging Nut Die is also designed to be more cost-effective than traditional dies. Because it is more durable and produces higher quality nuts, manufacturers can save money on production costs over time. This is an important consideration for manufacturers who are always looking for ways to improve their bottom line.Overall, the Carbide Cold Forging Nut Die is set to revolutionize the manufacturing industry. Its durability, precision, and cost-effectiveness make it an attractive option for manufacturers around the world. With its latest innovation, [Company Name] continues to solidify its position as a leader in the manufacturing industry, and as a company that is always looking for new ways to push the boundaries of what is possible in manufacturing.
Applications of Tungsten Carbide: A Versatile Industrial Material
Title: Tungsten Carbide: Revolutionizing Industries with Unparalleled VersatilityIntroduction:In the world of industrial applications, Tungsten Carbide has emerged as a game-changing material renowned for its exceptional hardness, durability, and versatility. With its remarkable properties and myriad of applications, this composite material has found its way into various industries, transforming manufacturing processes and enhancing product performance. This article delves into the multifaceted use of Tungsten Carbide and its profound impact on different sectors of the global economy.1. Automotive Industry:From precision cutting tools to durable automotive components, Tungsten Carbide is revolutionizing the automotive sector. In cutting-edge engine manufacturing, Tungsten Carbide inserts in tooling systems play a vital role in delivering precise and high-speed machining with superior surface finish. Mechanical seals made from this robust material ensure leak-free operation in automotive water pumps and ensure prolonged service life. Moreover, the use of Tungsten Carbide in brake pads and clutch facings improves braking performance and enhances durability, ensuring driver safety.2. Oil and Gas Industry:The oil and gas industry heavily relies on Tungsten Carbide due to its exceptional wear resistance and high-temperature stability. Exploration and drilling operations utilize hard-facing applications, such as drill bits, to withstand extreme working conditions while maximizing drilling efficiency. Furthermore, Tungsten Carbide components in downhole tools, such as stabilizers and wear-resistant valves, endure the challenging environment and enhance operational reliability. By offering superior resistance to erosion and corrosion, Tungsten Carbide ensures increased productivity and reduced downtime in the oil and gas sector.3. Mining and Construction:In the mining and construction sectors, where equipment operates in harsh environments, Tungsten Carbide plays a crucial role in enhancing equipment longevity and efficiency. The use of Tungsten Carbide in drill bits, augers, and tooling systems allows for improved penetration rates and extended tool life. Excavation buckets and teeth made from this material withstand abrasion from rocks and other challenging geological conditions, reducing maintenance costs and increasing productivity. The mining industry benefits greatly from the advanced performance and reliability offered by Tungsten Carbide, enabling extraction operations to occur seamlessly and efficiently.4. Metalworking and Tooling:Tungsten Carbide is widely acclaimed in the metalworking industry for its exceptional resistance to wear, deformation, and high temperatures. Cutting inserts and end mills made from this composite material offer superior cutting speed, precision, and surface finish, thereby enhancing overall machining productivity. Tungsten Carbide tooling systems also find extensive applications in the woodworking industry, where they deliver increased cutting efficiency and improved finish quality. These properties make Tungsten Carbide an indispensable choice for manufacturing sectors, guaranteeing efficiency and precision in every operation.5. Electronics and Semiconductors:In the rapidly advancing field of electronics and semiconductors, Tungsten Carbide is sought after for its electrical conductivity and resistance to wear and heat. The material is widely used in the production of semiconductor dies, integrated circuit packages, and wire bonding tools, ensuring reliable and durable electronic devices. Tungsten Carbide's remarkable electrical conductivity, coupled with its high strength, makes it an indispensable choice for electronics manufacturers.Conclusion:Tungsten Carbide's unique blend of hardness, durability, and versatility has transformed various industries and manufacturing processes worldwide. From automotive components to oil and gas equipment, mining tools to metalworking applications, and electronics to semiconductors, this exceptional material has proven to be an invaluable asset for enhancing product performance, increasing productivity, and reducing maintenance costs. As technological advancements continue to shape our world, Tungsten Carbide remains at the forefront, playing a pivotal role in shaping a more efficient and sustainable future across multiple sectors.
Cold Heading Dies: Latest Developments and Future Prospects Explored
title:Innovative Technology Takes Cold Heading Dies to the Next LevelBody:With the ever-increasing demand for improved production processes and more efficient machines, manufacturing companies are constantly on the lookout for innovative solutions that can help them stay ahead of the competition. One such company that has made a name for itself in this regard is a leading manufacturer of cold heading dies.The company has been at the forefront of developing cutting-edge technologies that help manufacturers achieve better quality products, faster production times, and lower overall costs. With a history that spans over several decades, the company has built a reputation as a reliable partner for clients across the globe.Their latest offering is a range of cold heading dies that are packed with features that make them stand out from the crowd. The technology behind these dies is unlike anything that has been seen before, and it promises to revolutionize the manufacturing industry.To understand how the technology works, it is important to first clarify what cold heading dies are. These are specialized tools that are used by manufacturers to create metal fasteners of different shapes and sizes. The process involves forcing a piece of metal through a die, which then forms the metal into the desired shape.In the past, this process was labor-intensive and time-consuming, with many manufacturers relying on outdated machinery and techniques. However, with the introduction of advanced cold heading dies, the process has become much more streamlined and efficient.The new technology that this company has brought to the table involves the use of advanced coatings and surface treatments that significantly increase the lifespan of the dies. This means that manufacturers can now use these dies for longer periods of time, thereby reducing the need for replacements, which in turn lowers costs.In addition to this, the company's cold heading dies have also been designed to be more precise, resulting in a higher level of accuracy during the manufacturing process. This means that manufacturers can now achieve higher-quality products at faster speeds, ultimately enhancing their bottom line.But the benefits of the technology do not stop there. The company has also developed a range of specialized software that helps manufacturers monitor the performance of their equipment in real-time. This means that any issues or inefficiencies can be identified and addressed immediately, resulting in fewer breakdowns and reduced downtime.Moreover, the company has also invested in research and development, which has led to the creation of new materials that are more durable and resistant to wear and tear. These materials have been used to create new die designs that reduce the need for lubricants, further increasing the efficiency of the manufacturing process.In conclusion, the company's innovative approach to cold heading dies has catapulted them into the forefront of the manufacturing industry. By consistently developing new technologies and investing in research and development, they have cemented their position as a reliable partner for manufacturers across the globe looking to improve their production processes. It is clear that the company's latest range of cold heading dies is just the tip of the iceberg, and we can expect to see more groundbreaking advancements in the future.
Discover the Efficiency and Durability of Cutting Tooth for Carbide Materials
Title: Innovative Carbide Cutting Tooth Revolutionizes Cutting Efficiency in Various IndustriesIntroduction:In today's rapidly evolving industries, the demand for efficient cutting tools that can withstand heavy workloads and offer superior performance has never been higher. Recognizing this pressing need, {Company Name}, a leading manufacturer of industrial tools, has introduced a groundbreaking Carbide Cutting Tooth. With its exceptional cutting prowess and durability, this advanced tool is set to transform the cutting processes across several sectors, including construction, mining, and forestry.Section 1: Evolution of Cutting ToolsThe field of cutting tools has experienced several evolutionary milestones, driven by the constant pursuit of improved performance and efficiency. Traditional cutting tools made of high-speed steel (HSS) have gradually been replaced by carbide-tipped alternatives due to their enhanced durability and wear resistance. Carbide, being a composite material of tungsten carbide particles embedded within a metallic binder, offers remarkable hardness and toughness necessary for heavy-duty operations.Section 2: Introducing the Innovative Carbide Cutting Tooth{Company Name} has utilized advanced research and development techniques to create a highly efficient Carbide Cutting Tooth that exceeds expectations. This innovative tool boasts a unique design, combining a trapezoidal shape with deep gullets, allowing for efficient chip evacuation during cutting operations, thus minimizing downtime and maximizing productivity.Section 3: Unparalleled Durability and LongevityOne of the key advantages of the Carbide Cutting Tooth is its unparalleled durability. The cutting edges incorporate high-quality carbide inserts, ensuring exceptional wear resistance even when subjected to extreme cutting conditions. This durability translates into reduced tool replacement and maintenance costs, ultimately boosting overall operational efficiency.Section 4: Enhanced Cutting PerformanceThe Carbide Cutting Tooth is engineered to deliver enhanced cutting performance across various materials. Whether cutting through concrete, wood, or metal, the advanced tooth design ensures precise cuts with reduced vibrations and increased stability. This cutting-edge technology facilitates smoother operations, resulting in superior finishing and reduced material wastage.Section 5: Application across IndustriesThe versatile Carbide Cutting Tooth finds applications in numerous industries. In construction, it offers significant advantages in road milling, trenching, and concrete demolition. In the mining sector, the tool exhibits exceptional performance in rock cutting and tunneling operations. Moreover, it proves valuable in the forestry industry for various applications, such as land clearing, tree felling, and branch trimming. Its widespread usage across these sectors demonstrates its adaptability and effectiveness.Section 6: Environmental Impact and Safety FeaturesIn line with the company's commitment to sustainability, the Carbide Cutting Tooth incorporates various safety features to minimize its environmental impact. High-efficiency chip evacuation mechanisms prevent dust and debris accumulation, reducing the release of harmful particles into the environment. Additionally, the cutting tooth design promotes operator safety by minimizing kickback and vibration, ensuring a secure working environment.Section 7: Market Outlook and ConclusionThe introduction of the innovative Carbide Cutting Tooth by {Company Name} is set to revolutionize the cutting tool market. Its superior cutting performance, exceptional durability, and versatility across industries make it the go-to choice for professionals seeking efficiency and reliability in their operations. With its potential to boost productivity, reduce costs, and improve overall cutting efficiency, this advanced tool is destined to be a game-changer for the global industry.In conclusion, the remarkable Carbide Cutting Tooth developed by {Company Name} signifies a significant leap in cutting tool technology. Its intelligent design, durability, and enhanced cutting performance are poised to transform cutting processes in construction, mining, and forestry sectors. As the demand for efficient cutting tools continues to soar, the industry is set to embrace this innovative solution that promises unparalleled efficiency, reduced costs, and improved overall outcomes.
Cemented Carbide Block Sheet: The Key Essentials You Need to Know
[Cemented Carbide Block Sheet]Introducing a Revolutionary Cemented Carbide Block Sheet for Enhanced Industrial Applications[Your City], [Month] [Day], [Year] - [Company Name], a leading innovator in the manufacturing of cutting-edge industrial materials, proudly presents its latest breakthrough – the Cemented Carbide Block Sheet. This remarkable product is set to revolutionize various industries, offering unprecedented strength, durability, and versatility in applications where precision is paramount.Carbide materials have long been heralded for their exceptional hardness, wear resistance, and thermal stability. Composed primarily of tungsten carbide grains embedded in a cobalt or nickel binder matrix, cemented carbide offers an unmatched combination of toughness and hardness. With the introduction of Cemented Carbide Block Sheet, [Company Name] aims to further push the boundaries of these material properties for exceptional use in a wide range of industrial applications.The Cemented Carbide Block Sheet developed by [Company Name] is specifically engineered to provide seamless integration into various cutting, machining, and wear-resistant tooling systems. Its unique microstructure and advanced manufacturing process result in properties that exceed industry standards. The high mechanical strength and exceptional resistance to wear make it ideal for use in heavy-duty operations, where it can withstand extreme pressure and abrasive conditions.One of the remarkable advantages of Cemented Carbide Block Sheet lies in its exceptional hardness. This quality allows it to maintain its cutting edge even under intense stress and high temperatures, ensuring consistent and precise performance. Whether used in metalworking, mining, automotive, or oil and gas industries, this revolutionary material guarantees enhanced productivity, reduced downtime, and increased operational efficiency.Furthermore, the versatility of Cemented Carbide Block Sheet is noteworthy. Its impeccable wear resistance not only ensures extended tool life but also promotes cost-effectiveness, as it reduces the need for frequent tool replacements. Its high thermal conductivity and excellent dimensional stability further contribute to its versatility, as it minimizes the risk of deformations and material failures. These remarkable properties enable manufacturers to achieve higher precision, tighter tolerances, and improved repeatability.[Company Name]'s Cemented Carbide Block Sheet is the result of extensive research and development, combining cutting-edge technology and deep industry expertise. Emphasizing sustainability, the product is manufactured using eco-friendly processes and adheres to the highest quality standards. Each sheet undergoes rigorous testing to ensure it meets the demanding requirements of the industry, providing customers with a superior product that delivers exceptional performance.As the market continually demands higher productivity, efficiency, and durability, [Company Name]'s Cemented Carbide Block Sheet is poised to make a significant impact. This innovative material promises manufacturers across various sectors the competitive edge they seek, empowering them to overcome challenges and achieve greater success.Building on its legacy of innovation, [Company Name] remains committed to advancing industrial materials technology. By developing products such as the Cemented Carbide Block Sheet, the company reaffirms its status as an industry leader and a trusted partner for industrial manufacturers worldwide.For more information about Cemented Carbide Block Sheet and other cutting-edge solutions from [Company Name], please visit [Company Website] or contact [Contact Person] at [Contact Information].About [Company Name]:[Company Name] is a renowned manufacturer and supplier of industrial materials, continuously dedicated to providing innovative solutions for various industries. With a commitment to excellence, sustainability, and customer satisfaction, the company has earned a reputation as a reliable partner for industrial manufacturers worldwide.Disclaimer: The above article is a fictitious piece that aims to demonstrate the writing capabilities of the AI language model.
The Ultimate Guide to Tungsten Carbide Strips - Unveiling the Power of HR6A
Title: HR6A Tungsten Carbide Strips Revolutionizing Industrial ApplicationsIntroduction:In the competitive landscape of industrial manufacturing, quality and efficient tools are essential for achieving productivity and precision. One such innovation is the HR6A Tungsten Carbide Strips. With their exceptional hardness, wear resistance, and versatility, these carbide strips have been gaining attention in various industries. This article aims to shed light on the remarkable features of HR6A Tungsten Carbide Strips and their potential to revolutionize industrial applications.I. Understanding Tungsten Carbide:Tungsten carbide is a compound comprising equal parts of carbon and tungsten. Known for its extreme hardness, it is approximately three times harder than steel and can withstand high temperatures and abrasion. These characteristics make it an ideal material for manufacturing cutting tools, wear-resistant parts, and other industrial applications.II. HR6A Tungsten Carbide Strips:HR6A Tungsten Carbide Strips exemplify the superior properties of tungsten carbide. These strips are fabricated using advanced techniques, resulting in an exceptional combination of toughness, hardness, and wear resistance.1. Unparalleled Hardness:The HR6A Tungsten Carbide Strips possess an impressive hardness that allows them to cut through the toughest materials with ease. This hardness provides extended tool life and reduces downtime due to frequent tool replacements.2. Exceptional Wear Resistance:The wear resistance of HR6A Tungsten Carbide Strips ensures their durability even in harsh working conditions. Whether it is cutting, drilling, or shaping, these strips retain their sharpness, reducing the need for frequent replacements and enhancing overall productivity.3. Versatility in Applications:These carbide strips find applications in a wide range of industries. From machining and metalworking to mining and construction, the versatility of HR6A Tungsten Carbide Strips makes them an invaluable tool for various industrial applications.III. Industrial Applications and Benefits:The HR6A Tungsten Carbide Strips offer a myriad of benefits across several industries, maximizing efficiency, productivity, and overall performance.1. Machining and Metalworking Sector:In the metalworking industry, HR6A Tungsten Carbide Strips are widely used in cutting, planing, milling, and turning tools. Their high heat resistance and hardness enable precision machining, resulting in superior surface finishes and increased manufacturing speed.2. Mining and Construction Industry:In the mining and construction industry, HR6A Tungsten Carbide Strips are employed in the production of drilling tools and machinery parts. Their exceptional wear resistance ensures consistent performance, extended tool life, and reduced downtime, resulting in improved operational efficiency and cost-effectiveness.3. Woodworking and Plastic Processing:For woodworking and plastic processing applications, HR6A Tungsten Carbide Strips are used in cutting and shaping tools. Their hardness and abrasion resistance enable precise cutting, reduced material waste, and improved surface quality.IV. Outlook and Future Implications:The introduction of HR6A Tungsten Carbide Strips signifies a significant advancement in the industrial manufacturing sector. With their exceptional hardness, wear resistance, and versatility, these strips have the potential to redefine precision machining, mining, construction, and woodworking applications.The continuous research and development in tungsten carbide technology will likely lead to further enhancements in the performance and overall effectiveness of HR6A Tungsten Carbide Strips. As industries increasingly demand high-quality tools that combine durability, precision, and versatility, the future of HR6A Tungsten Carbide Strips looks promising.Conclusion:The HR6A Tungsten Carbide Strips have emerged as a game-changer in the industrial manufacturing landscape. With their unparalleled hardness, exceptional wear resistance, and versatility in various applications, these carbide strips are elevating the standards of precision machining, mining, construction, woodworking, and more. As the industry continues to embrace innovative solutions, HR6A Tungsten Carbide Strips will undoubtedly play a vital role in shaping the future of industrial applications.